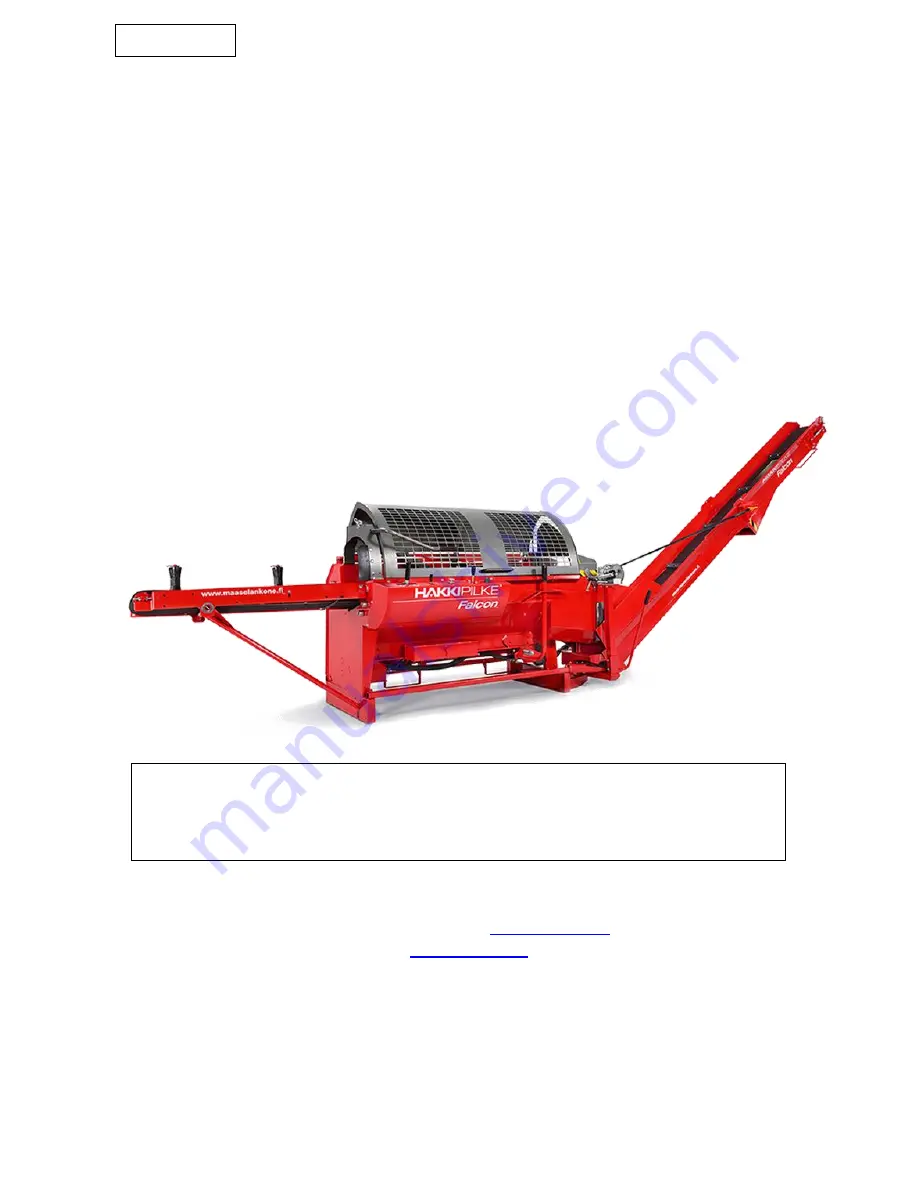
1 / 41
Hakki Pilke 35 Falcon
Translation
Version 10
Hakki Pilke
Falcon 35
FIREWOOD PROCESSOR
– Instructions for assembly, operation and maintenance
– EC Declaration of Conformity
– Safety instructions
– Guarantee terms
MAASELÄN KONE OY
Valimotie 1, FI-85800 Haapajärvi
tel.+358 (0)8 7727300,
info@
hakkipilke
.fi
www.hakkipilke.fi
ENGLISH
The operator must read and understand these
instructions before operating the machine!