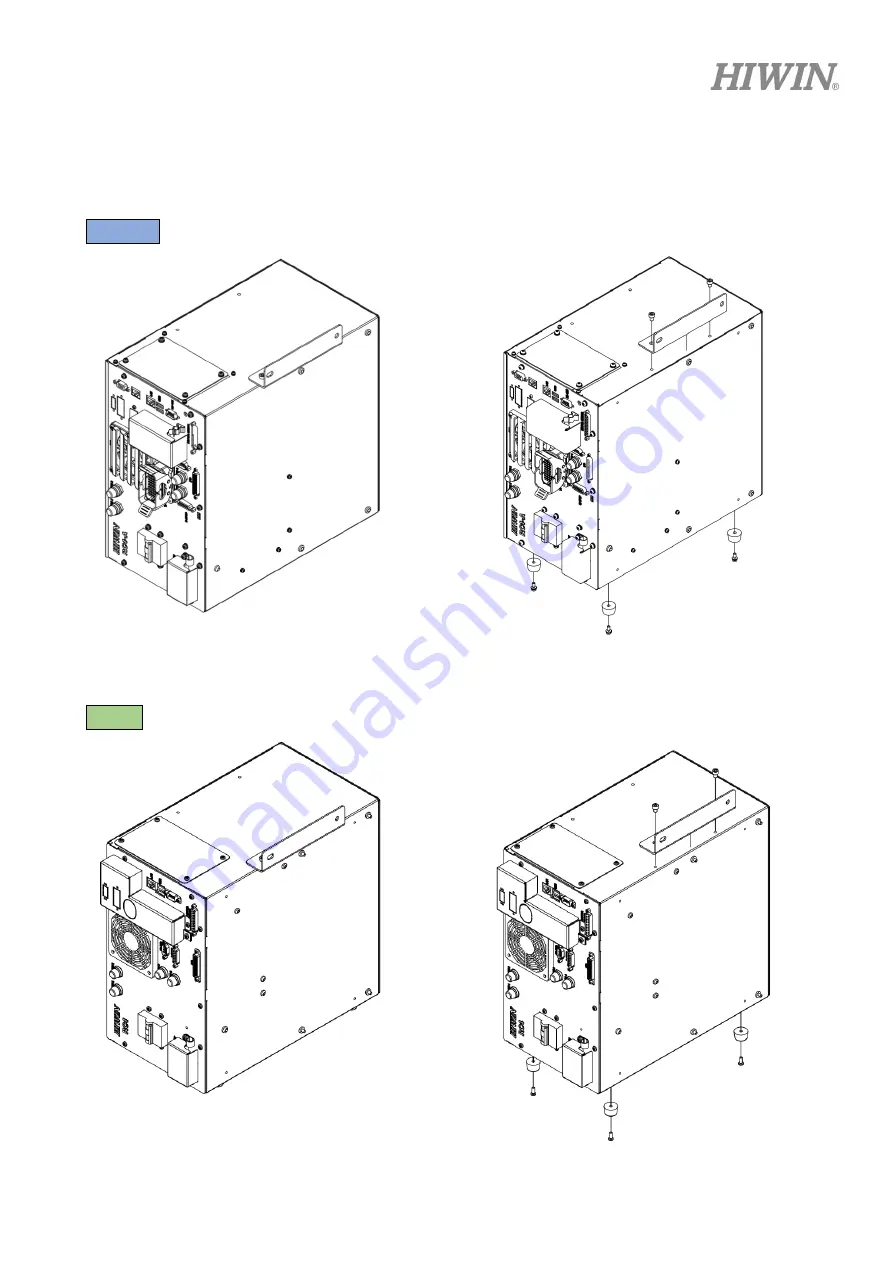
C21UE102-2110
37
Description:
Place the controller upright, you must remove a fixed sheet metal part and replace the plastic foot
from the bottom of the controller to the original side fixing point, as shown below. The plastic foot bolt is
M4X0.7PX10L.
RC4-A
:
Figure 2-4 upright installed of RC4-A controller and plastic foot position replacement
RC4
:
Summary of Contents for RC4
Page 1: ...www hiwin tw User Manual Robot Controller RC4 Series Original Instruction ...
Page 64: ...C21UE102 2110 62 D SUB 44P INPUT NPN OUTPUT NPN ...
Page 65: ...C21UE102 2110 63 D SUB 44P INPUT PNP OUTPUT PNP ...
Page 77: ...C21UE102 2110 75 ...
Page 79: ...C21UE102 2110 77 Figure 3 15 Digital output expansion model 32CH NPN configuration diagram ...
Page 80: ...C21UE102 2110 78 Figure 3 16 Digital output expansion model 32CH PNP configuration diagram ...