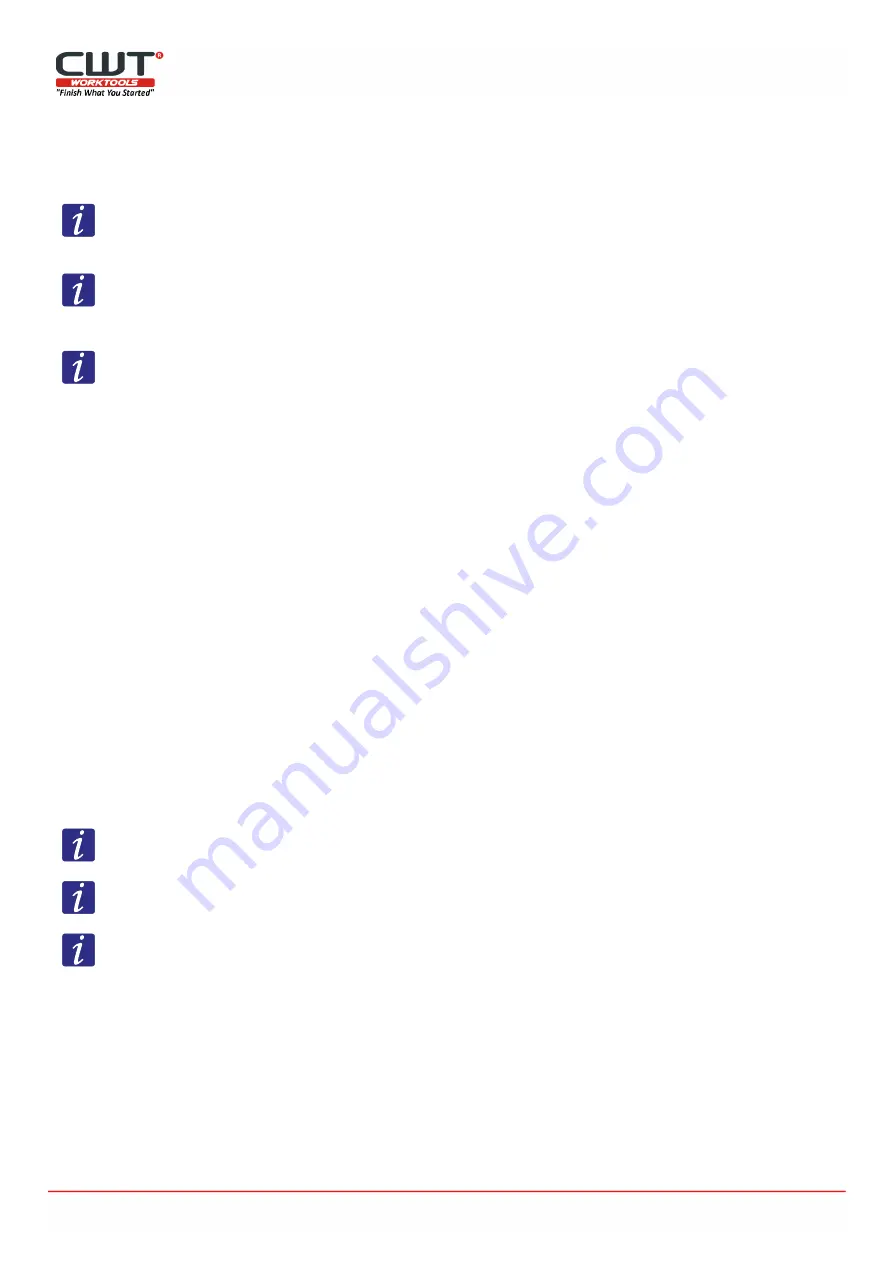
●
●
●
●
●
7.4 Emergency stop
Press one of the emergency buttons on the machine to immediately stop all its functions.
7.5 Restart after an emergency stop
To restore the cycle after an emergency stop:
Resolve the cause that led to the emergency stop.
Deactivate the emergency button, turning the button counter-clockwise.
Press the safety reset button.
Restart processing. See par. 7.2.
7.6 Re-start after a black-out
To restart the machine after a black-out:
Perform the operations described in par. 7.2.
7.7 Shut-down
The emergency stop causes deactivation of the auxiliary circuits and consequently an immediate stop of all machine
movements.
When they are hot, the rollers can deform if left stationary for prolonged periods of time.
They must always be kept in rotation for cooling.
If they need to be stopped, for example for an emergency stop, restart them as soon as possible.
When they are hot, the rollers can deform if stopped and left in contact with one another.
If they need to be stopped, move them away from one another.
The machine is switched off by setting the main electrical switch to pos. OFF or 0.
The machine can be switched off only after the two rubber rollers have cooled down.
Stopping rotation of the two rubber rollers while they are still hot may damage them as they tend to become oval-
shaped.
GALAXY
USE AND MAINTENANCE MANUAL
EN
MANUAL CODE: 756100330_EN
REVISION: 0
DATE: 07/03/2019
FLEXA S.r.l. - Partial or whole reproduction prohibited without authorisation
44
Summary of Contents for CWT GALAXY
Page 2: ......
Page 93: ......
Page 94: ...FLEXA Sr l reserves the right to make technical changes to this manual without prior notice...