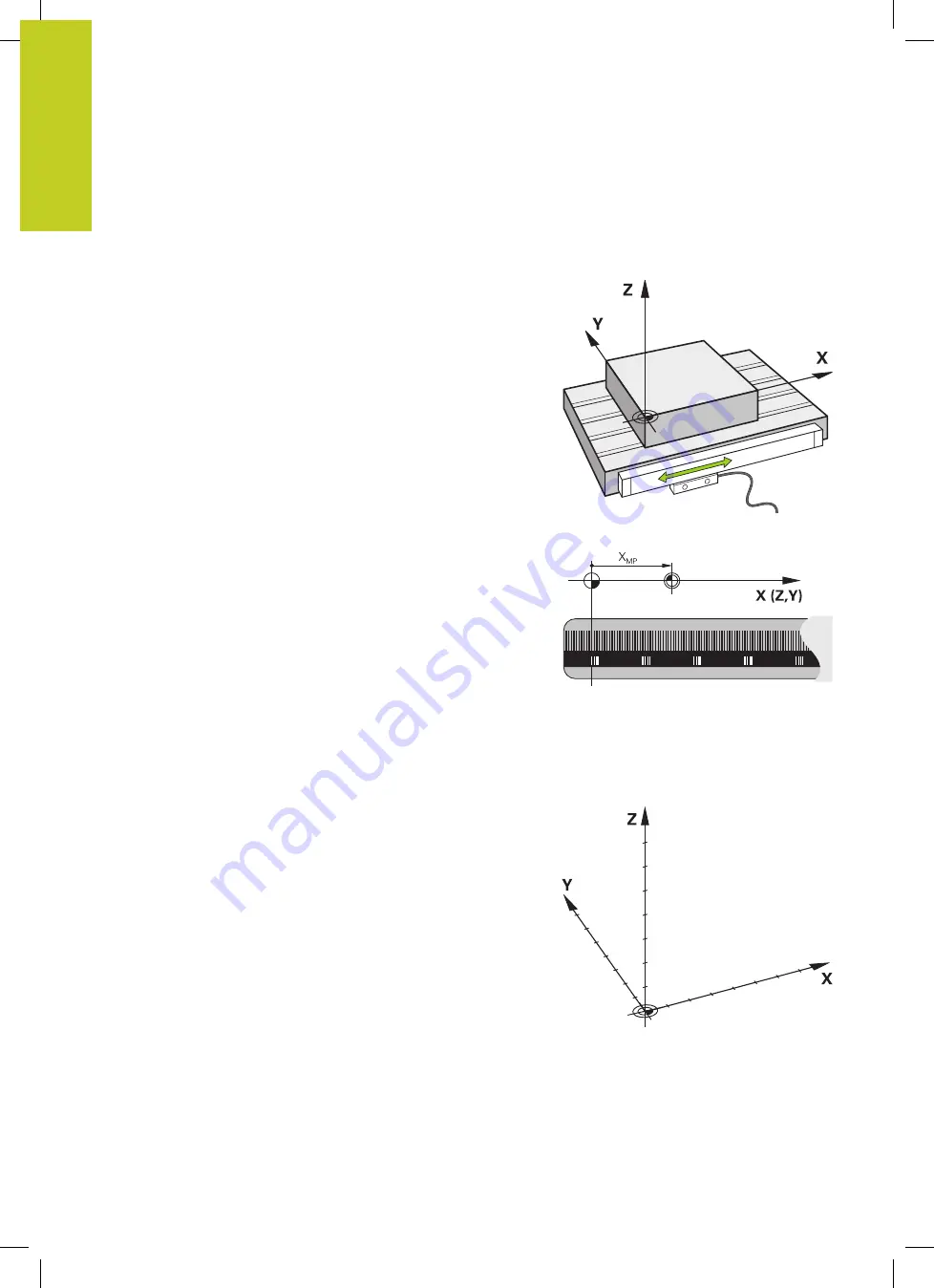
Programming: Fundamentals, file management
3.1
Fundamentals
3
82
TNC 320 | User's Manual
HEIDENHAIN Conversational Programming | 3/2014
3.1
Fundamentals
Position encoders and reference marks
The machine axes are equipped with position encoders that
register the positions of the machine table or tool. Linear axes are
usually equipped with linear encoders, rotary tables and tilting axes
with angle encoders.
When a machine axis moves, the corresponding position encoder
generates an electrical signal. The TNC evaluates this signal and
calculates the precise actual position of the machine axis.
If there is a power interruption, the calculated position will no
longer correspond to the actual position of the machine slide.
To recover this association, incremental position encoders are
provided with reference marks. The scales of the position encoders
contain one or more reference marks that transmit a signal to the
TNC when they are crossed over. From that signal the TNC can
re-establish the assignment of displayed positions to machine
positions. For linear encoders with distance-coded reference
marks, the machine axes need to move by no more than 20 mm,
for angle encoders by no more than 20°.
With absolute encoders, an absolute position value is transmitted
to the control immediately upon switch-on. In this way the
assignment of the actual position to the machine slide position is
re-established directly after switch-on.
Reference system
A reference system is required to define positions in a plane or in
space. The position data are always referenced to a predetermined
point and are described through coordinates.
The Cartesian coordinate system (a rectangular coordinate system)
is based on the three coordinate axes X, Y and Z. The axes are
mutually perpendicular and intersect at one point called the datum.
A coordinate identifies the distance from the datum in one of these
directions. A position in a plane is thus described through two
coordinates, and a position in space through three coordinates.
Coordinates that are referenced to the datum are referred to
as absolute coordinates. Relative coordinates are referenced to
any other known position (reference point) you define within the
coordinate system. Relative coordinate values are also referred to
as incremental coordinate values.
Summary of Contents for TNC 320
Page 4: ...Controls of the TNC 4 TNC 320 User s Manual HEIDENHAIN Conversational Programming 3 2014 ...
Page 5: ...Fundamentals ...
Page 16: ...Contents 16 TNC 320 User s Manual HEIDENHAIN Conversational Programming 3 2014 ...
Page 43: ...1 First Steps with the TNC 320 ...
Page 63: ...2 Introduction ...
Page 81: ...3 Programming Fundamentals file management ...
Page 124: ......
Page 125: ...4 Programming Programming aids ...
Page 152: ......
Page 153: ...5 Programming Tools ...
Page 180: ......
Page 181: ...6 Programming Programming contours ...
Page 232: ......
Page 233: ...7 Programming Data transfer from DXF files or plain language contours ...
Page 251: ...8 Programming Subprograms and program section repeats ...
Page 267: ...9 Programming Q Parameters ...
Page 337: ...10 Programming Miscellaneous functions ...
Page 357: ...11 Programming Special functions ...
Page 379: ...12 Programming Multiple Axis Machining ...
Page 406: ......
Page 407: ...13 Manual operation and setup ...
Page 462: ......
Page 463: ...14 Positioning with Manual Data Input ...
Page 468: ......
Page 469: ...15 Test run and program run ...
Page 497: ...16 MOD functions ...
Page 525: ...17 Tables and overviews ...