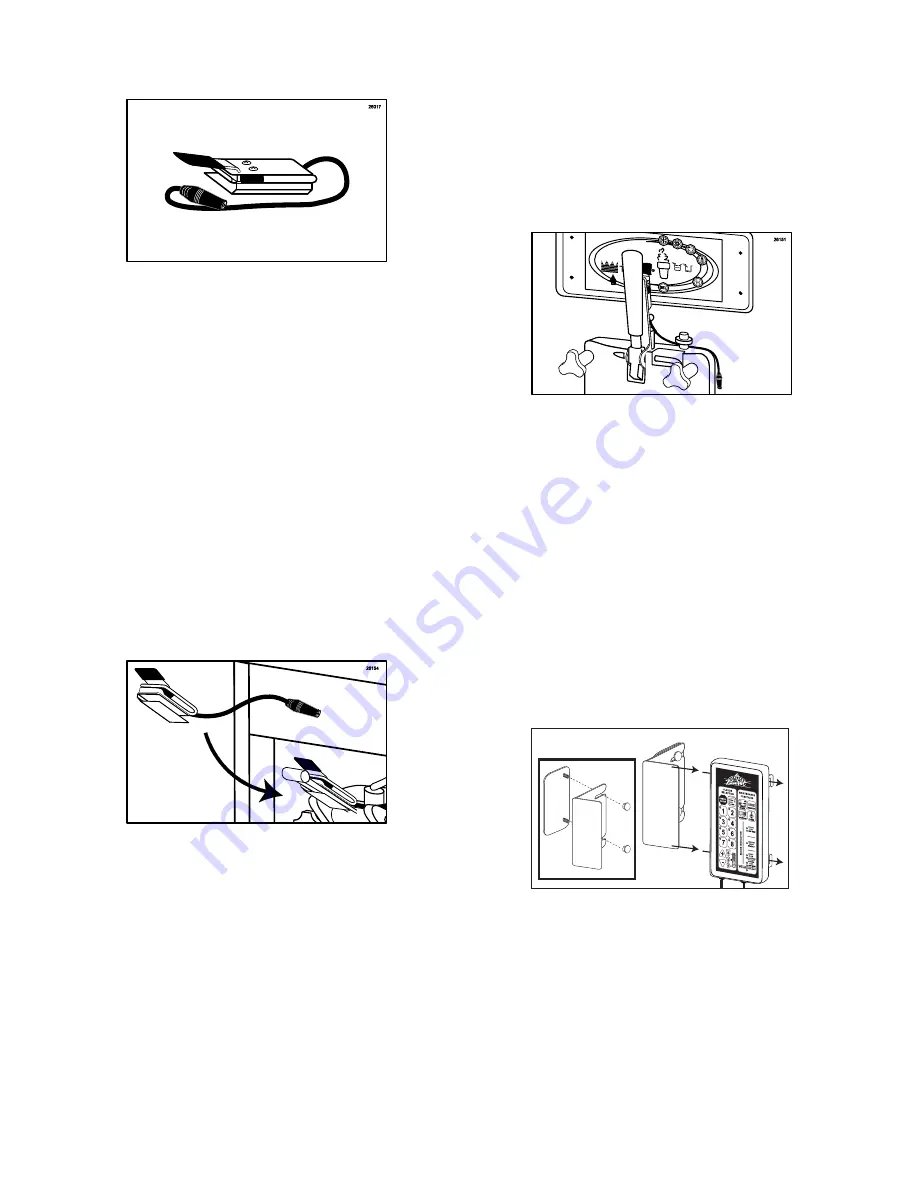
47
Installing the Spigot Switch Assembly
Figure 116
To activate the Flavor Burst
®
system, a switch
must be installed on the freezer draw-handle.
Every FB 80D system ships with a standard
Spigot Switch Assembly common to most
freezers with flat handle bars. (See Figure 116.)
Should your freezer have a round handle rod or
a handle of unusual size or shape, this standard
switch may not be suitable for your freezer
model. Contact your local distributor if the
Spigot Switch included with your unit does not
fit.
1. To install the standard Spigot Switch
assembly to a flat handle, simply clip the
Switch Bracket onto the handle and slide it
up the handle until the switch is within
grasping range. (See Figure 117.)
Figure 117
NOTE:
IF YOUR UNIT INCLUDES AN
ALTERNATE SPIGOT SWITCH, REFER TO
INSTRUCTIONS INCLUDED WITH IT FOR
PROPER INSTALLATION.
NOTE
: THE SPIGOT SWITCH INSTALLED
ON THE FREEZER SHOWN IN OTHER
SECTIONS THROUGHOUT THIS MANUAL IS
NOT
THE STANDARD SPIGOT SWITCH
ASSEMBLY AND IS ONLY FOR USE WITH
THAT FREEZER OR SIMILAR MODELS. (See
Figure 118.)
Figure 118
Installing the Keypad and Keypad Mounting
Bracket
The Keypad is the control unit for the Flavor
Burst
®
system. Normal operating functions are
performed using the Keypad and the freezer
draw handle. The Keypad is attached to the
freezer with the Keypad Mounting Bracket.
1. Slide the Keypad onto the main Bracket
plate and assemble the two Bracket parts in
the style that will best suit your freezer and
daily operations. One example is given in
the figure below. (See Figure 119.)
26120
Figure 119
Summary of Contents for FB 80D Series
Page 5: ...4 General System Overview 13 2 1 3 5 6 15 14 10 8 11 12 9 7 17 16 4 26000 Figure 1...
Page 7: ...6 Outer Cabinet 3 1 2 12 10 7 13 4 5 9 8 6 11 26001 Figure 2...
Page 9: ...8 Inner Cabinet 26002 15 11 13 16 14 11 12 1 9 2 6 6 11 18 19 16 4 5 3 4 17 11 8 10 7 Figure 3...
Page 20: ...19...
Page 24: ...23...
Page 32: ...31...
Page 62: ...61...
Page 72: ...71...