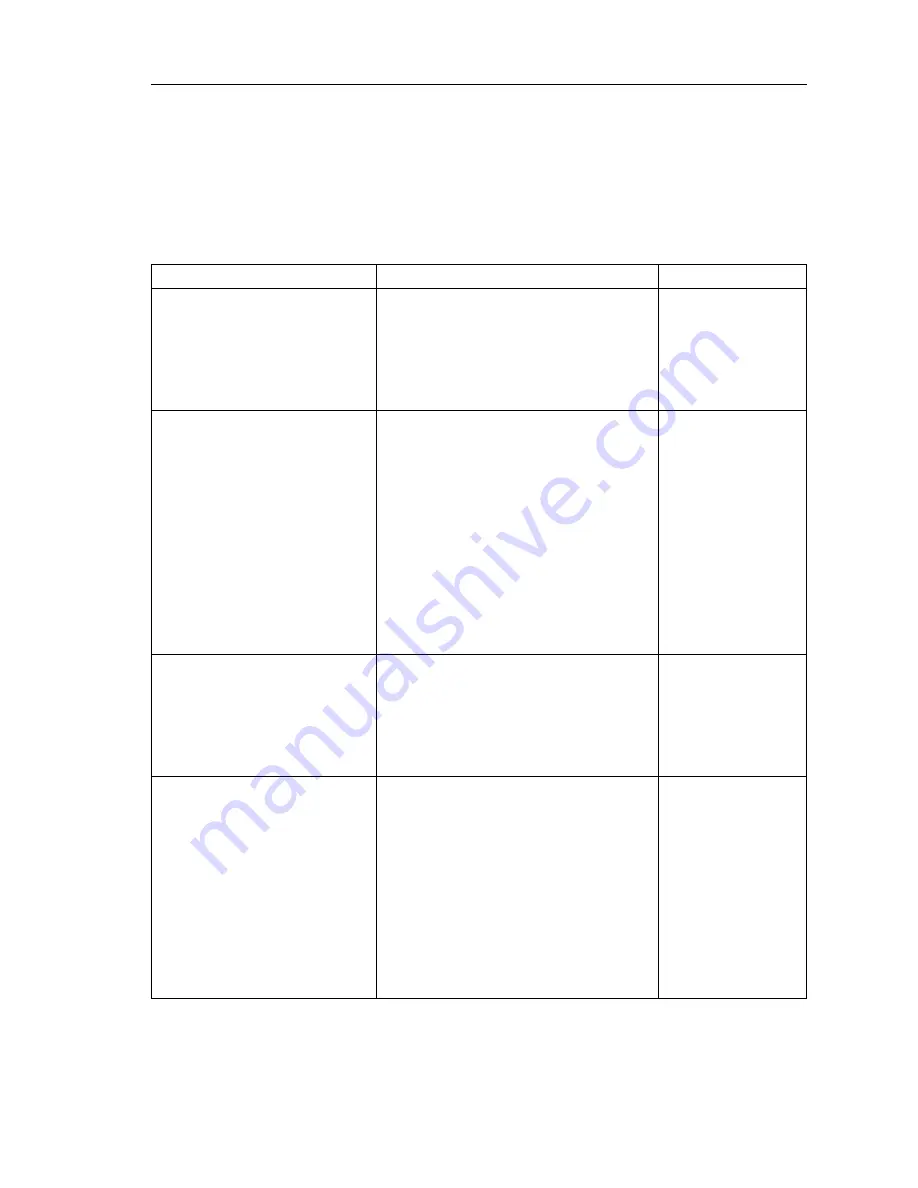
Brake--Remove malfunction
Remove malfunction
Malfunction phenomenon table
Use following table to help you find the reason of malfunction, the number in table indicates the preferred
sequence of possible reasons of malfunction. Please check every part by sequence, if necessary, change
this part.
Malfunction phenomenon
Possible malfunction part
Reference page
1. Brake system (leaking oil).
-
The height of brake pedal is too
2. Brake system (entering air).
135
low or brake pedal is loose.
3. Piston oil seal (abraded or damaged).
141, 144
4. Brake main pump (invalid)
138
5. Vacuum booster lever (adjusted badly)
138
1. Brake pedal free travel (too small).
136
2. Parking brake handle travel (adjusted badly).
154
3. Parking brake pull cable (lag).
156, 158
4. Brake block (damaged or distorted).
141, 144
Brake lag
5. Piston (locked).
141, 144
6. Piston (freezed).
141, 144
7. Tensility or return spring (invalid).
161
8. Vacuum booster lever (adjusted badly).
138
9. Vacuum boosting system (vacuum leakage).
138
10. Brake main pump (invalid).
138
1. Piston (locked).
141, 144
2. Brake block (oil dirt).
141, 144
Brake offset
3. Piston (freezed).
141, 144
4. Brake disk (scratched).
141, 144
5. Brake block (abraded or distorted).
141, 144
1. Brake system (leaking oil).
2. Brake system (entering air).
135
3. Brake block (abraded).
141, 144
4. Brake block (damaged or distorted).
141, 144
Brake pedal is too hard to make power lack.
5. Brake block (oil dirt).
141, 144
6. Brake block (sclerosesed).
141, 144
7. Brake disk (scratched).
141, 144
8. Vacuum booster lever (adjusted badly).
138
9. Vacuum boosting system (vacuum leakage).
138
133
Summary of Contents for FC
Page 1: ......
Page 2: ......
Page 302: ...Light Side turning light Side turning light Components Side turning light 291 ...
Page 409: ...Electric glass lifter Electrical schematic diagram Electric glass lifter 398 ...
Page 412: ...Electric rearview mirror Electrical schematic diagram Electric rearview mirror 401 ...
Page 413: ...Reversing radar system Electrical schematic diagram Reversing radar system 402 ...
Page 414: ...Safety airbag system Electrical schematic diagram Safety airbag system 403 ...
Page 418: ...Combination instrument Electrical schematic diagram Combination instrument 407 ...