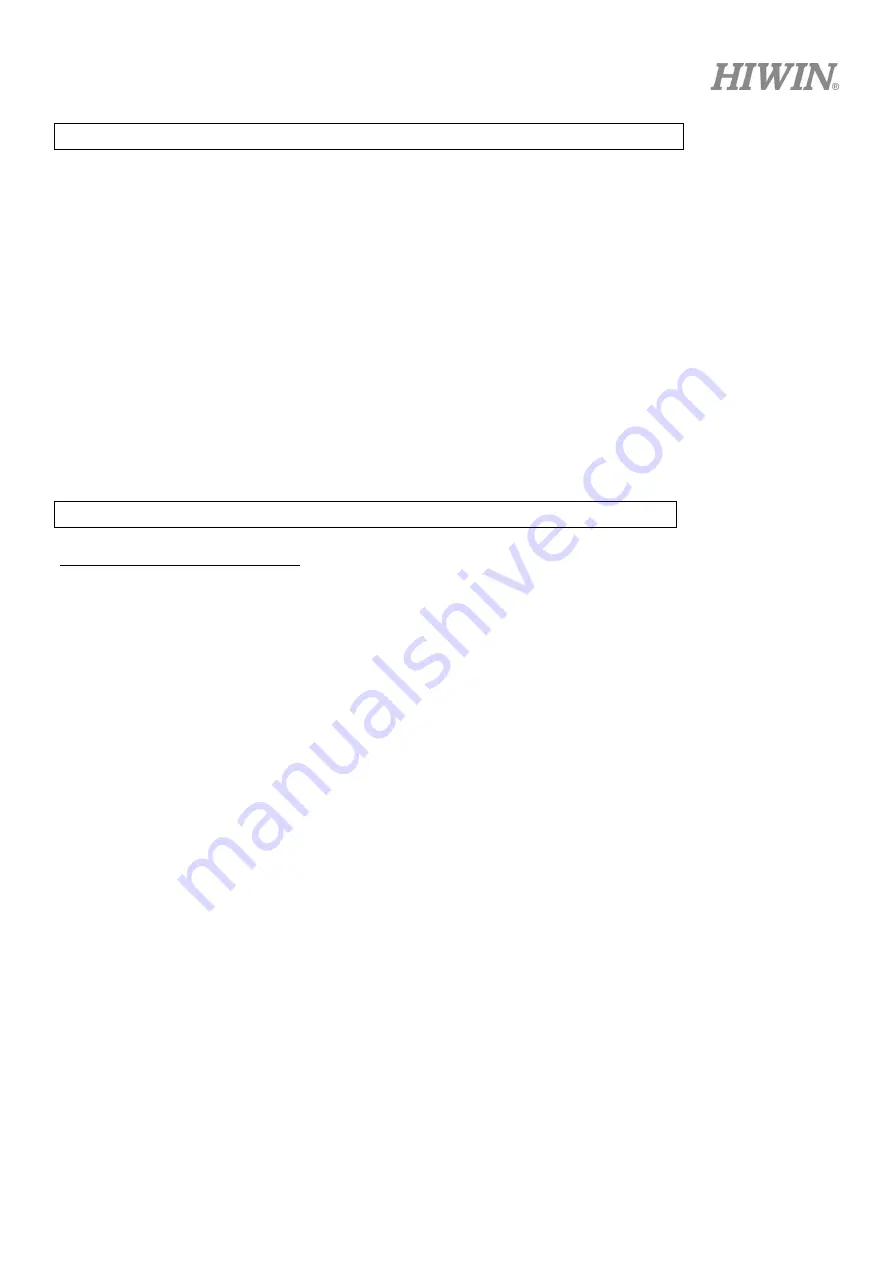
C21UE102-2110
11
Safe Guard Devices Description
The safe guard device must use the components approved by the safety regulations and set and plan
according to the relevant regulations.
The robotic arm system must be automatically activated to receive the safety signal. In the event of a
connection failure during automatic mode operation, an emergency stop must be triggered. When
reconnecting after disconnection, the device cannot be automatically started directly and must be started
manually. Manual slow running (T1) and manual fast running (T2) modes allow the guard not activate. A
method must be provided to confirm that no personnel are in the protected area when the automatic
mode is activated.
Users must strictly abide by the content description, otherwise it will cause serious casualties.
Temporary fences can be used during system installation and can be set according to ISO 10218-2
regulations
Stop Functions
Emergency Stop Description
Emergency stop related precautions
Confirm that the function is functioning normally every six months.
System integrators should provide emergency stop devices to ensure that the machine is operational
or that a hazardous situation exists.
At least one external emergency stop device is installed. Make sure that additional emergency stop
devices are available for use without or losing the teach pendant.
Provide interface to connect external emergency stop devices.
The emergency stop function can be triggered when the safety control system connected to the robot
arm is cut off.
The risk assessment should assess whether the emergency stop is not triggered when the robotic arm
control system is turned off and provides a response.
If a tool or other device connected to the robot is dangerous, it must be connected to the emergency
stop circuit on the equipment side.
Summary of Contents for RC4
Page 1: ...www hiwin tw User Manual Robot Controller RC4 Series Original Instruction ...
Page 64: ...C21UE102 2110 62 D SUB 44P INPUT NPN OUTPUT NPN ...
Page 65: ...C21UE102 2110 63 D SUB 44P INPUT PNP OUTPUT PNP ...
Page 77: ...C21UE102 2110 75 ...
Page 79: ...C21UE102 2110 77 Figure 3 15 Digital output expansion model 32CH NPN configuration diagram ...
Page 80: ...C21UE102 2110 78 Figure 3 16 Digital output expansion model 32CH PNP configuration diagram ...