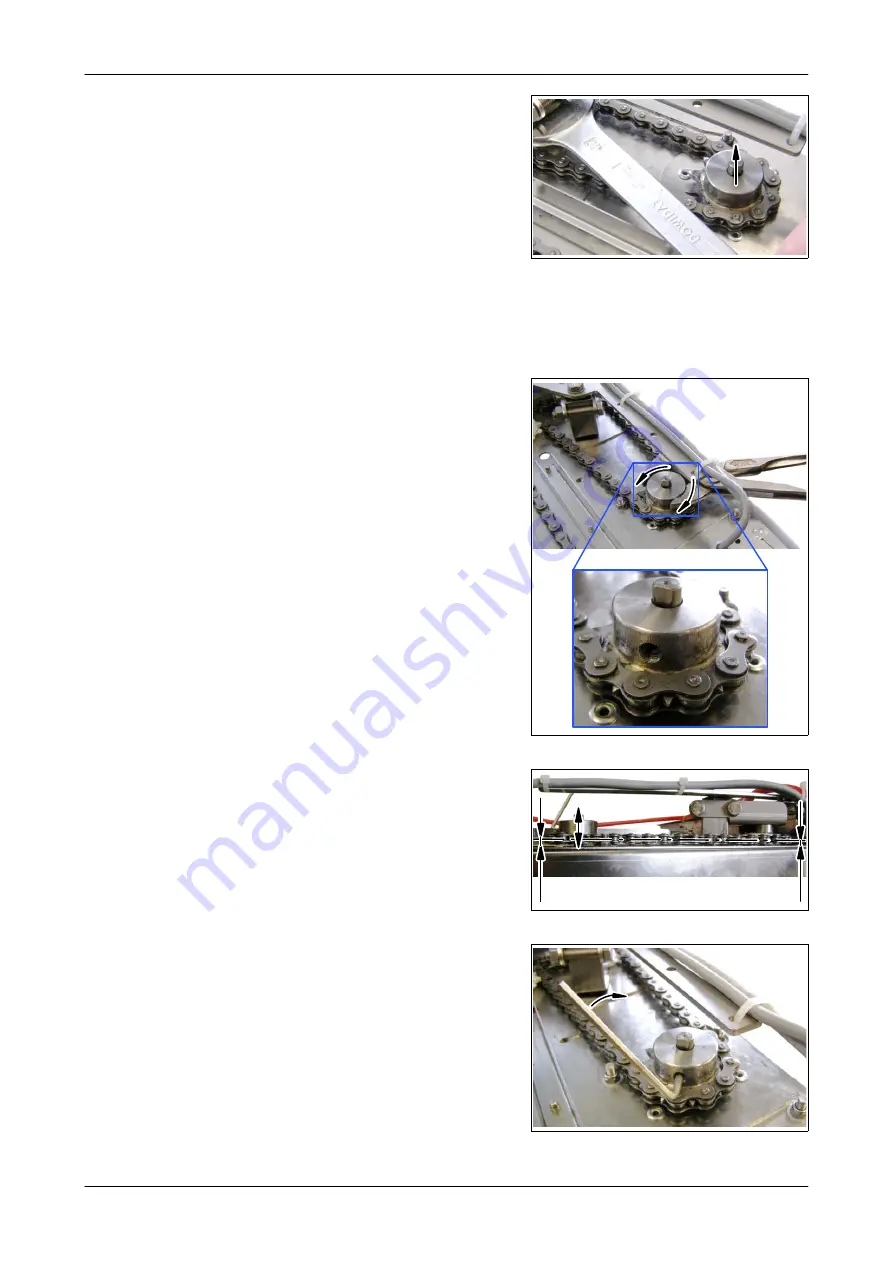
Maintenance
Inspections and preventive maintenance
7821-9001-005
01. October 2019
● Remove the sprocket from the drive
shaft.
● Replace any defective parts (e.g. chain or sprockets).
● Place sprocket with chain on the drive shaft, loosening the chain with the
spanner.
● Turn the sprocket until the threaded pin
is pointing towards the flat surface of the
drive shaft.
● Position the sprocket at the required
height on the drive shaft.
=
=
● Tighten the threaded pin on the
sprocket (drive) with a spanner.
● Re-assemble the sampling device.