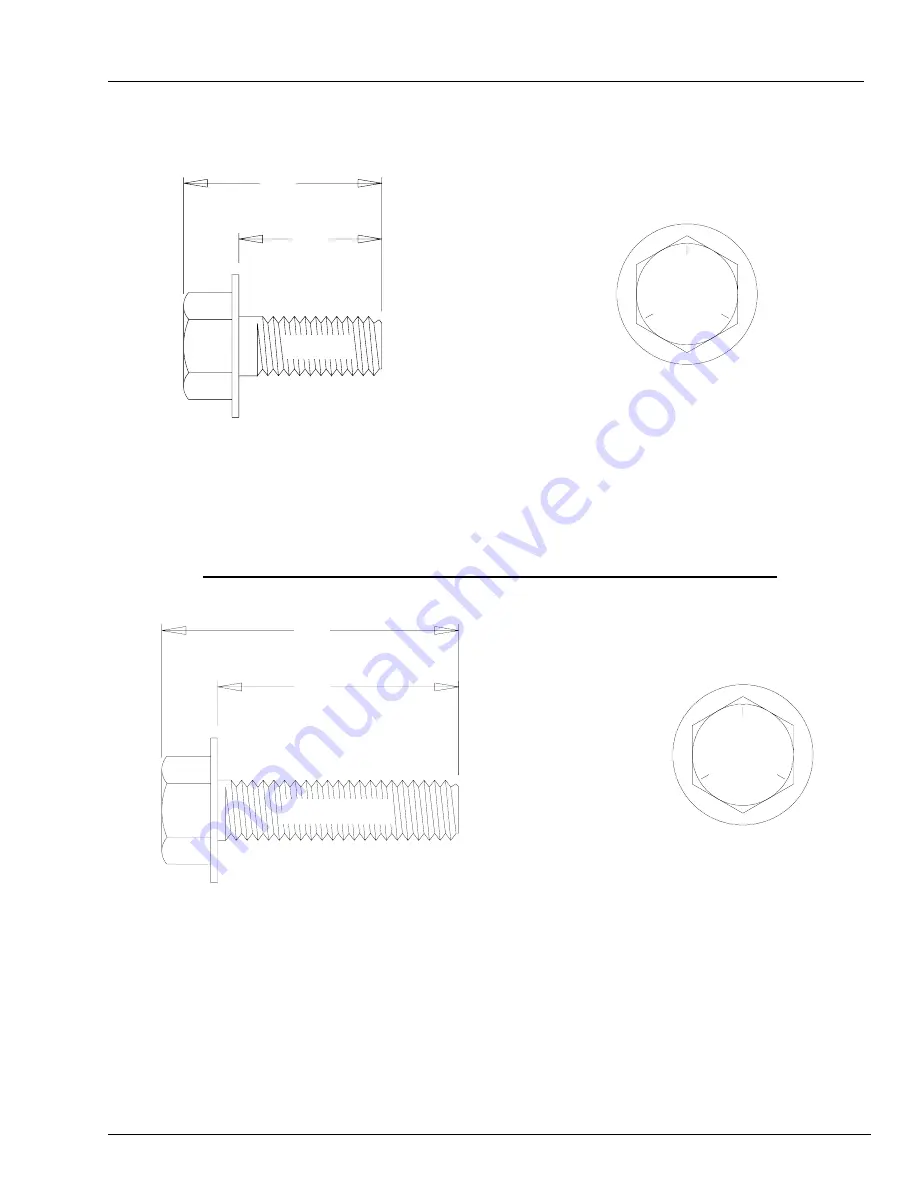
17
24' Batch & Autoflow
This bolt is used to connect horizontal and vertical seams for 13 gage and thinner sidewall sheets to each
other, and to bolt the stiffeners to the sidewall sheets. It is also used in attaching roof panels to the top
sidewall sheet and attaching roof panels and flashing to the center collar.
Refer to Top Dry Tank Bolting Requirements for Complete Bolt Usage
Figure #6
.950"
.750"
Top View
Side View
Grade 5
1.250"
1.437"
This bolt is primarily used to connect roof panels together where they overlap. It is also used at the
bottom of the flat bottomed bins to attach the base angle to the sidewall sheet. A small number of these
are provided for joints and FC-42076 splice plates for the stiffeners to sidewall connection.
.3125" x 1.250"
pre-assembled
with a steel backed
neoprene washer.
Top View
Grade 5
TOP DRY TANK BOLTING
.3125" x .750"
pre-assembled
with a steel
backed neoprene
washer.
S-275
Side View
S-277