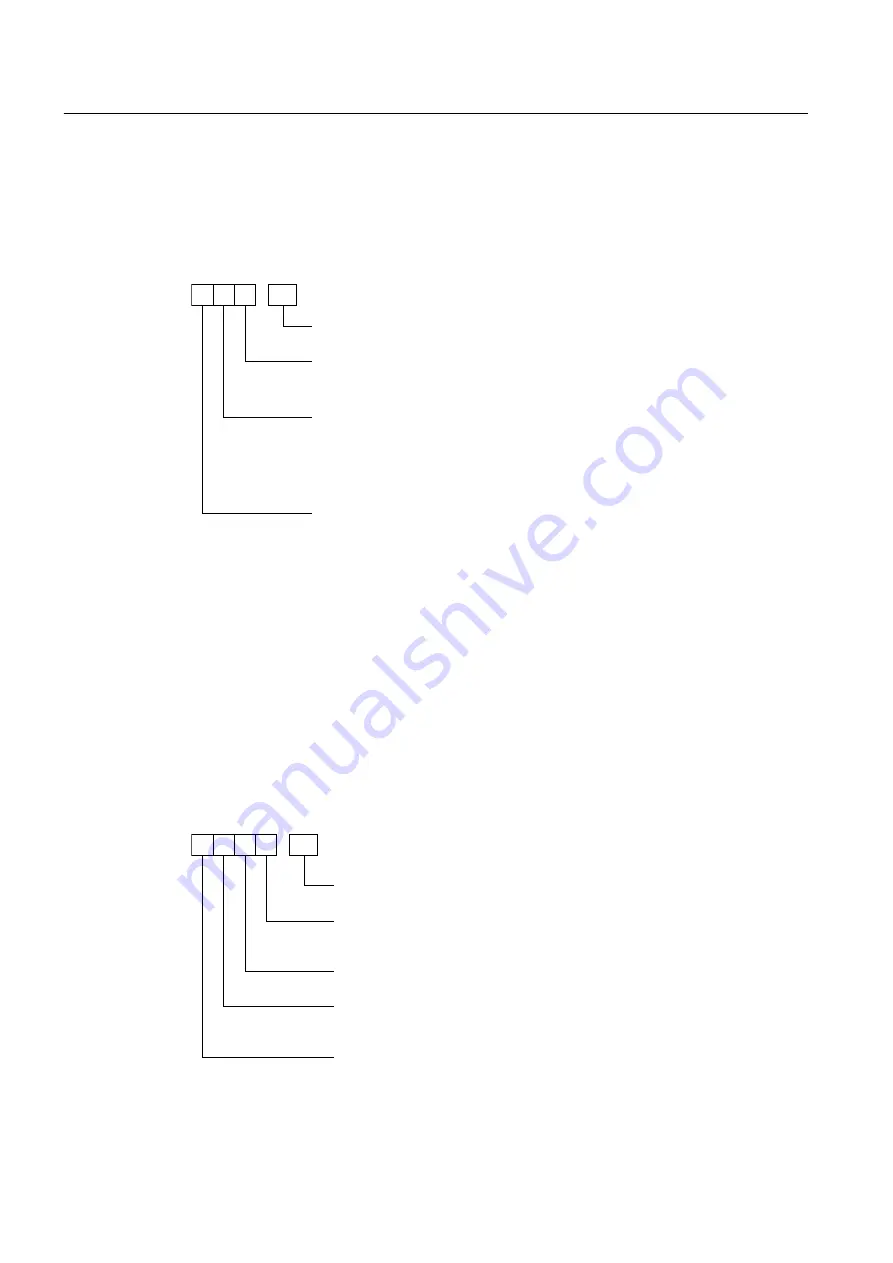
Example code
The following is an example of the code printed in line 5 of the rating plate and explains the
meaning of the individual letters and numbers.
6L]H
'HVLJQRIWKHRXWSXWVKDIW
WR
6ROLGVKDIWJHDUXQLWZLWKIRRW
*HDUXQLWW\SH
6KDIWPRXQWHGJHDUXQLWZLWKIRRW
6KDIWPRXQWHGJHDUXQLWZLWKRXWIRRW
2QHKHOLFDOJHDUVWDJH
1RRIVWDJHV
7ZRKHOLFDOJHDUVWDJHV
7KUHHKHOLFDOJHDUVWDJHV
)RXUKHOLFDOJHDUVWDJHV
)LYHKHOLFDOJHDUVWDJHV
6L[KHOLFDOJHDUVWDJHV
+HOLFDOJHDUXQLW
%HYHOKHOLFDOJHDUXQLW
6 ( 1
$
2
1
6
.
(
=
'
9
)
6
Further information
You can find additional information on the weights and the enveloping surface sound pressure
levels in chapters Weights (Page 118) and Enveloping surface sound pressure level
(Page 121).
Further information about these technical data can be found in the separate data sheet and the
dimension drawings in the complete documentation for the gear unit.
Example code
The following is an example of the code printed in line 5 of the rating plate and explains the
meaning of the individual letters and numbers.
6L]H
WR
'HVLJQRIWKHLQSXWVKDIW
+RUL]RQWDOLQSXWVKDIW
9HUWLFDOLQSXWVKDIW
6KDIWPRXQWHGJHDUXQLWZLWKRXWIRRW
)RXUKHOLFDOJHDUVWDJHV
)LYHKHOLFDOJHDUVWDJHV
%HYHOKHOLFDOJHDUXQLW
'HVLJQRIWKHRXWSXWVKDIW
1RRIVWDJHV
*HDUXQLWW\SH
. ) 2
+
9
2
.
9
9
)
Technical data
B.1 General technical data
REDUREX Gear unit 5200en
114
Operating Instructions 03/2019
Summary of Contents for K.A Series
Page 2: ...07 03 2019 13 01 V4 00...
Page 10: ...Table of contents REDUREX Gear unit 5200en 10 Operating Instructions 03 2019...
Page 44: ...Description 3 16 Auxiliary drive REDUREX Gear unit 5200en 44 Operating Instructions 03 2019...
Page 82: ...Mounting 5 9 Final work REDUREX Gear unit 5200en 82 Operating Instructions 03 2019...
Page 104: ...Maintenance 8 4 Possible faults REDUREX Gear unit 5200en 104 Operating Instructions 03 2019...
Page 106: ...Service Support REDUREX Gear unit 5200en 106 Operating Instructions 03 2019...
Page 108: ...Disposal REDUREX Gear unit 5200en 108 Operating Instructions 03 2019...
Page 110: ...Spare parts REDUREX Gear unit 5200en 110 Operating Instructions 03 2019...
Page 126: ...Index REDUREX Gear unit 5200en 126 Operating Instructions 03 2019...
Page 127: ......