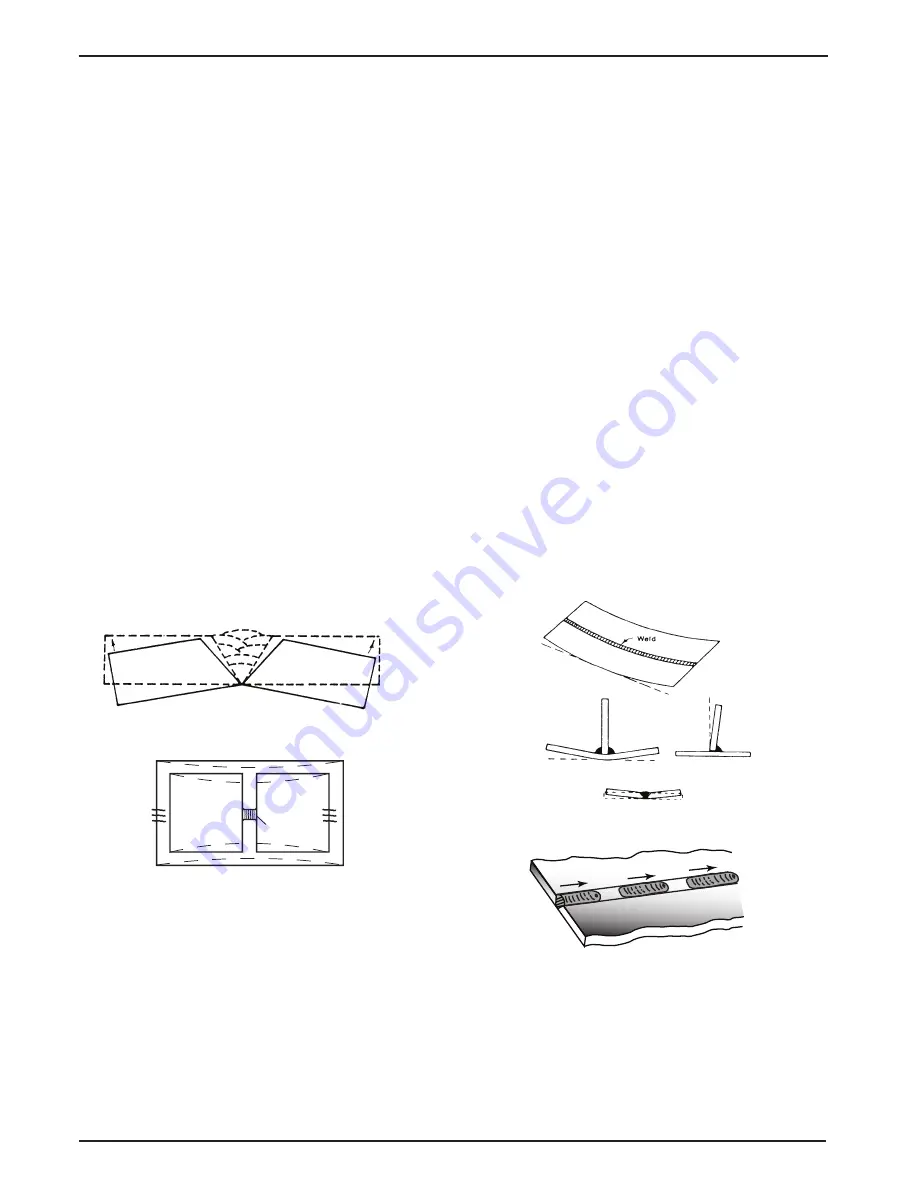
Firepower MST 140i
BASIC WELDING GUIDE
4-16
Manual 0-5338
Overcoming Distortion Effects
There are several methods of minimizing distortion effects.
A. Peening
This is done by hammering the weld while it is still hot. The weld metal is flattened slightly and because of this the tensile
stresses are reduced a little. The effect of peening is relatively shallow, and is not advisable on the last layer.
B. Distribution of Stresses
Distortion may be reduced by selecting a welding sequence which will distribute the stresses suitably so that they tend
to cancel each other out. See Figures 4-31 through 4-33 for various weld sequences. Choice of a suitable weld sequence
is probably the most effective method of overcoming distortion, although an unsuitable sequence may exaggerate it.
Simultaneous welding of both sides of a joint by two welders is often successful in eliminating distortion.
C. Restraint of Parts
Forcible restraint of the components being welded is often used to prevent distortion. Jigs, positions, and tack welds are
methods employed with this in view.
D. Presetting
It is possible in some cases to tell from past experience or to find by trial and error (or less frequently, to calculate)
how much distortion will take place in a given welded structure. By correct pre-setting of the components to be welded,
constructional stresses can be made to pull the parts into correct alignment. A simple example is shown in Figure 4-31.
E. Preheating
Suitable preheating of parts of the structure other than the area to be welded can be sometimes used to reduce distortion.
Figure 4-32 shows a simple application. By removing the heating source from b and c as soon as welding is completed,
the sections b and c will contract at a similar rate, thus reducing distortion.
Art # A-07707
Figure 4-31: Principle of Presetting
Art # A-07708
B
Preheat
Preheat
Dotted lines show effect if no preheat is used
Weld
C
Figure 4-32: Reduction of Distortion by Preheating
Art # A-07709
Figure 4-33: Examples of Distortion
Art # A-07710_AB
1
Block Sequence.
The spaces between the welds are
filled in when the welds are cool.
2
3
Figure 4-34: Welding Sequence
Summary of Contents for MST 140i
Page 6: ...This Page Intentionally Blank ...
Page 76: ...Firepower MST 140i BASIC WELDING GUIDE 4 24 Manual 0 5338 This Page Intentionally Blank ...
Page 82: ...Firepower MST 140i KEY SPARE PARTS 6 2 Manual 0 5338 6 02 Power Source Art A 12518 31 ...
Page 86: ...Firepower MST 140i KEY SPARE PARTS 6 6 Manual 0 5338 This Page Intentionally Blank ...
Page 87: ...Firepower MST 140i Manual 0 5338 1 APPENDIX APPENDIX This Page Intentionally Blank ...
Page 89: ...Firepower MST 140i Manual 0 5338 3 APPENDIX Art A 12517 ...