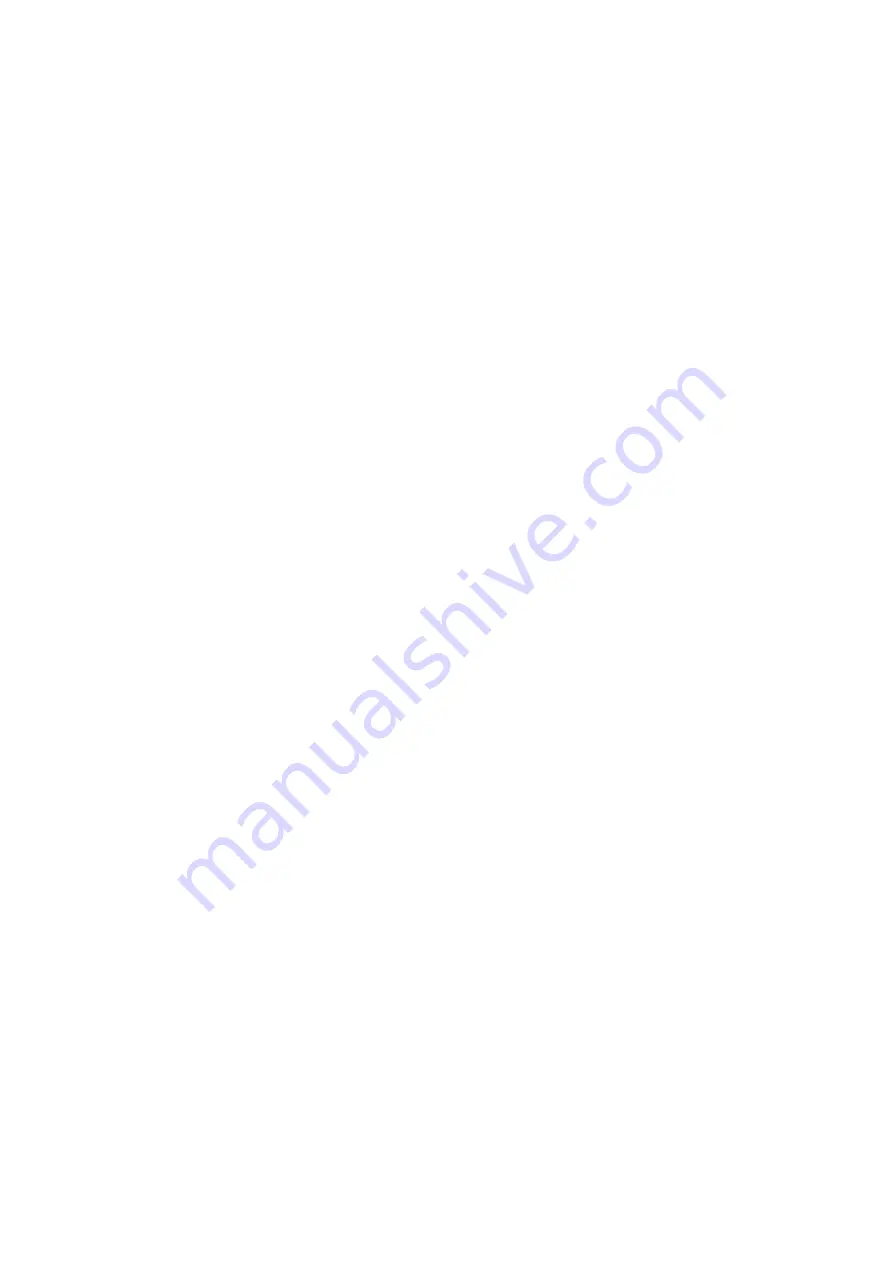
3
Area check
Before starting work on systems containing flammable refrigerants, safety checks must be carried out to
guarantee a minimal ignition risk.
Work procedure
The work must be carried out according to a controlled procedure in order to reduce the risks of releasing a
flammable gas or vapour while working.
General work area
All maintenance staff and other personnel working in the surrounding area must be made aware of the work
carried out. Work conducted in enclosed areas must be avoided.
Check for the presence of refrigerant
The area must be analysed using a suitable refrigerant detector before and during work so that the technician is
informed of the presence of a potentially toxic or flammable atmosphere. Check that the leak detection
equipment used is suitable for use with all refrigerants concerned, i.e. that it does not cause a spark, is
correctly isolated or is entirely safe.
Check for the presence of a fire extinguisher
If work must be carried out on the cooling equipment or any part associated therewith at a certain
temperature, suitable fire extinguishing means must be within reach. Place a dry chemical fire extinguisher or
CO
2
fire extinguisher near the work area.
