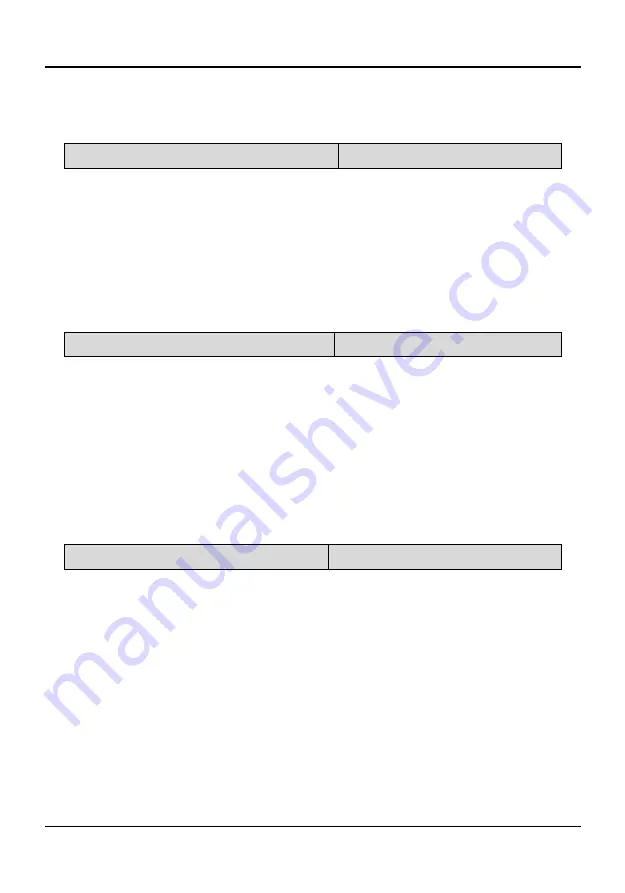
HV350 Mini Frequency Inverter User Manual
95
l
:
The parameter is not stored into
EEROM in communication.
Pd Faults and protection parameters
Pd.00
Motor overload protection mode
Setting range
:
0
,
1
,
2
0:
No protection
1:
Common motor protection
Since cooling conditions of common motor deteriorates at low speed,
please lower the motor‘s thermal protection threshold at this time.
2:
Variable frequency motor protection
Since the variable frequency motor applies forced air-cooling, the
protection parameters needn't be adjusted during low speed running.
Pd.01
Motor overload protection factor
Setting range
:
20.0%-150.0%
Heat dissipation becomes worse at low frequency, and high temperature will
reduce service life of the motor. Through setting threshold of the electronic thermal
overload relay, overload current and current limit will be proportionally adjusted.
When motor capacity is lower than that of the drive, this function is used
provide overheat protection for the motor.
When several motors are driven by the same variable speed drive, this function
is disabled. When display readings reaches 100%, overload protection will be
trigged
Pd.02
Over voltage stall selection
Setting range
:
0,1
Over voltage stall selection
0: Disabled;
1:Enabled
In inverter's Dec process, the actual motor speed may be higher than the
output synchronized speed of the inverter due to the load inertia. At this time, the
motor will feed the energy back to the inverter, resulting in the voltage rise on the
inverter's DC bus. If no measures being taken, tripping will occur due to over
voltage.
The overvoltage stall protection function is that during the Dec running, the inverter
detects the bus voltage and compares it with the stall overvoltage point defined by
PD.03. If the bus voltage exceeds the stall overvoltage point, the inverter will stop