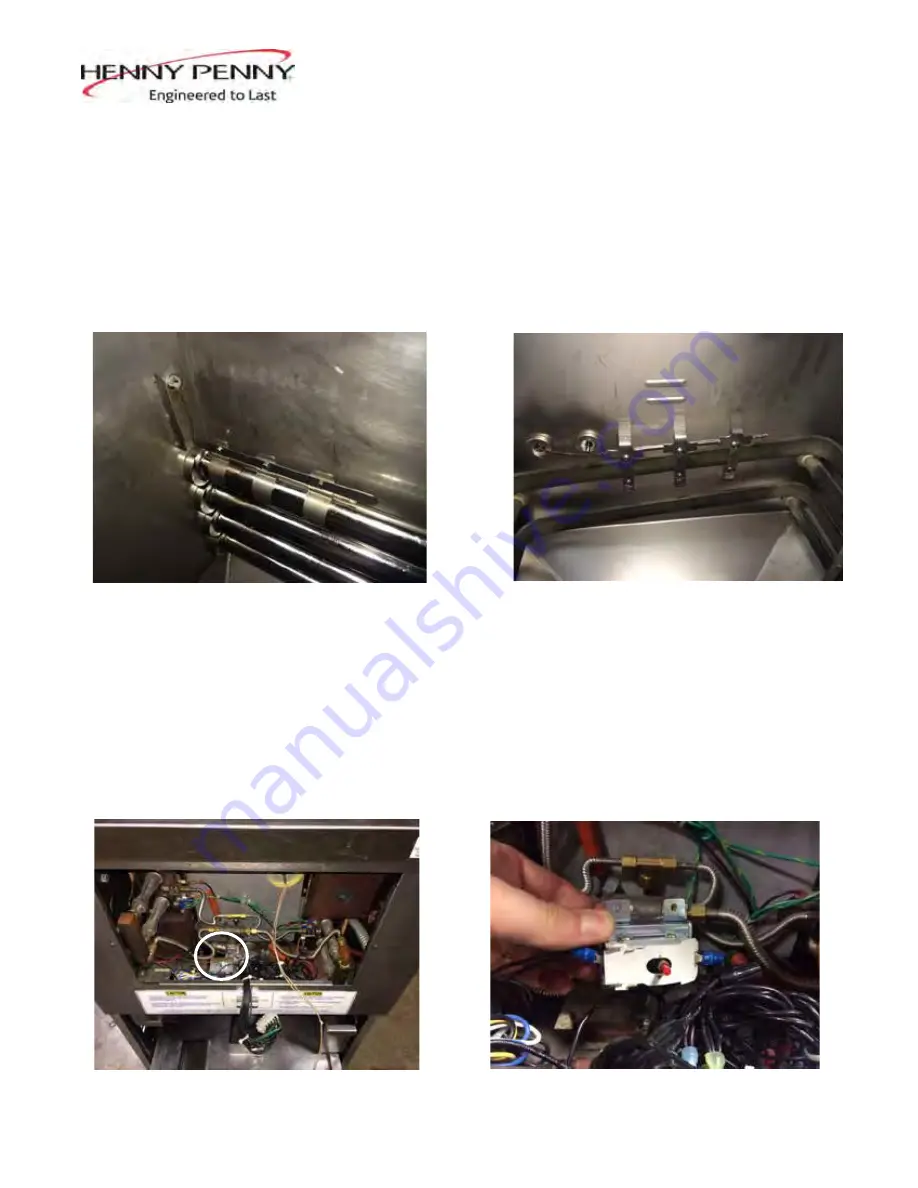
High Limit Inspection Rev. A Nov 2016
High Limit Inspection
- 8 Head PFE and PFG Fryers
Objective:
Ensure the high limit is securely installed and operational
Procedure
1. Drain oil to drain pan and visually inspect the high limit bulb and capillary tube mounted inside the fry pot.
Ensure the bulb is not dented, the capillary tube is not severed and the bracket matches figure 1. for a 690 or
figure 2. for a 580 / 590. If the capillary tube or bulb is damaged, stop. Take the fryer out of service until it is
replaced with #16738. If any hardware is damaged, or missing, replace hardware to match figures 1 and 2.
