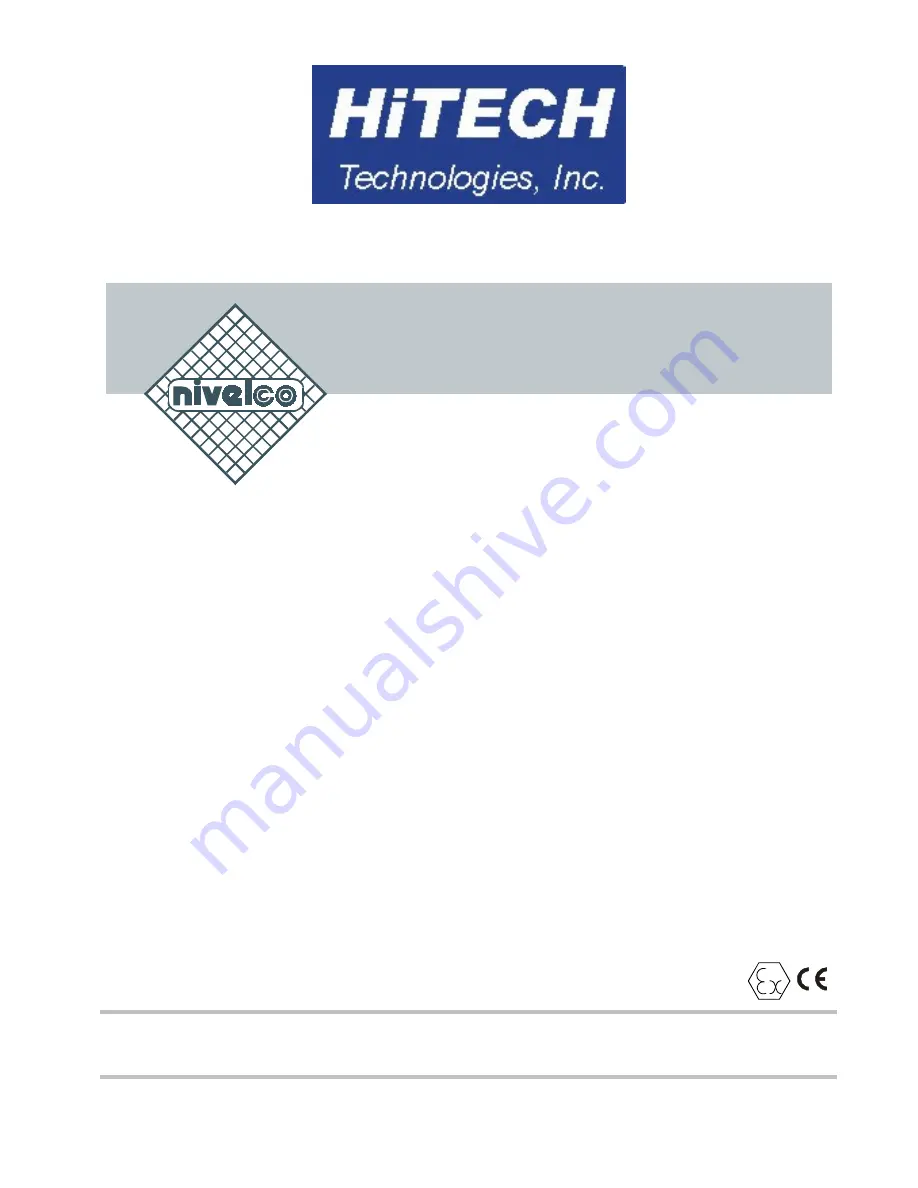
TÛV
-A 03 ATEX 0019X
♦
cbr2052a0600p_01
♦
36/1
N IV O C A P
C -2 0 0 , C -2 0 0 E x, C -3 0 0
tw o-w ire com pa ct ca pa cita nce
level tra nsm itter
INSTALLATION AND PROGRAMMING MANUAL
1
st
Edition
HiTECH/NIVELCO Co.
301 Oxford Valley Road, Bldg 505 Yardley, PA 19067-7711
Phone.: (215) 321-6012
♦
Fax: (215) 321-6067
e-mail:[email protected]
♦
www.nivelco.com