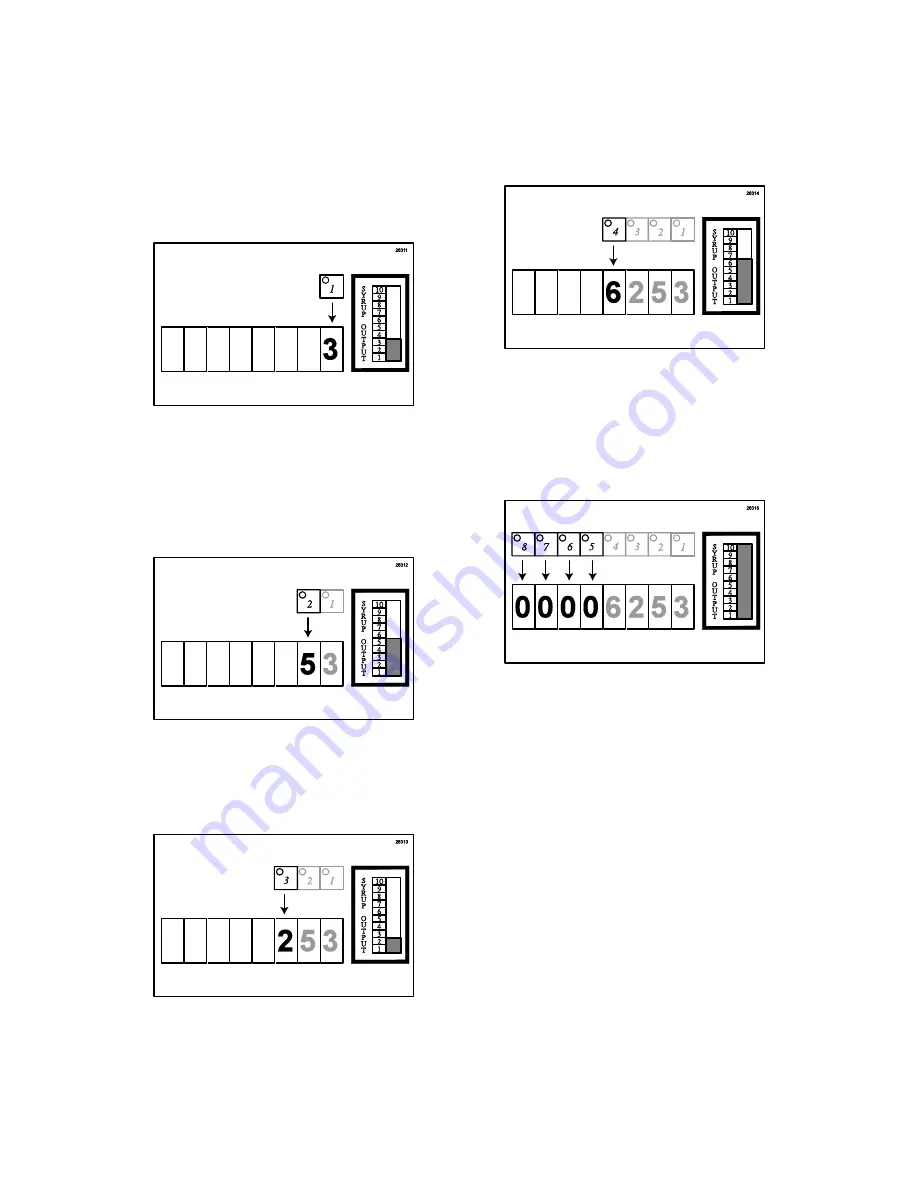
62
2. Touch the #1 key on the keypad and
read the SYRUP OUTPUT level bar
graph. Write down the level value 1-0
as your first number on the right. 10 on
the bar graph represents 0. (See
Figure 160.)
Figure 160
3. Touch the #2 key on the keypad and
read your SYRUP OUTPUT bar graph.
Write down the value as your second
number from the right. (See
Figure 161.)
Figure 161
4. Touch the #3 key and record as your
third number from the right. (See
Figure 162.)
Figure 162
5. Touch the #4 key and record as your
fourth number from the right. (See
Figure 163.)
Figure 163
6. Repeat with selections #5- #8
recording each number down from the
right to left. Remember that 10 on the
bar graph represents 0. (See
Figure 164.)
Figure 164
7. The final number (in this example
6,253) is your total serving count.
Deduct the previous day’s reading from
the current reading to determine the
current day’s serving count.
8.
To exit the ACCESS COUNT
READOUT mode, press the OFF
key.
Summary of Contents for FB 80S-08
Page 4: ...3 PARTS IDENTIFICATION FUNCTIONS General System Overview See Figure 1 ...
Page 5: ...4 Figure 1 ...
Page 6: ...5 Cabinet See Figure 2 ...
Page 7: ...6 Figure 2 ...
Page 8: ...7 Blending Assembly and Related Parts See Figure 3 ...
Page 9: ...8 Figure 3 ...
Page 10: ...9 Syrup Pump and Related Parts See Figure 4 ...
Page 11: ...10 Figure 4 ...
Page 12: ...11 Sanitizer Pump and Related Parts See Figure 5 ...
Page 13: ...12 Figure 5 ...
Page 14: ...13 Electronic Parts and Connections See Figure 6 ...
Page 15: ...14 Figure 6 ...
Page 16: ...15 Spare Parts Kit See Figure 7 ...
Page 17: ...16 Figure 7 ...
Page 18: ...17 ...
Page 30: ...29 ...
Page 46: ...45 ...
Page 67: ...66 ...
Page 68: ...67 ...
Page 69: ...68 ...
Page 70: ...69 ...
Page 71: ...70 ...
Page 72: ...71 ...