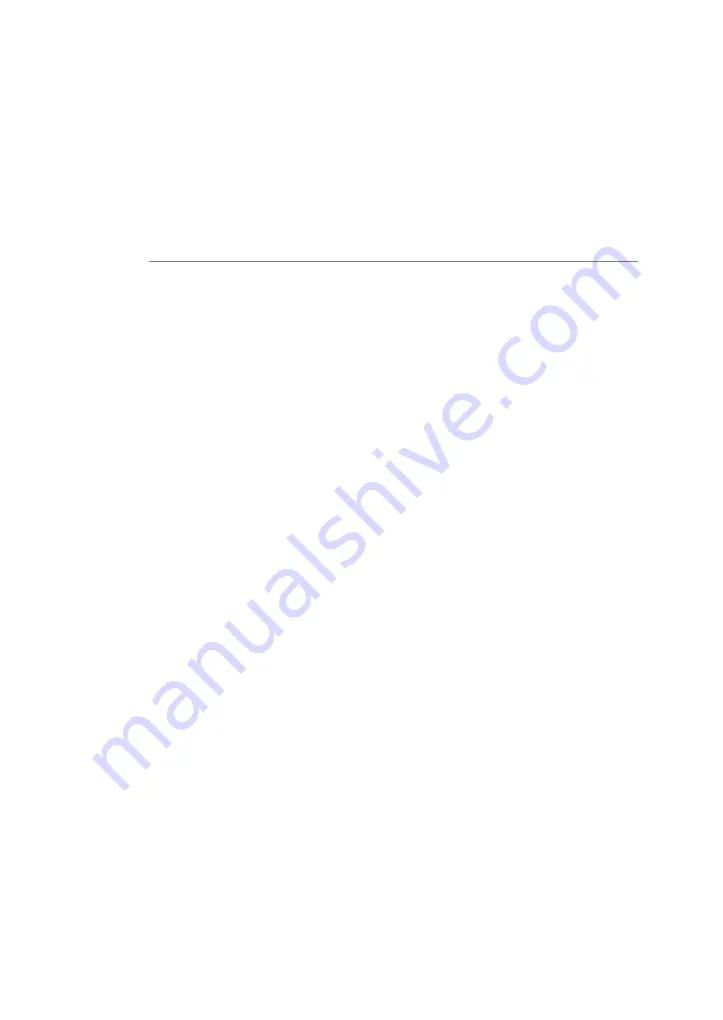
Function
The module has two separate restrictors for A and B pumps respectively. The flow path
inside this module is designed to use inlets from pump A for sample application.
The system pressure sensor is located inside the flow restrictor module. This sensor
measures the pressure near the outlet, and UNICORN compares the value with the
highest allowed and the lowest allowed system pressure.
38
ÄKTA pilot 600 User Manual 29274559 AA
3 Description of modules
3.4 Flow restrictor
Summary of Contents for AKTA pilot 600
Page 1: ...KTA pilot 600 User Manual...