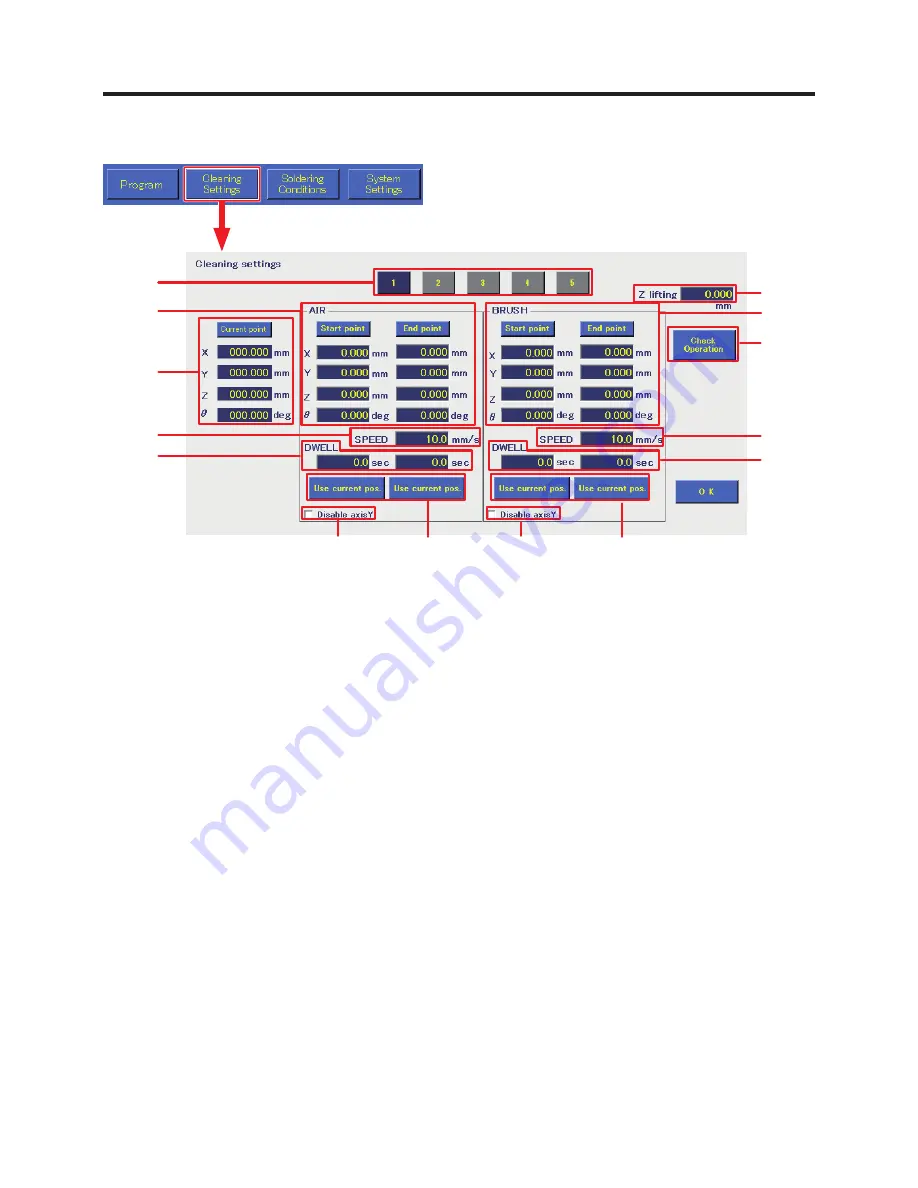
47
7-1-2 Cleaning Settings
Cleaning Settings Screen
(1) Cleaning Settings
(top screen)
Button for setting cleaning settings. Up to 5 settings can be set.
(2) Cleaning number
Cleaning program number. Up to 5 cleaning programs can be set.
(3) Current point
Shows the current tip position.
(4) AIR
Sets air cleaning settings.
(5) BRUSH
Sets brush cleaning settings.
(6) SPEED
Sets the movement speed when moving the tip from Start point
→
End point
→
Start point.
(7) DWELL
Sets the respective cleaning times while waiting at the start point and end point during cleaning.
(Settable range: 0.0 – 60.0 sec.)
(8) Use current pos.
Sets the current coordinates as the start point or end point.
(9) Disable axis Y
When checked, forces the Y axis to not move during cleaning regardless of the input coordinate
values.
(10) Z lifting
The Z axis lift coordinates to be used during cleaning. These values will be given priority during
cleaning regardless of the
Z axis lift coord.
set in the top screen.
For details on Z axis lift behavior, refer to “7-2-2 Z Axis Lift” (p. 60).
(11)
Check operation
Checks the operation of the set cleaning behavior.
(2)
(3)
(6)
(6)
(7)
(7)
(11)
(10)
(8)
(8)
(1)
(4)
(5)
(9)
(9)