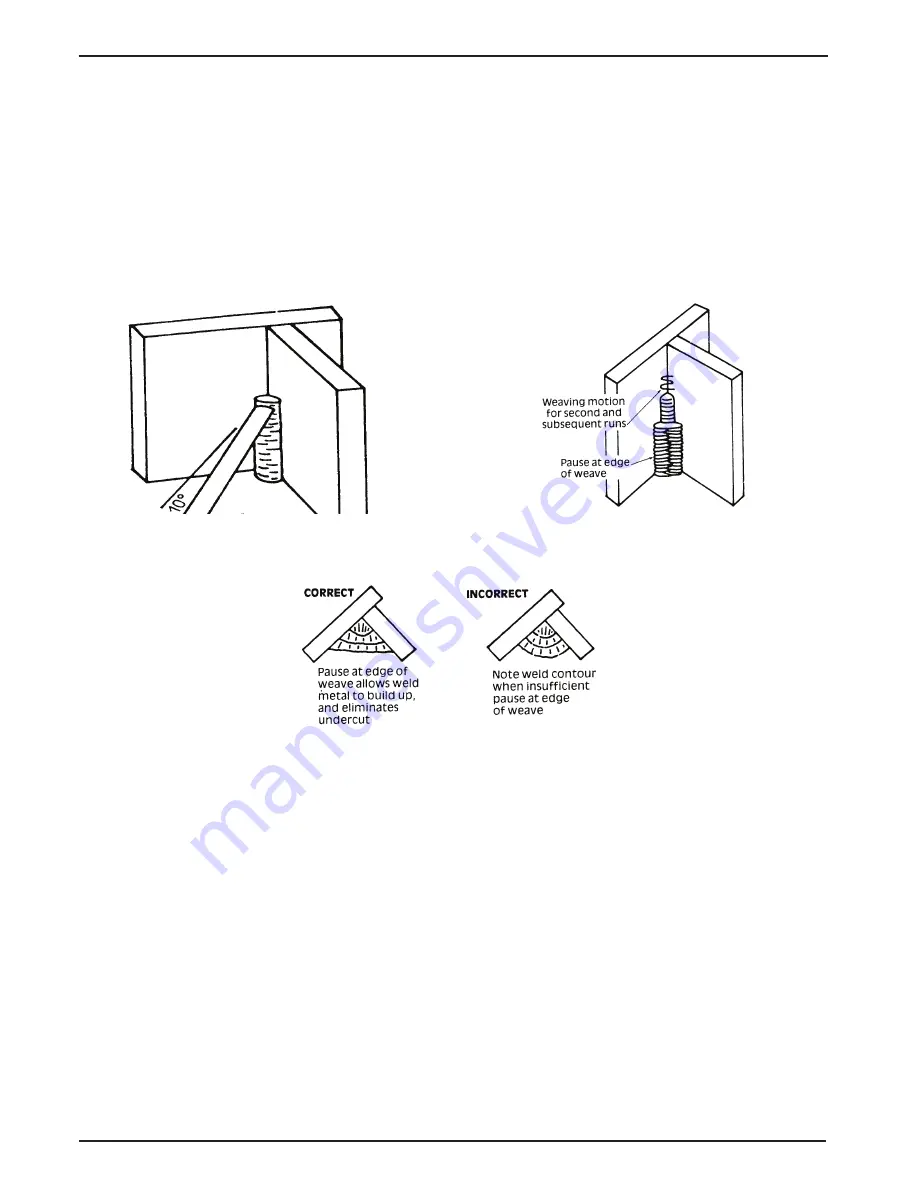
Firepower MST 140i
BASIC WELDING GUIDE
4-14
Manual 0-5338
Art # A-07701
Figure 4-25: Single Run Vertical Fillet Weld
C. Vertical Welds
1. Vertical Up
Tack weld a three feet length of angle iron to your work bench in an upright position. Use a 1/8"(3.2mm) E7014 Stick
electrode and set the current at 100 amps. Make yourself comfortable on a seat in front of the job and strike the
arc in the corner of the fillet. The electrode needs to be about 10º from the horizontal to enable a good bead to be
deposited. Refer Figure 4-25. Use a short arc, and do not attempt to weave on the first run. When the first run has
been completed de-slag the weld deposit and begin the second run at the bottom. This time a slight weaving motion
is necessary to cover the first run and obtain good fusion at the edges. At the completion of each side motion, pause
for a moment to allow weld metal to build up at the edges, otherwise undercut will form and too much metal will
accumulate in the centre of the weld. Figure 4-26 illustrates multi-run technique and Figure 4-27 shows the effects
of pausing at the edge of weave and of weaving too rapidly.
Art # A-07702
Figure 4-26: Multi Run Vertical Fillet Weld
Art # A-07703
Figure 4-27: Examples of Vertical Fillet Welds
2. Vertical Down
The
E7014 Stick electrode makes welding in this position particularly easy. Use a 1/8"(3.2mm) electrode at 100 amps.
The tip of the electrode is held in light contact with the work and the speed of downward travel is regulated so that the
tip of the electrode just keeps ahead of the slag. The electrode should point upwards at an angle of about 45º.
3. Overhead Welds
Apart from the rather awkward position necessary, overhead welding is not much more difficult that downhand welding.
Set up a specimen for overhead welding by first tacking a length of angle iron at right angles to another piece of angle
iron or a length of waste pipe. Then tack this to the work bench or hold in a vice so that the specimen is positioned
in the overhead position as shown in the sketch. The electrode is held at 45º to the horizontal and tilted 10º in the line
of travel (Figure 4-28). The tip of the electrode may be touched lightly on the metal, which helps to give a steady run.
A weave technique is not advisable for overhead fillet welds. Use a 1/8"(3.2mm) E6013 Stick electrode at 100 amps,
and deposit the first run by simply drawing the electrode along at a steady rate. You will notice that the weld deposit
is rather convex, due to the effect of gravity before the metal freezes.
Summary of Contents for MST 140i
Page 6: ...This Page Intentionally Blank ...
Page 76: ...Firepower MST 140i BASIC WELDING GUIDE 4 24 Manual 0 5338 This Page Intentionally Blank ...
Page 82: ...Firepower MST 140i KEY SPARE PARTS 6 2 Manual 0 5338 6 02 Power Source Art A 12518 31 ...
Page 86: ...Firepower MST 140i KEY SPARE PARTS 6 6 Manual 0 5338 This Page Intentionally Blank ...
Page 87: ...Firepower MST 140i Manual 0 5338 1 APPENDIX APPENDIX This Page Intentionally Blank ...
Page 89: ...Firepower MST 140i Manual 0 5338 3 APPENDIX Art A 12517 ...