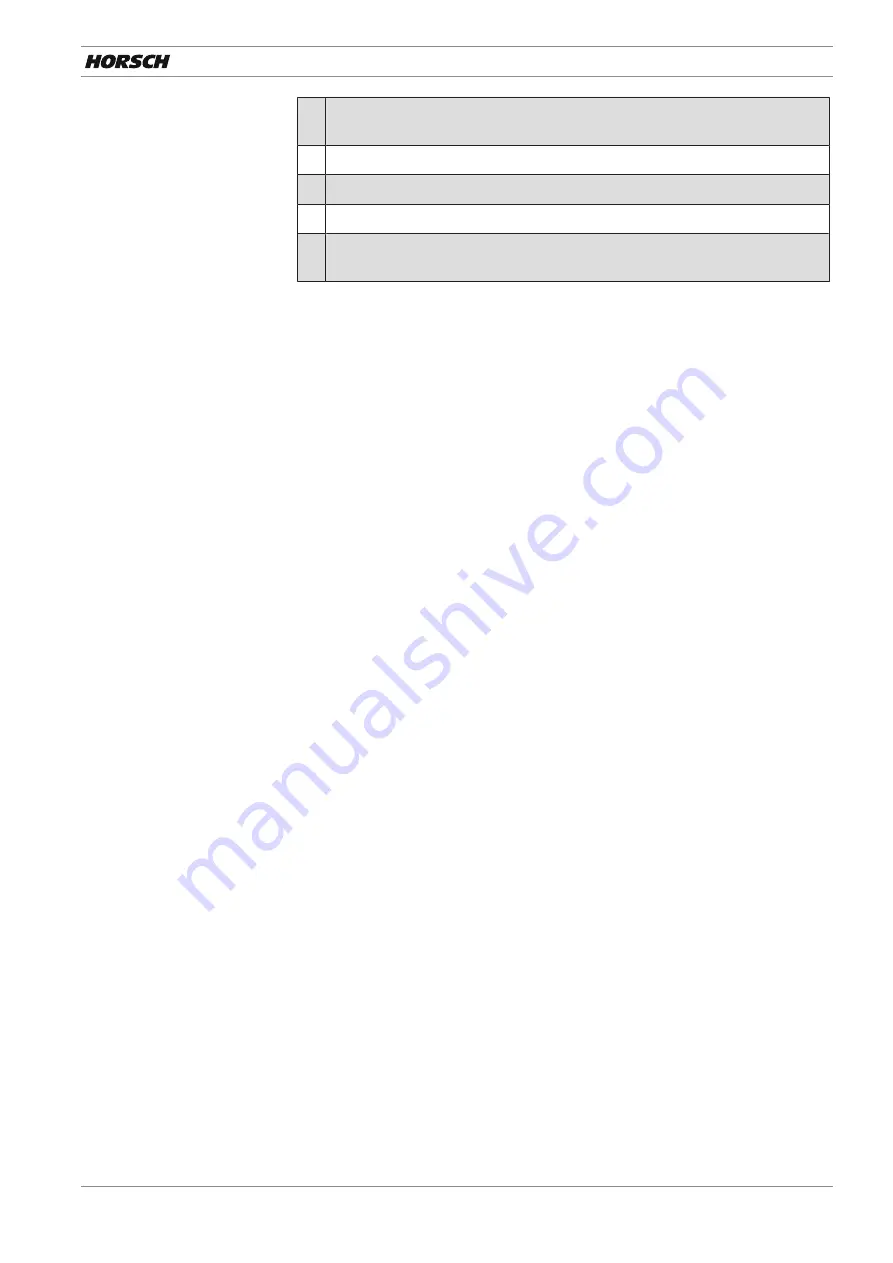
Diagnostics | 31
60043599 • 02 • 03/2021 • en
127
1
Current consumption of metering motor – terminal: MA15 – Master job com-
puter Pin 15
2
Current selection (frequency) – terminal: MA36 – Master job computer Pin 36
3
Speed of metering motor – terminal: MA36 – Master job computer Pin 36
4
Pulses of metering motor – terminal: MA36 – Master job computer Pin 36
5
Output value with selection of motor – terminal: MA15 – Master job computer
Pin 15
The figure shows the diagnostics screen using the example of a metering unit.
In addition, the terminals on the job computer with the respective pin number are
shown. MA – Master job computer, SL – Slave job computer