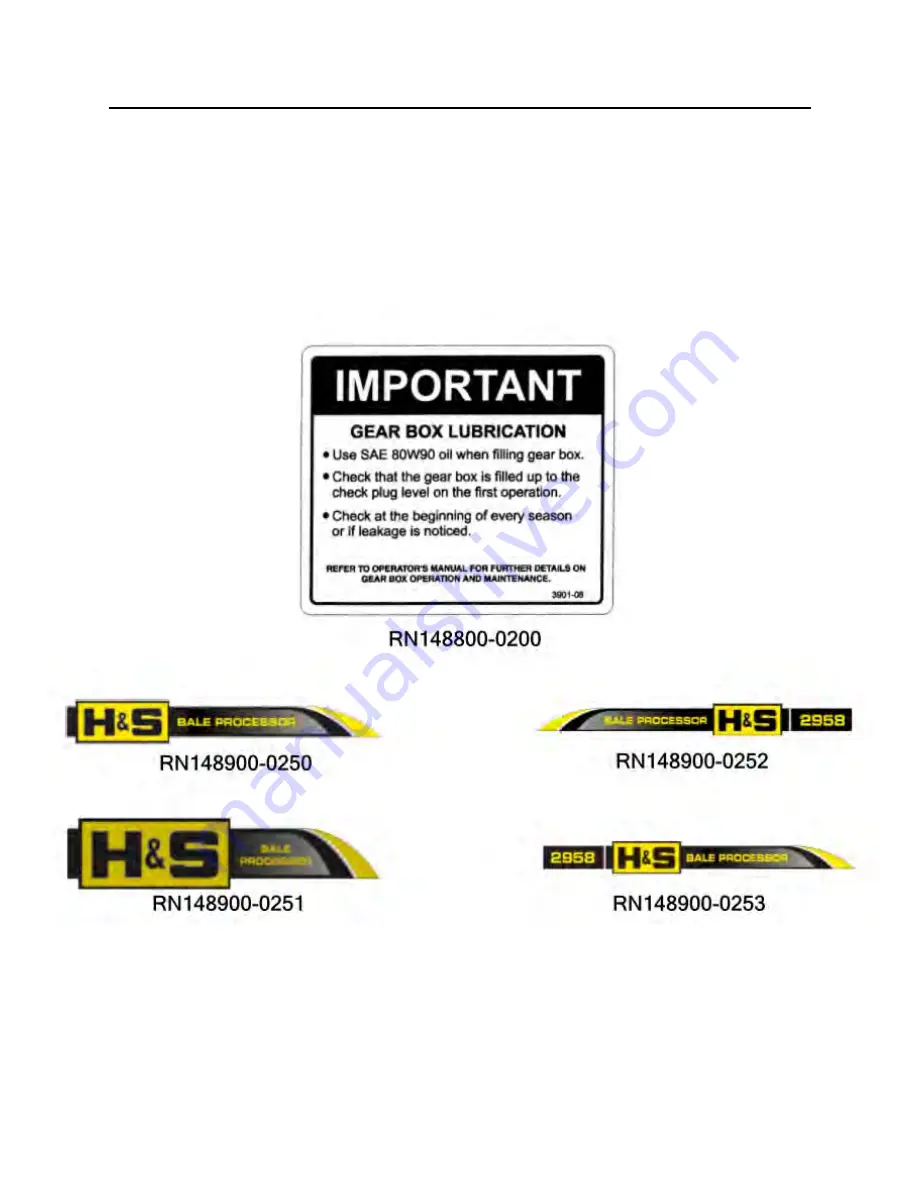
3 DECAL
3.2 Information Decal Locations
The types of informational and operational decals on this machine and their
locations are shown in the following illustrations.
- 3.4 -
REMEMBER - If safety signs have been damaged, removed, become illegible or parts have
been replaced without safety signs, new signs must be applied. New safety signs are availa-
ble from your authorized dealer.
L
ൺඌඍ
R
ൾඏංඌංඈඇ
NOV 2016
VK
L
ൺඌඍ
R
ൾඏංඌංඈඇ
AUG 2019
KK
Summary of Contents for 2958
Page 2: ......
Page 6: ...PAGE INTENTIONALLY LEFT BLANK...
Page 14: ...3 2 3 Safety Decal Locations...
Page 15: ...3 3 3 Safety Decal Locations...
Page 17: ...3 5 3 2 Information Decal Locations...
Page 36: ...5 5 5 4 PTO...
Page 43: ...7 3 Bolt Torque 38 7 2...
Page 44: ...7 3 7 4 Overall Dimensions...
Page 45: ...7 4 7 4 Overall Dimensions...
Page 46: ...7 5 7 4 Overall Dimensions...
Page 47: ...PAGE INTENTIONALLY LEFT BLANK...
Page 52: ...N 10 1...
Page 53: ......
Page 54: ...H S MFG CO Products approved for the FEMA SEAL OF QUALITY...