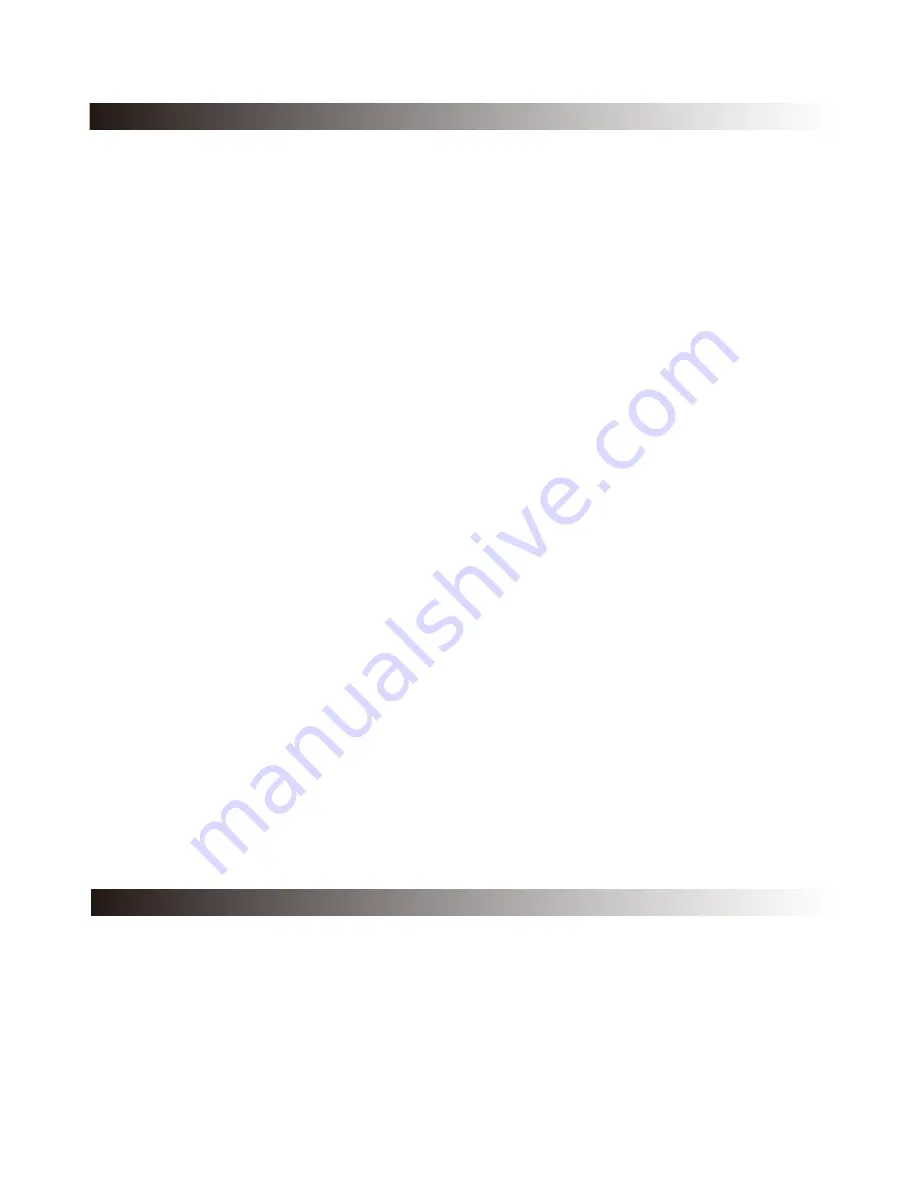
CONTENTS
1. DESCRIPTION OF EACH CONTROL OPERATION
1. COOLING OPERATION................................................................................................
3. DRY OPERATION.........................................................................................................
2. HEATING OPERATION.................................................................................................
5. INDOOR FAN CONTROL..............................................................................................
4. AUTO CHANGEOVER OPERATION............................................................................
7. LOUVER CONTROL.....................................................................................................
6. OUTDOOR FAN CONTROL..........................................................................................
10. TIMER OPERATION CONTROL.................................................................................
9. COMPRESSOR CONTROL..........................................................................................
12. TEST OPERATION CONTROL...................................................................................
11. ELECTRONIC EXPANSION VALVE CONTROL........................................................
14. FOUR-WAY VALVE EXTENSION SELECT................................................................
13. PREVENT TO RESTART (ST)...................................................................................
16. FORCED AUTO OPERATION....................................................................................
15. AUTO RESTART.........................................................................................................
17. FORCED COOLING OPERATION.............................................................................
19. 10°C HEAT OPERATION............................................................................................
18. COMPRESSOR PREHEATING..................................................................................
20. ECONOMY OPERATION............................................................................................
22. OFF DEFROST OPERATION CONTROL...................................................................
21. DEFROST OPERATION CONTROL...........................................................................
01-01
01-02
01-02
01-03
01-05
01-07
01-08
01-10
01-11
01-13
01-13
01-14
01-14
01-14
01-14
01-15
01-15
01-15
01-16
01-18
01-13
2. TROUBLE SHOOTING
2-1 INDOOR UNIT ERROR DISPLAY...............................................................................
2-2 WIRELESS LAN ADAPTER ERROR DISPLAY..........................................................
2-3 MOBILE APP ERROR DISPLAY.................................................................................
02-01
02-02
02-03
2-4 MOBILE APP ERROR DISPLAY (In Wireless LAN Control system)........................... 02-04
23. VARIOUS PROTECTIONS.......................................................................................... 01-19
24. LOW NOISE OPERATION........................................................................................... 01-21
26. POWERFUL OPERATION...........................................................................................
25. HUMAN SENSOR (Energy Saving).............................................................................
01-22
27. FILTER CLEAN............................................................................................................ 01-22
01-21
8. DUAL FAN CONTROL.................................................................................................. 01-09
28. PLASMA CLEAN ......................................................................................................... 01-22
29. WIRELESS LAN ......................................................................................................... 01-23
2-5 TROUBLE SHOOTING WITH ERROR CODE............................................................. 02-05
2-6 TROUBLE SHOOTING WITH NO ERROR CODE.......................................................02-38
2-7 SERVICE PARTS INFORMATION.............................................................................. 02-43
Summary of Contents for AO*G09KXCA Series
Page 4: ...1 DESCRIPTION OF EACH CONTROL OPERATION WALL MOUNTED type INVERTER ...
Page 28: ...2 TROUBLESHOOTING WALL MOUNTED type INVERTER ...
Page 82: ...3 APPENDING DATA WALL MOUNTED type INVERTER ...
Page 89: ...INDOOR UNIT Main PC board Sub PC board 4 WIRING DIAGRAMS OUTDOOR UNIT 03 07 ...
Page 90: ...4 DISASSEMBLY PROCESS WALL MOUNTED type INVERTER ...
Page 110: ...Dec 2016 Printed in Japan 3 3 17 Suenaga Takatsu ku Kawasaki 213 8502 Japan ...