No source of ignition
No person carrying out work on a cooling system involving exposing the piping may use any ignition source,
which could create a fire or explosion risk. All possible ignition sources, in particular cigarettes, must not enter
within a sufficient perimeter of the installation, repair, removal or disposal site, in the event that refrigerant
could be released into the surrounding space. Before starting the work, the area around the equipment must
be examined to check for all fire or ignition risks. "No smoking" signs must be displayed.
Area ventilation
Before accessing the unit in any manner whatsoever with the intention of performing any maintenance task,
check that the area is open and well-ventilated. Suitable ventilation must be provided throughout the
maintenance task to allow any refrigerant that could be released into the atmosphere to be safely dispersed.
Refrigeration equipment check
The manufacturer's recommendations in terms of care and maintenance must always be complied with. When
replacing electric components, check that components used are of the same type and category as those
recommended/approved by the manufacturer. When in doubt, contact the manufacturer's technical
department for assistance.
The following checks must be applied to installations using flammable refrigerants:
-the markings on the equipment must remain visible and legible; any illegible markings or signs must be rectified;
-the hoses or components of the cooling circuit are installed in a position where they are unlikely to be exposed to
any substance capable of corroding the components containing refrigerant, unless the components are made from
materials that are typically corrosion-proof or correctly protected from such corrosion.
Electric component check
The repair and maintenance of electric components must include initial safety checks and component
inspection procedures. If a defect capable of jeopardising safety arises, no power supply must be connected to
the circuit until the problem has been completely resolved. If the defect cannot be rectified immediately and if
Summary of Contents for 74139
Page 2: ......
Page 4: ......
Page 13: ...9 2 Dimension unit mm Model FSP 05...
Page 14: ...10 Model FSP 08 FSP 11...
Page 15: ...11 Model FSP 14...
Page 22: ...18 Dry contact timer connection Timer Dry contact pump connection...
Page 30: ...26 8 Exploded Diagram Model FSP 05...
Page 32: ...28 Model FSP 08 FSP 11...
Page 35: ...31 Model FSP 14...
Page 47: ...43 2 Dimensiones mm Modelos FSP 05...
Page 48: ...44 Modelos FSP 08 FSP 11...
Page 49: ...45 Modelos FSP 14...
Page 65: ...61 8 Diagrama Explosionado Model FSP 05...
Page 67: ...63 Model FSP 08 FSP 11...
Page 70: ...66 Model FSP 14...
Page 82: ...78 2 Dimension mm Mod le FSP 05...
Page 83: ...79 Mod les FSP 08 FSP 11...
Page 84: ...80 Mod le FSP 14...
Page 100: ...96 8 Sch ma Eclat Mod le FSP 05...
Page 102: ...98 Mod le FSP 08 FSP 11...
Page 105: ...101 Mod le FSP 14...
Page 117: ...113 2 Dimension mm Modell FSP 05...
Page 118: ...114 Modell FSP 08 FSP 11...
Page 119: ...115 Modell FSP 14...
Page 134: ...130 8 Explosionszeichnung Modell FSP 05...
Page 136: ...132 Modell FSP 08 FSP 11...
Page 139: ...135 Modell FSP 14...
Page 151: ...147 2 Dimensione mm Modelli FSP 05...
Page 152: ...148 Modelli FSP 08 FSP 11...
Page 153: ...149 Modelli FSP 14...
Page 169: ...165 8 Exploded Diagram Model FSP 05...
Page 171: ...167 Model FSP 08 FSP 11...
Page 174: ...170 Model FSP 14...
Page 186: ...182 2 Dimensie mm Model FSP 05...
Page 187: ...183 Model FSP 08 FSP 11...
Page 188: ...184 Model FSP 14...
Page 195: ...191 Dry contact timer verbinding Timer Dry contact pomp aansluiting...
Page 203: ...199 8 Ge xplodeerd Diagram Modellen FSP 05...
Page 205: ...201 Modellen FSP 08 FSP 11...
Page 208: ...204 Modellen FSP 14...
Page 220: ...216 2 Dimens o mm Modelo FSP 05...
Page 221: ...217 Modelo FSP 08 FSP 11...
Page 222: ...218 Modelo FSP 14...
Page 229: ...225 Conex o do temporizador de contacto seco Cron metro Conex o da bomba de contacto seco...
Page 237: ...233 8 Diagrama Explodido Modelo FSP 05...
Page 239: ...235 Modelo FSP 08 FSP 11...
Page 242: ...238 Modelo FSP 14...
Page 250: ......
Page 251: ......
Page 252: ......