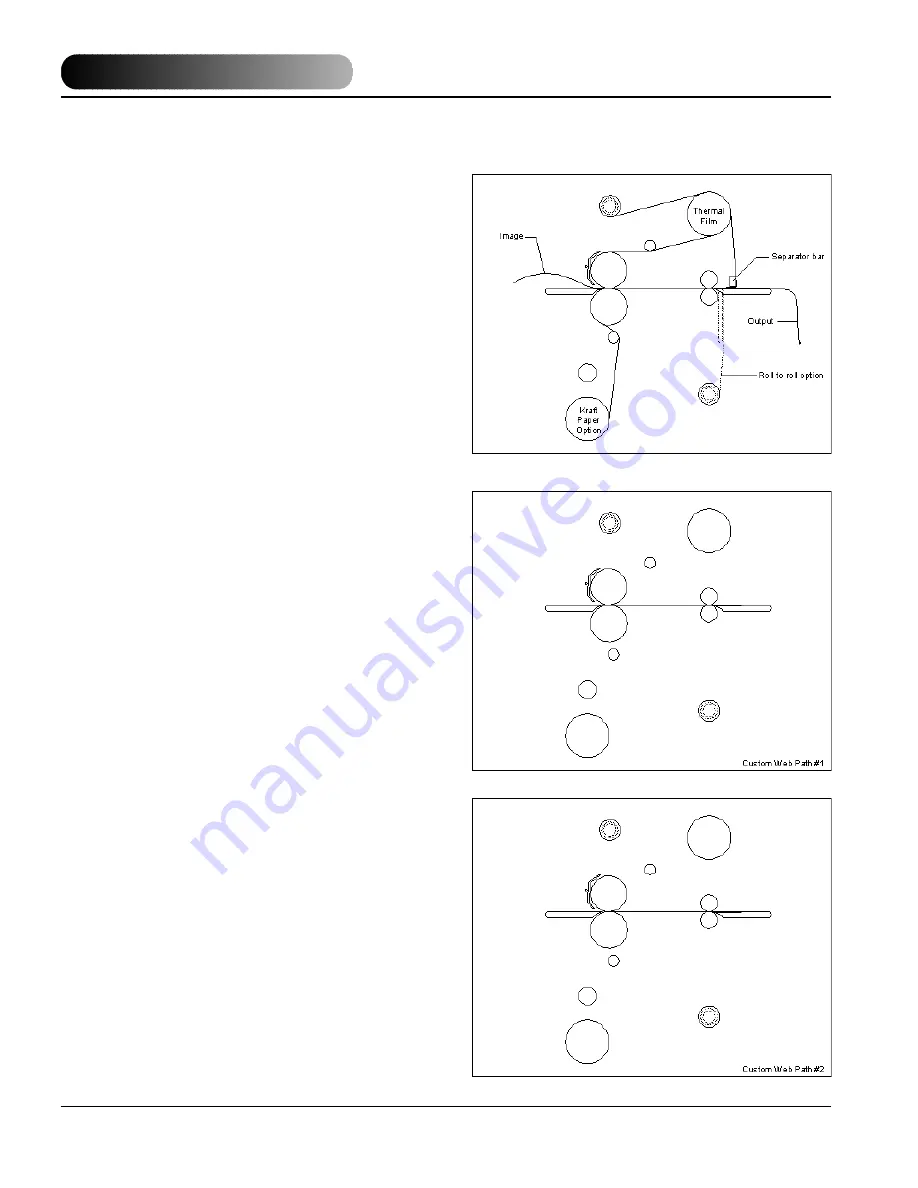
Falcon 60+ (-1)
Falcon 60+ (-1)
Operations Manual
© 2003 General Binding Corporation
Page 22
Tips for ACCUSHIELD
(Figure 40)
1. Load the laminator as illustrated in Figure 40.
2. You must have the Separator bar option to
accurately run this material.
3. Set Top Temp. to 265 OF (129 OC) and a speed
setting no greater than 4.
4. Liner rewind tension will be greater than normal
operating standards.
5. To prevent some adhesive adhering to the rollers,
you may choose to use a roll of kraft paper for a
carrier.
Use the blank space below and blank diagrams to
note your tips and web paths for your special
applications.
TIPS FOR CUSTOM APPLICATION #1 (Figure 41)
1.
2.
3.
4.
TIPS FOR CUSTOM APPLICATION #2 (Figure 42)
1.
2.
3.
4.
5.
Fig 40
Fig 41
Fig 42
Summary of Contents for Falcon 60+ (-1)
Page 1: ......