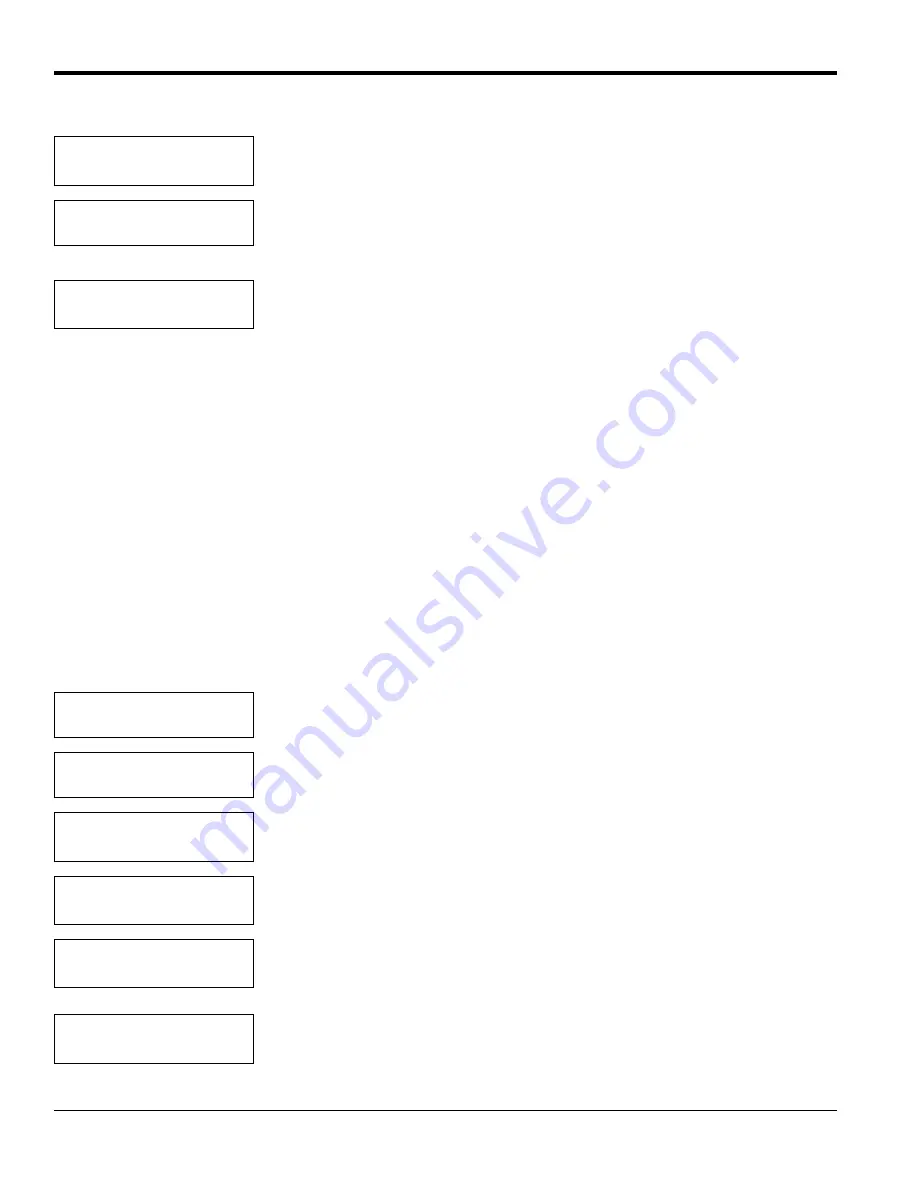
Chapter 4. Basic Programming
30
TMO2D Digital Display User’s Manual
4.4.8 Set Error Handling? (cont.)
You have completed the Setup Menu. At the Main Menu prompt, press [NO] to leave the Setup Menu and progress to
the Outputs Menu.
4.5 The Outputs Menu
The second main menu, the
Outputs Menu
, enables users to select which 4-20 mA output (A or B) to adjust, and to
enter all necessary information for either or both outputs.
The TMO2D provides a choice of one isolated 0/4-20 mA output, or two isolated 0/4-20 mA outputs. You can set both
options for a 0 to 20-mA or a 4-20 mA response, and scale the output anywhere within the range of the transmitter.
Note:
The display is programmed to accept settings for two outputs; however, if only a single isolated output is used,
only output A is effective.
The steps in the following example illustrate how to set up outputs. In this instance, output A will have a 0 to 20-mA
range, with 0 mA equal to 0% oxygen and 20 mA equal to 100% oxygen. (Appendix B offers a flow diagram of the
Outputs Menu
in Figure 26 on page 79.)
System Error Effects
Done?
Press [YES] to return to the Setup Menu, or [NO] to continue scrolling through the
System Error Effects submenu.
SETUP MENU
Set Error Handling?
Press [NO] to exit the Error Handling menu.
SETUP MENU
Done?
Press [YES] to exit the Setup Menu and return to the Main Menu. Press [NO] to
return to the “Set Time?” prompt.
MAIN MENU
Setup?
Press [NO] to proceed to the Output Menu.
MAIN MENU
Outputs?
Press [YES] to enter the Output Menu.
Select Output to set:
[A] B done
Use the [NO] or arrow keys to move the brackets to “A,” and press [YES] to confirm
the selection.
A Output Range (mA):
[0-20] 4-20
Use the [NO] or arrow keys to select the desired output range, and press [YES] to
confirm the choice.
Output A 0 mA Value
%O
2
[X.XX]:
Use the numeric keys to enter the low end value. (The X’s represent the previously
entered value for 0 mA.)
Output A 0 mA Value
%O
2
[0.00]:
Then press [YES] to confirm the entry and [YES] again to proceed to the high end
value.
Summary of Contents for TMO2D
Page 1: ...GE Measurement Control Solutions Gas Moisture TMO2D Digital Display User s Manual ...
Page 4: ...ii ...
Page 10: ...Chapter 1 Features and Capabilities 2 TMO2D Digital Display User s Manual ...
Page 24: ...Chapter 2 Installation 16 TMO2D Digital Display User s Manual ...
Page 26: ...Chapter 2 Installation TMO2D Digital Display User s Manual 18 ...
Page 72: ...Chapter 6 Specifications 64 TMO2D Digital Display User s Manual ...
Page 74: ...Appendix A Outline and Installation Drawings 66 TMO2D Digital Display User s Manual ...
Page 86: ...Appendix B Menu Maps 78 TMO2D Digital Display User s Manual ...
Page 92: ...Appendix B Menu Maps TMO2D Digital Display User s Manual 84 ...
Page 96: ...Index 88 TMO2D Digital Display User s Manual ...
Page 98: ...Warranty 90 TMO2D Digital Display User s Manual ...
Page 100: ......
Page 101: ......