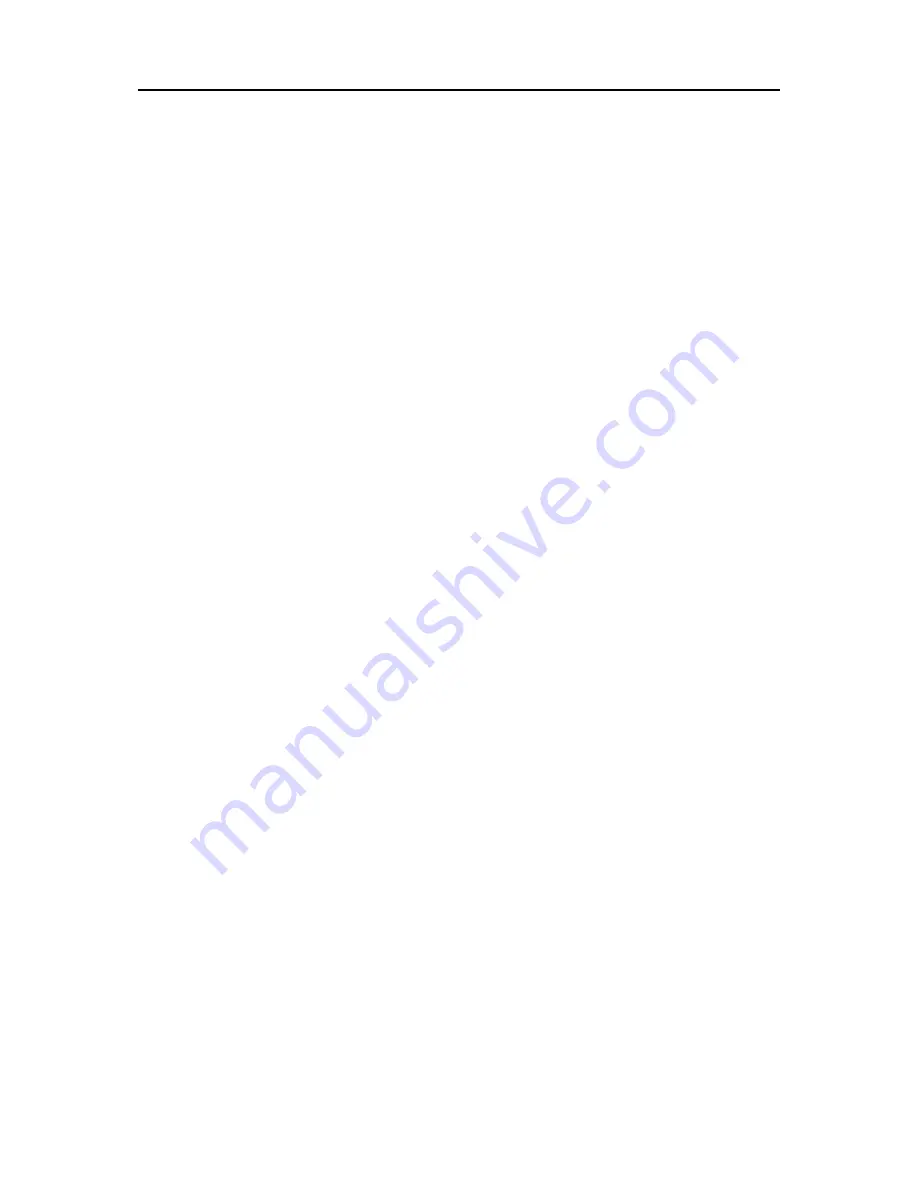
Configuration
18
Doc.Id. HMSI-168-91
Anybus X-gateway CANopen - PROFINET
Doc.Rev. 2.10
5.4 Configuration of the PROFINET Interface
5.4.1 Data Exchange
The first two bytes of the I/O area are used for the status/control word. Thus the slave interface ex-
changes up to 510 bytes of I/O data in each direction
The control and status words are used by the PROFINET master to control the CANopen network and
to read the status of the CANopen network. The contents of the control and status words are described
in “Data Exchange” on page 24
The amount of data that is exchanged as I/O Data is specified when configuring the CANopen master
interface. The data arriving from the CANopen master is completely transparent. The interpretation has
to be defined by the master of the slave interface, in this case PROFINET.
See also...
• “CANopen Master/Slave Configuration” on page 16
• “Data Exchange” on page 24
5.4.2 PROFINET IO Data
PROFINET is the open Industrial Ethernet standard for Automation from PROFIBUS International.
The PROFINET IO adapter provides PROFINET IO Soft Real-Time Communication.
As with most fieldbus systems, PROFINET makes a distinction between fast cyclical data, a.k.a. ‘IO Da-
ta’, and acyclical data, called ‘Record Data’. The Anybus X-gateway CANopen does however not sup-
port Record Data. PROFINET IO Data corresponds to the ‘I/O Data’ in the Anybus X-gateway
CANopen.
PROFINET IO Data is exchanged cyclically and is built up by I/O modules. In the case of the Anybus
X-gateway, the actual I/O module configuration is adopted from the I/O Controller/Supervisor, pro-
vided that their total size does not exceed the IO sizes specified in the Gateway Config Interface. The
modules are mapped to the Input- and Output Buffers in the order of their slot number.
The amount of I/O data to be exchanged is defined when configuring the CANopen master interface.
Summary of Contents for AB7307
Page 55: ......