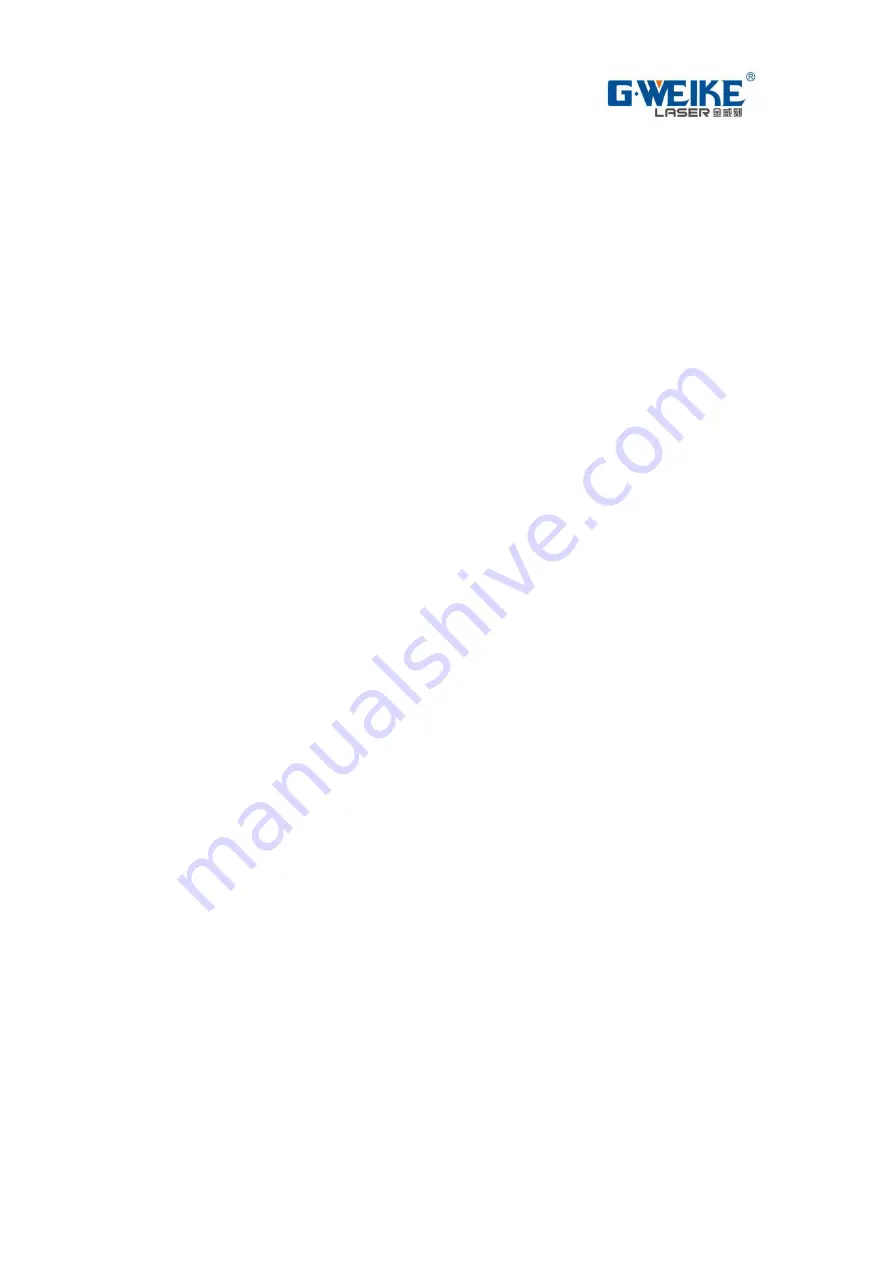
G.Weike Laser
Profession Laser Manufacturer more than 15 Years.
4.4 Fiber Special Cutting Head
......................................................................
.....................................................................
4.4.2 Height controller connection
.......................................................
4.4.3 Installation of ceramic part & nozzles
.......................................
.................................................................................................
.......................................................................
...................................................................................
4.7Installation debugging methods and relevant specification
Chapter 5 Testing and operation of the machine
........................................................
5.1Summarize and operation guide
.............................................................
5.2 RAYCUS Optical fiber signal line connection method
5.3 Adjusting laser head height and turn on the software
...............................................................................
5.3.2 Control software operation process
..........................................
..........................................................................
.....................................................................................
5.6 Nozzle function and central adjustment
..............................................
5.6.1Nozzle function and adjustment
..................................................
5.6.2 Adjusting laser beam focus
.........................................................
5.6.3 Set distance between nozzle and work piece
5.7 Laser cutting process principle
.............................................................
..................................................................
5.7.2 The choice of laser cutting gas and pressure
5.7.3 The influence of laser cutting power in cutting quality
5.8 Note for use main machine, chiller, laser power supply.
5.8.1 Electric safety precautions
...........................................................
5.8.2 Operational matters needing attention
.....................................
5.8.3 Note on the use of temperature in spring and winter
5.9 After installation and debugging acceptance test program,
method and judgment
...............................................................................
51
5.10 The machine shutdown procedure
.....................................................
Chapter6 Maintain and trouble shooting
......................................................................
...................................................................................................
......................................................................................
6.2 The peripheral equipment daily maintenance and maintenance
.................................................................
6.2.2 Laser Source and laser head Module maintenance
6.3 Optical system inspection and cleaning
..............................................
6.3.1 Something should pay attention
.................................................
6.3.2 Dismantle ,installation or replacement the method of optical
lenses
.................................................................................................
58
6.3.3 The steps of cleaning lenses
.......................................................
6.3.4 Storage of optical lenses
..............................................................
................................................................................
..............................................................................