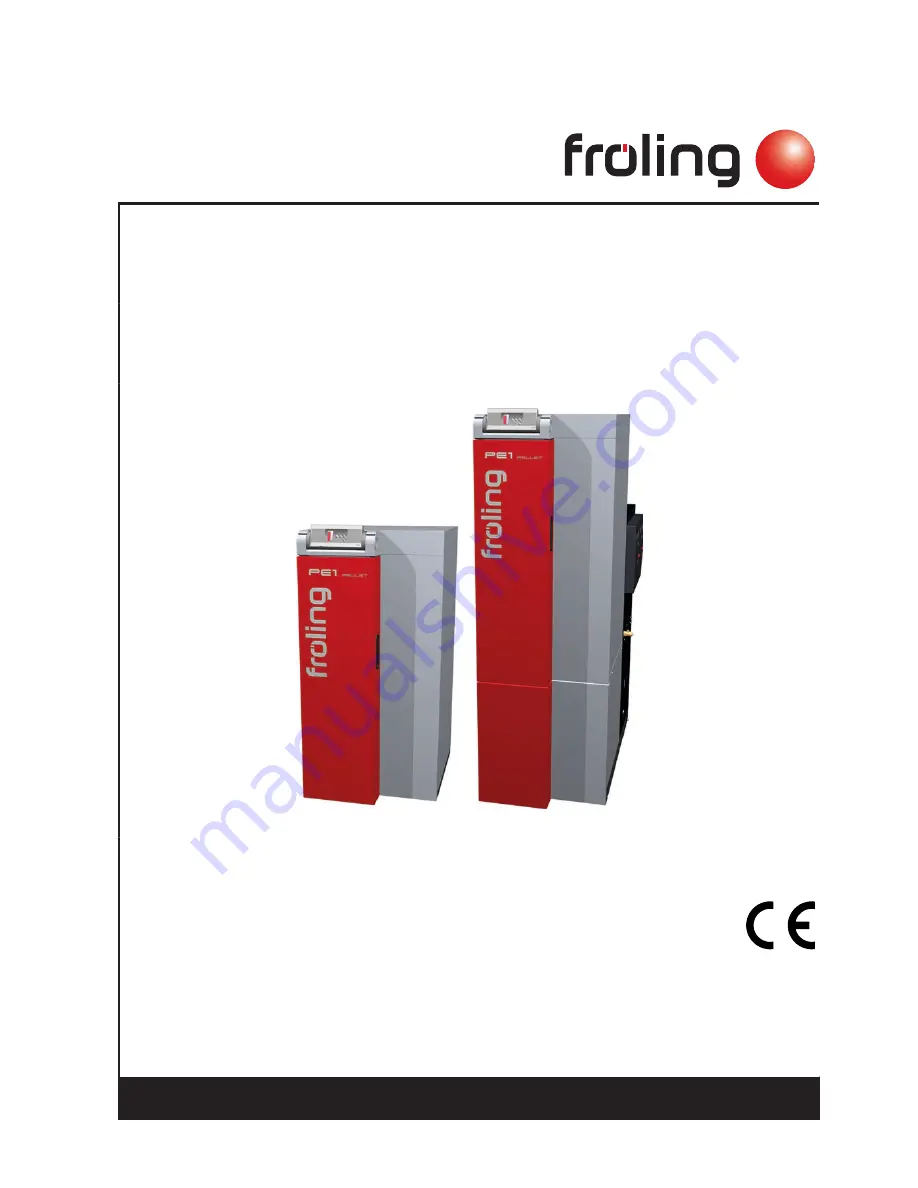
Installation Instructions
Pellet boiler PE1 Pellet 7-35
Translation of the original German installation instructions for technicians
Read and follow the instructions and safety information!
Technical changes, typographical errors and omissions reserved!
M1441017_en | Edition 24/03/2017
Froling GesmbH | A-4710 Grieskirchen, Industriestraße 12 | www.froeling.com