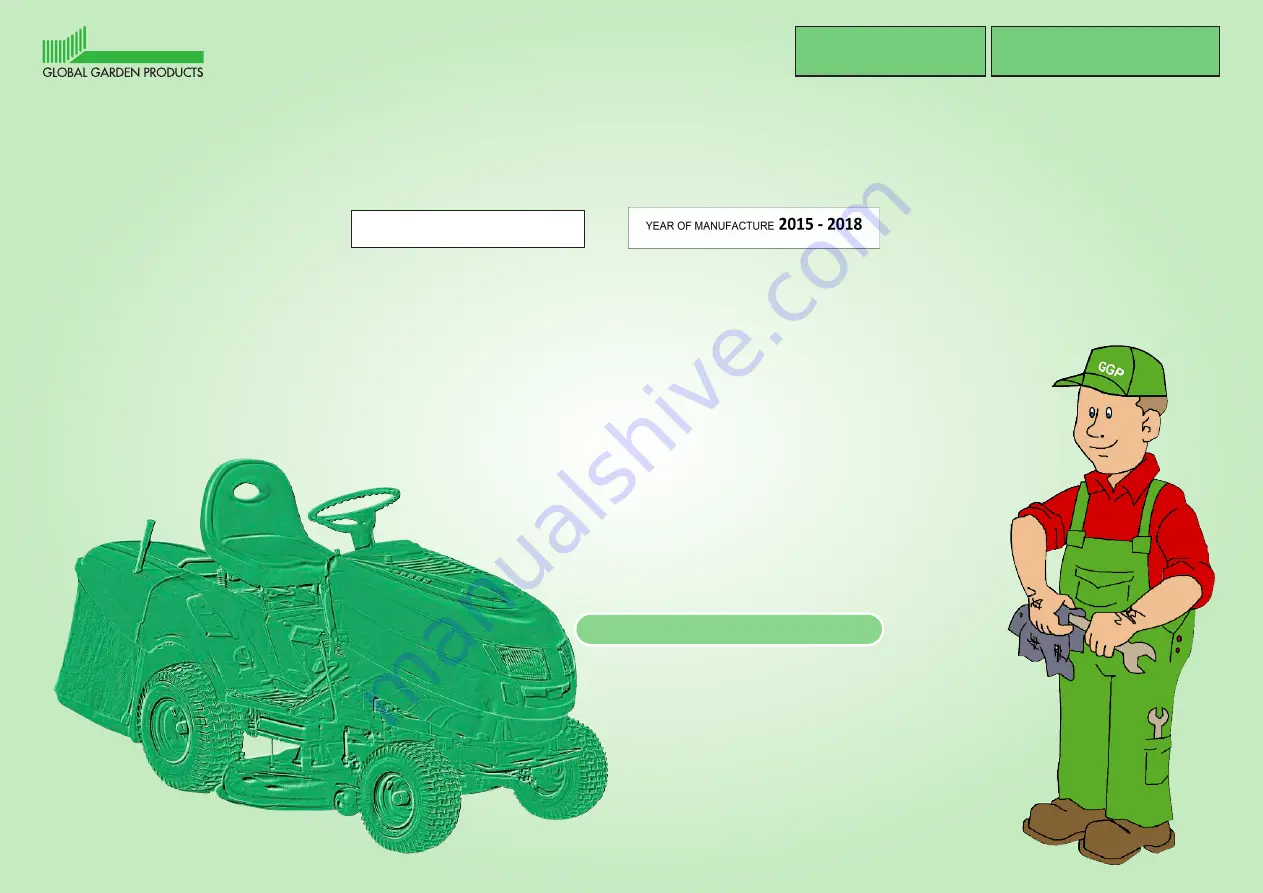
WORKSHOP MANUAL
WORKSHOP MANUAL
Rel. 2.1
YEAR OF MANUFACTURE
2016
The Manufacture reserves the right to make any improvements to the product of a technical or commercial nature
that may be necessary. There may be, therefore, differences between the various series of machines and that
described here, though the basic features and various repair methods will remain the same.
© by GLOBAL GARDEN PRODUCTS - No use of the illustrations or duplication, reproduction or translation, even
partial, of the texts in this document may be made without explicit authorization.
All brands, names, logos and trademarks mentioned
belong to their respective owners.
IMPORTANT NOTICE
- The information contained herein
is intended for Service Operations and professionals only,
able to competently perform the operations described here-
in, using the appropriate equipment in order to safeguard
security and performance of the machine. The manufacturer
is not liable for damages or injuries arising from operations
performed by individuals or inadequate facilities.
N...102 Hy
N...102