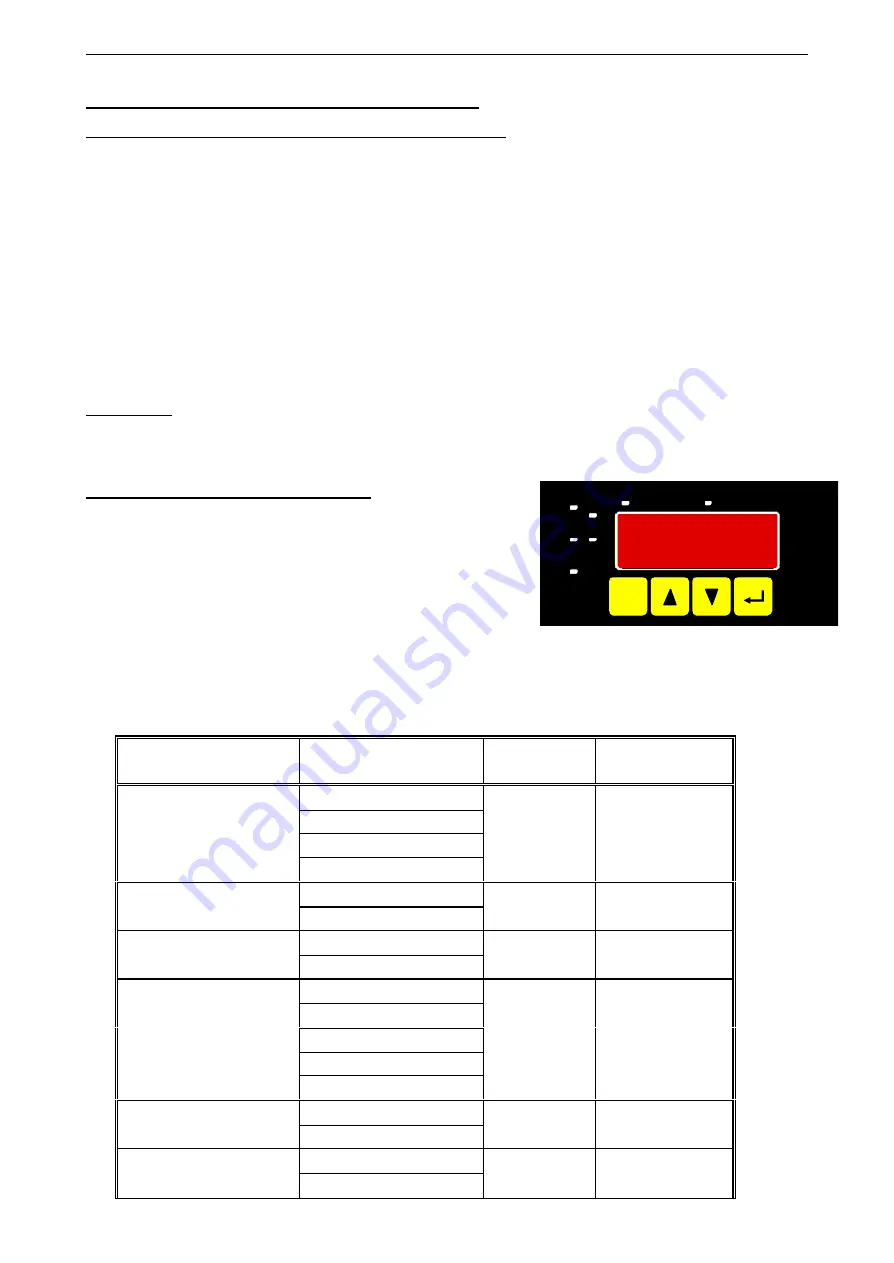
E32.0.02.6C-04
Manual for connection and operation of the
GIA 2000 / AAG and GIR 2002 / AAG
page 10 of 30
4. Configuration of the measuring input
General description and notes to the operating of the menu
By means of
button 1
you can go to the next parameter.
Additionally a given changing in the parameter setting can be confirmed by this button and the new value
will be saved. Afterwards it will be changed to the parameter view again.
By means of
button 2
and
3
you can go from the parameter view to the parameter setting and adjust its
value there.
Hint:
The buttons 2 and 3 are featured with a ‘roll-function‘. When pressing the button once the value will be raised
(button 2) by one or lowered (button 3) by one. When holding the button pressed for longer than 1 sec. the value
starts counting up or down, the counting speed will be raised after a short period of time.
The device also features a ‘overflow-function‘, when reaching the upper limit of the range, the device switches to
the lower limit, vice versa.
By means of
button 4
a
given changing will be cancelled in the parameter setting. The changing will be dis-
carded and the former parameter value will be preserved.
In the parameter view button 4 closes the menu.
Please note:
If you don’t press any button for more than 10 sec. in the parameter setting, the adjustment will
be cancelled, the changing discarded and it will be changed to the parameter view. If you don’t
press any button for more than 60 sec. in the menu, the menu will be automatically closed.
4.1. Selecting an input signal type
-
Turn the device on and wait until it completed its built-in seg-
ment test.
-
At the same time press the pushbutton on the rear side (but-
ton 5) and button 2 for >2 seconds.
The device displays “
InP
“ ('INPUT').
-
Use button 2 or button 3 to select the input signal
(see table below).
-
Validate the selection with button 1. The display will show “
InP
“ again.
Depending on the selected input signal, additional configurations will be needed.
Input type
Signal
to select as
input
proceed in chapter
0 – 10 V
0 – 2 V
0 – 1 V
Voltage signal
0 – 50 mV
U
4.2
4 – 20 mA
Current signal
0 – 20 mA
I
4.2
Pt100
RTD
Pt1000
t.rES
4.3
NiCr-Ni
(type K)
Pt10Rh-Pt
(type S)
NiCrSi-NiSi
(type N)
Fe-CuNi
(type J)
Thermocouples
Cu-CuNi
(type T)
t.tc
4.3
TTL-signal
Frequency
Switch-contact NPN, PNP
FrEq
4.4
TTL-signal
Rotation
Switch-contact NPN, PNP
rPn
4.5
ON/SP
SET
min.
OFF/Hy.
1
2
max.
ALARM
Scale
Analog
CAL
Scale
Analog
CAL
ON/SP
SET
min.
OFF/Hy.
1
2
max.
GIR/GIA
ALARM
SET
1
2
3
4