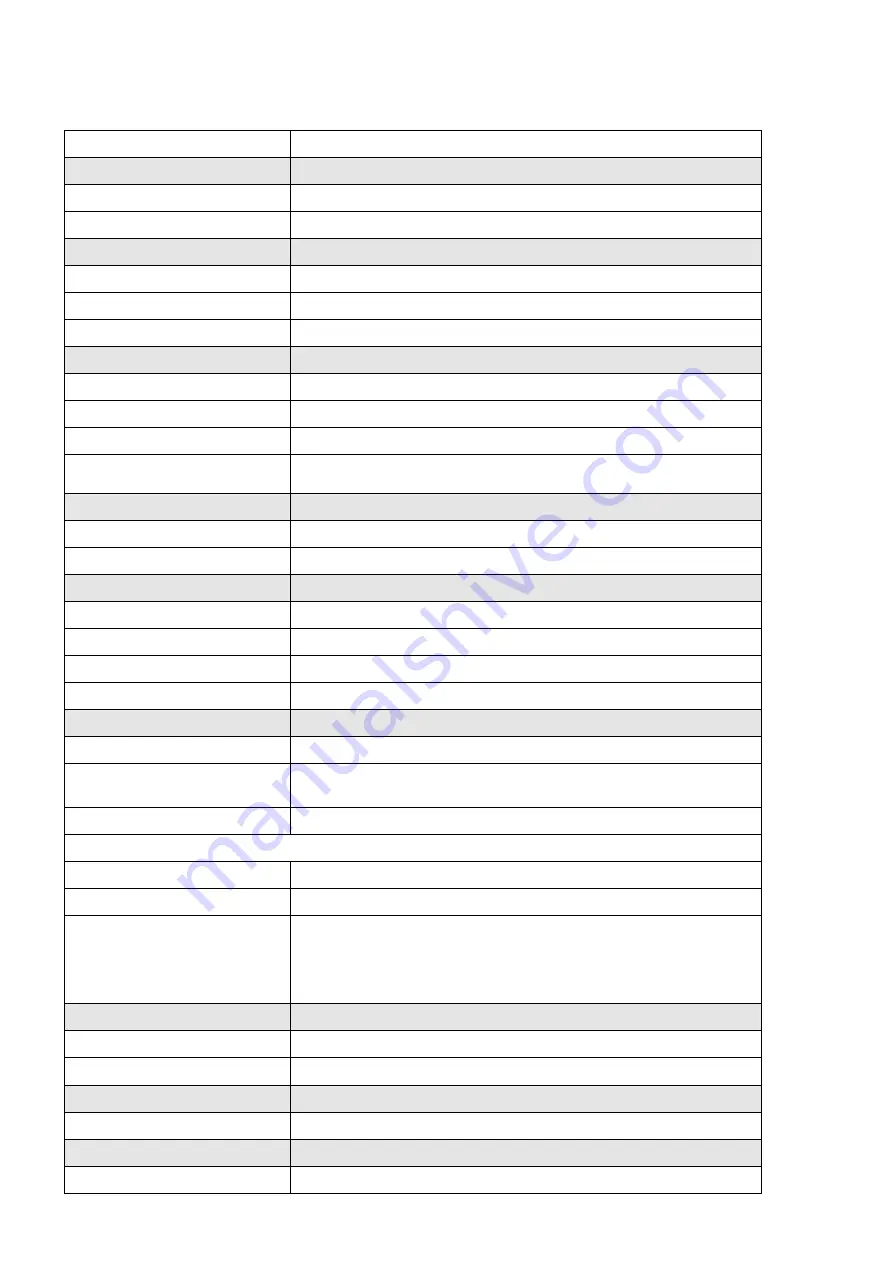
Bedienungsanleitung H1280
HASCO hot runner 43
6 Technical data
Operation and display
7” touchscreen, resistive
Housing
Housing material
Galvanised steel
Protection type
IP 20
Environmental conditions
Ambient temperature
Max. 35°C
Humidity
0…90% rel. humidity, no condensation
Storage temperature
-25…+75 °C
Mains supply
Supply voltage
3x 400 V AC, N, PE
Switchable to
3x 230 V AC, PE
Tolerance
+ 5% / -15%
Power consumption
when idle
7 W + 5 W per power board
Control voltage
Internal control voltage
+24VDC
Protection
1 x 2A medium delay (5 x 20mm)
Thermocouple inputs
Thermocouple
FeCuNi (TYPE J) 0..700° switchable to: NiCr-Ni (TYPE K) 0..700°
Cold junction compensation
Integrated
Resolution
0.1 K
Accuracy
< 1K
Load outputs
Bistable, electrically insulated
per zone
1x heating, 230V AC switching
Control time (phase angle
/pulse package
10 ms at 50 Hz – 8.3 ms at 60 Hz
Current per zone
max. 16 A with 80% switch-on duration per zone
Caution: observe the total load capacity of the electrical connection cable
Minimum load
100 W
Signal shape
Pulse operation/phase control (automatic or manual selection)
Protection
2-pole; 6.3 x 32 mm
Internal: SIBA TYPE 16A T
External SIBA TYPE 16A GRL
Only use these fuse types!
Alarm notification outputs
3x relay contact
Potential-free for max. 250 VAC
Maximum current
4 A for cos
= 1; 2A for cos
= 0.5
Digital inputs
Insulated, potential-free
16 – 30 V DC
Data interfaces
Ethernet
CAT 5