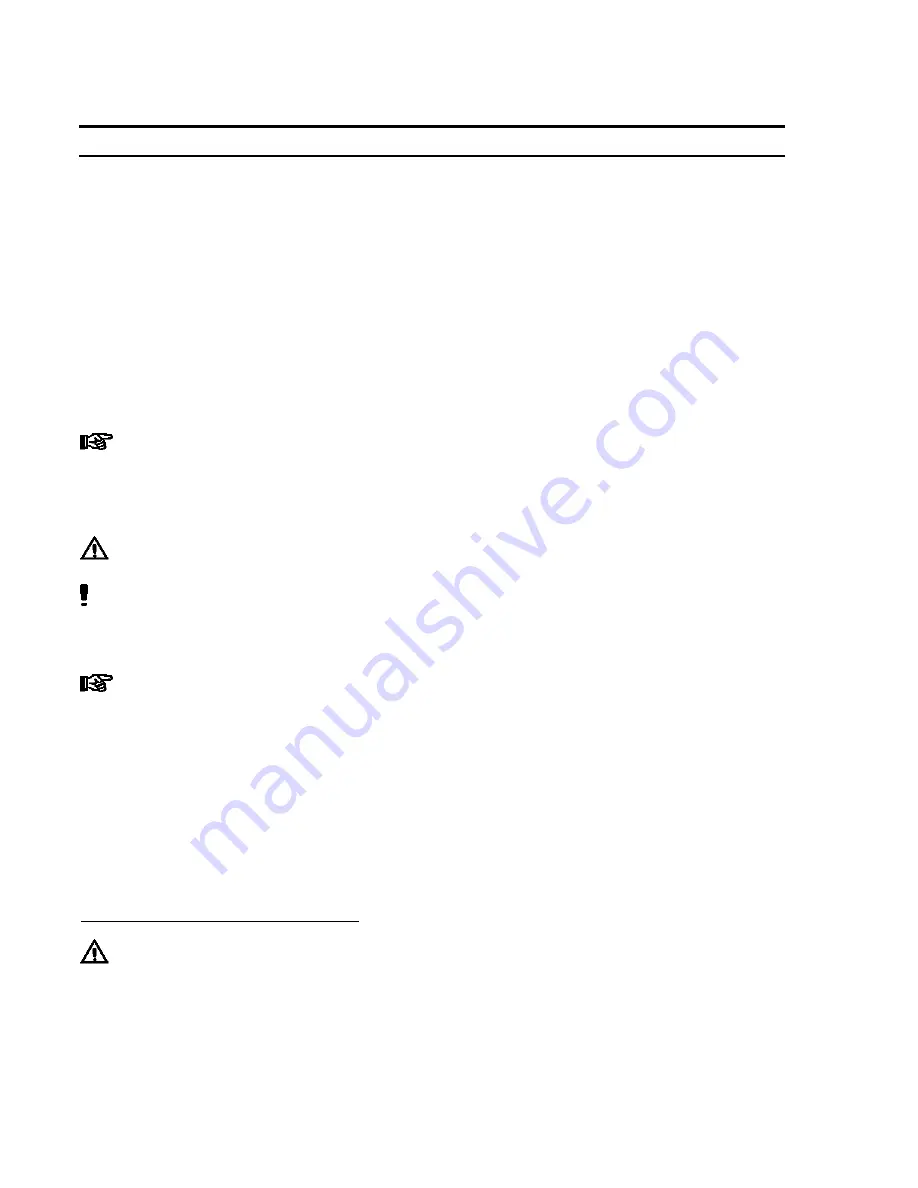
4. Installation
4.1 Unpacking and Inspection
Carefully remove the system from its shipping carton and inspect it for any signs of damage. Any
damage should be reported immediately to the carrier. Refer to the list of supplied parts (see
page 4) and compare to the contents. Report any missing or damaged parts promptly to the Loctite
customer service department at 1-800-LOCTITE (562-8483).
4.2 Installation
The Loctite
®
Single Rotary Dispense Station will arrive completely assembled. To install:
1. Plug the power cord into the back of the controller and into the wall socket.
Notice:
This unit has an autoranging power supply that can be used with either 110 or
220V and 50 or 60 Hz.
2. Connect the foot switch to the back of the controller.
3. Connect the air input line using ¼” outer diameter pneumatic tubing (not supplied).
4. Turn on the air input. This must be a minimum of 80 psi and a maximum of 125 psi.
Warning!
When the air is connected, the slide may retract. Be sure to keep your hands
and other objects clear of the slide before connecting the air.
Caution!
Clean, dry, filtered air must be used. If it is not, the solenoids in the controller
will be fouled over time. If the required air quality is not achieved, install a Loctite filter
regulator. In the US order a 5
µ
m filter using Part Number 985397. In Europe or Asia,
order a 10
µ
m filter using Part Number 97120.
Notice:
If the vacuum setting is open you will hear air leaking from the “VACUUM
EXHAUST” on the back panel of the controller. This is normal when using the vacuum
suckback feature for syringe dispensing. If you would like to stop the air exhaust, turn the
vacuum off by turning the “VACUUM” knob on the controller clockwise until it stops.
4.3 Dispenser Integration
The Loctite
®
Single Rotary Dispense Station is designed to use syringes, cartridges, single acting
valves and double acting valves. To integrate these dispense systems please use the following
instructions:
4.3.1 Syringe or Cartridge Dispensing
Warning!
Before integrating any dispensing equipment, please press the “EMERGENCY
STOP” button. This will dump the pressure to all pneumatic devices and allow the slide to
advance eliminating the potential for pinch points. It will also allow the syringe, cartridge or
valve to be installed when the slide is advanced minimizing the potential for crashes.
9