Figure 1. PFG-690
Figure 2. PFE-590
2. Press the red reset button on the high limit several times. If this button clicks each time it is pressed, stop.
Take the fryer out of service until the high limit can be replaced with part #16738 and make sure it gets wired
into the circuit upon replacement.
3.
With power disconnected from the fryer, lower the control board, remove the heat shield, and remove the two
mounting screws that secure the high limit body to the fryer. Remove the high limit and inspect to make sure
the high limit is properly wired into the circuit. Make sure both wires are
not
attached to the same terminal
on the high limit. Make sure these wires are not damaged, and also make sure the two wires have not been
removed from the high limit and connected together. Figures 3 & 4 shows a properly wired high limit (690 high
limit shown). If bypassing of the high limit is found, or any damaged wiring is found, stop. Take the fryer out of
service until the wiring is corrected and high limit replaced if defective..
Figure 3.
Figure 4.
Inspection 28
Rev A
Summary of Contents for PFG-691
Page 1: ...Henny Penny Pressure Fryer Model PFG 691 TECHNICAL MANUAL...
Page 2: ......
Page 52: ...Model 691 2 34 SN FH001JC ABOVE Aug 2004...
Page 53: ...Model 691 2 35 SN FH001JC ABOVE Aug 2004...
Page 54: ...Model 691 2 36 SN FH001JC ABOVE Aug 2004...
Page 55: ...Model 691 2 37 BELOW SN FH001JC March 2004...
Page 56: ...Model 691 2 38 BELOW SN FH001JC March 2004...
Page 57: ...Model 691 2 39 BELOW SN FH001JC March 2004...
Page 58: ...Model 691 2 40 BELOW SN FH001JC March 2004...
Page 60: ......
Page 62: ...Model 691 3 2 FIGURE 3 1 FRAME COVER ASSEMBLY Oct 2004...
Page 68: ...Model 691 3 8 FIGURE 3 6 LID COVER ASSEMBLY March 2007...
Page 70: ...Model 691 3 10 FIGURE 3 7 DRAIN PAN FILTER ASSEMBLY Aug 2010...
Page 72: ...Model 691 3 12 FIGURE 3 8A FILTER PUMP ASSEMBLY SN LH028JC BELOW Aug 2010...
Page 74: ...Model 691 3 14 FIGURE 3 8B FILTER PUMP ASSEMBLY SN LH029JC ABOVE Oct 2004...
Page 77: ...Model 691 3 17 FIGURE 3 10 GAS BURNER ASSEMBLY May 2005...
Page 79: ...Model 691 3 19 FIGURE 3 11 GAS PIPING CONTROLS Dec 2009...
Page 84: ...Model 691 3 24 FIGURE 3 15 DEADWEIGHT SOLENOID ASSY SN AP0802029 ABOVE Aug 2010...
Page 87: ...Model 691 3 27 FIGURE 3 16B STEAM BOX HOSE ASSEMBLY SN AP0802028 BELOW Aug 2010...
Page 89: ...Model 691 3 29 FIGURE 3 17 FLUE ASSEMBLY BLOWER SN AP0802028 BELOW Dec 2009...
Page 93: ...Model 691 3 33 FIGURE 3 18 SOLENOID VALVE ASSEMBLY Sept 2005...
Page 95: ...Model 691 3 35 FIGURE 3 19 FRYPOT DRAIN PIPING Oct 2008...
Page 97: ...Model 691 3 37 FIGURE 3 20 LIFT BEAM SHROUDS SN AP0802028 BELOW Aug 2010...
Page 99: ...Model 691 3 39 FIGURE 3 21 COUNTERWEIGHT PULLEY SYSTEM SN AP0802028 BELOW Aug 2010...
Page 139: ...Inspection 12 Rev A...
Page 140: ...Inspection 12 Rev A...
Page 141: ...Inspection 12 Rev A...
Page 144: ...Inspection 15 Rev A...
Page 145: ...Inspection 16 Rev A...
Page 146: ...Inspection 16 Rev A...
Page 159: ...Inspection 24 Rev A Figure 2 1...
Page 160: ...Inspection 24 Rev A Figure 2 2...
Page 183: ......