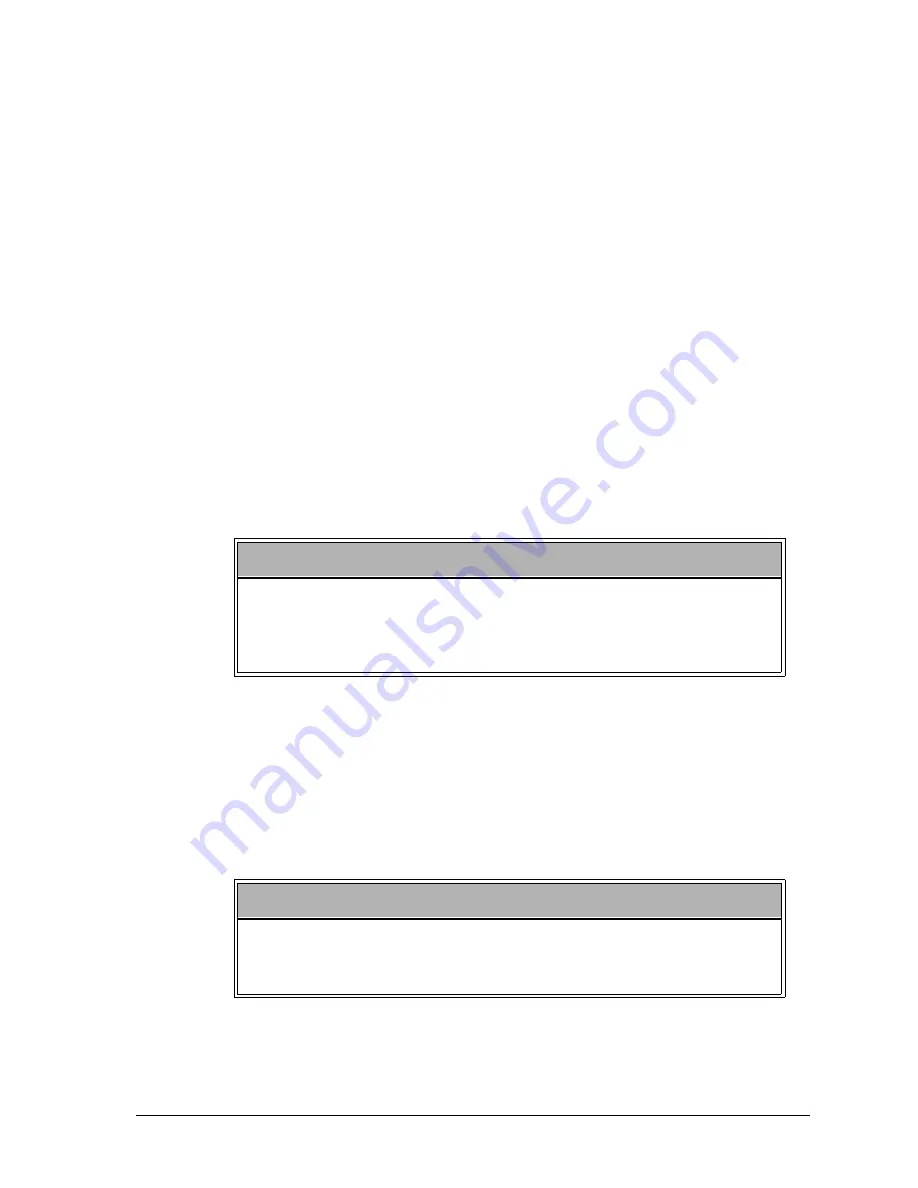
CE and EMC Guidelines
G & L Motion Control Inc.
MMC Hardware Manual
163
Under the stated conditions, there will be no disturbance of digital
I/O, encoder, or stepper operation. For analog signals, there may be
momentary disturbances but there will be self-recovery when the
noise subsides.
In order to meet the EU directive requirement for emissions and
immunity, fiber optics must be used for I/O expansion.
Although the control will pass the electrical fast transient test on
incoming power lines, users may still want to use a power line
conditioner.
As a general precaution, do not operate transmitters, arc welding
equipment, or other high noise radiators within one meter of a PiC
enclosure that has the door open. Continue to equip inductive
devices, if they are in series with a mechanical contact or switch,
with arc suppression circuits. These devices include contactors,
solenoids and motors. Shield all cables that carry heavy current
near the system, using continuous foil wrap or conduit grounded at
both ends. Such cables include power leads for high-frequency
welders and for pulse-width-modulated motor drives.
Worst case tests with analog I/O modules have caused momentary
disturbances no greater than .5V in a +10V to -10V range and .5
mA in a 4 to 20 mA range. Worst case tests with an RTD module
have caused momentary disturbances no greater that + or -4°C in a
range of -200° to 266°C. Worst case tests with a JK thermocouple
module have caused momentary disturbances no greater than + or -
1 mV over a 100 to 1.
NOTE
Shields for signal wires are grounded at only one end, to provide im-
munity to outside noise sources. However, the shields for “noise
sources” are grounded at both ends, to reduce emissions and “con-
tain” the noise.
NOTE
To assure compliance with the low voltage directive, it is necessary
to follow installation instructions in the controller Hardware Manual.
Also refer to any instructions specific to individual control modules.
Summary of Contents for MMC-A2
Page 1: ...Standalone MMC TM Hardware Manual Version 15 0 G L Motion Control Inc...
Page 2: ......
Page 36: ...Installation Operation Maintenance 28 MMC Hardware Manual G L Motion Control Inc...
Page 124: ...Standalone Digital MMC Control 116 MMC Hardware Manual G L Motion Control Inc...
Page 136: ...MMC Ethernet TCP IP Option Module 128 MMC Hardware Manual G L Motion Control Inc...
Page 175: ...CE and EMC Guidelines G L Motion Control Inc MMC Hardware Manual 167...
Page 176: ...CE and EMC Guidelines 168 MMC Hardware Manual G L Motion Control Inc...
Page 177: ...CE and EMC Guidelines G L Motion Control Inc MMC Hardware Manual 169...
Page 178: ...CE and EMC Guidelines 170 MMC Hardware Manual G L Motion Control Inc...
Page 186: ...Appendix A Operation Details 178 MMC Hardware Manual G L Motion Control Inc...