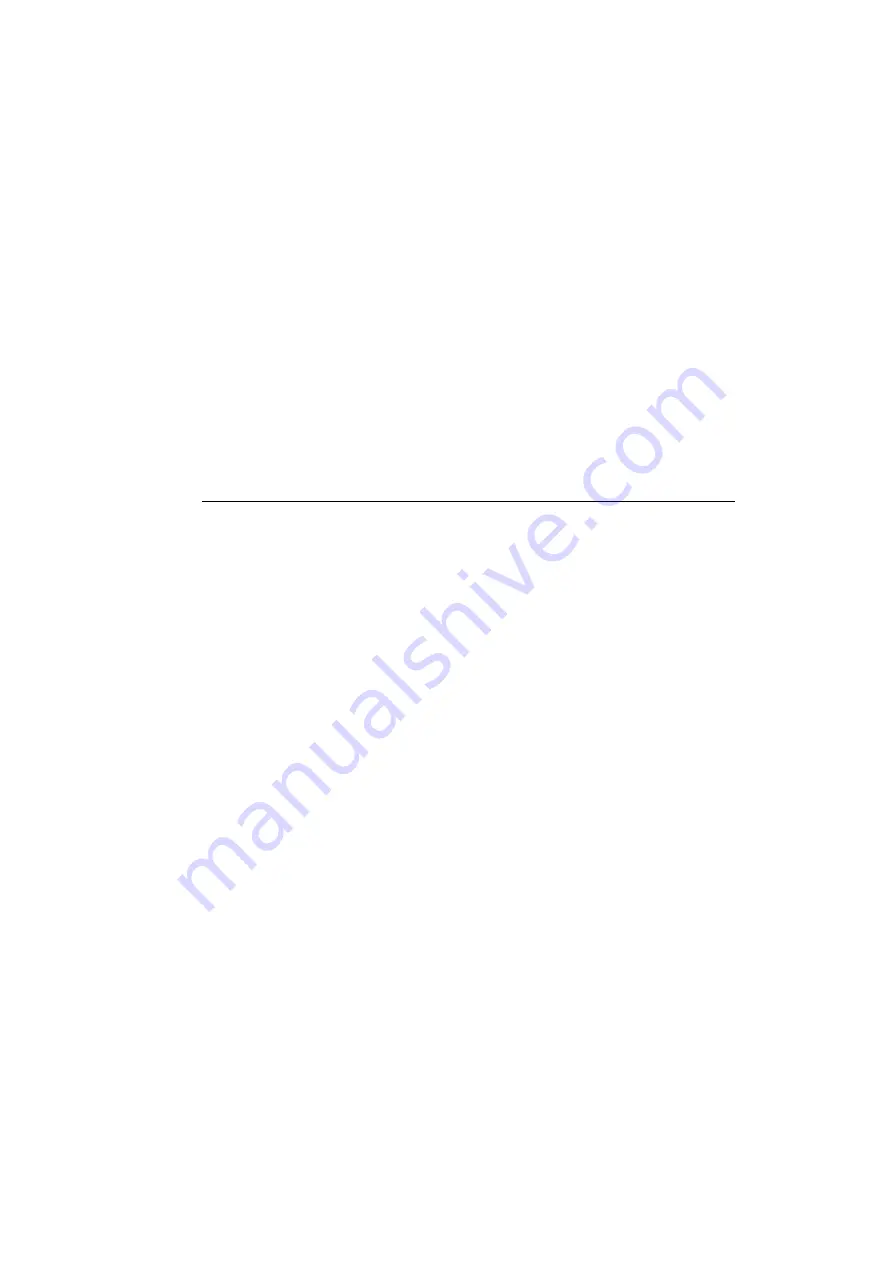
Chapter 4
Options
This chapter explains the options available for the SHA series actuator.
4-1 Options ··············································································· 94
Chapter 4
Options
This chapter explains the options available for the SHA series actuator.
4-1 Options ··············································································· 94