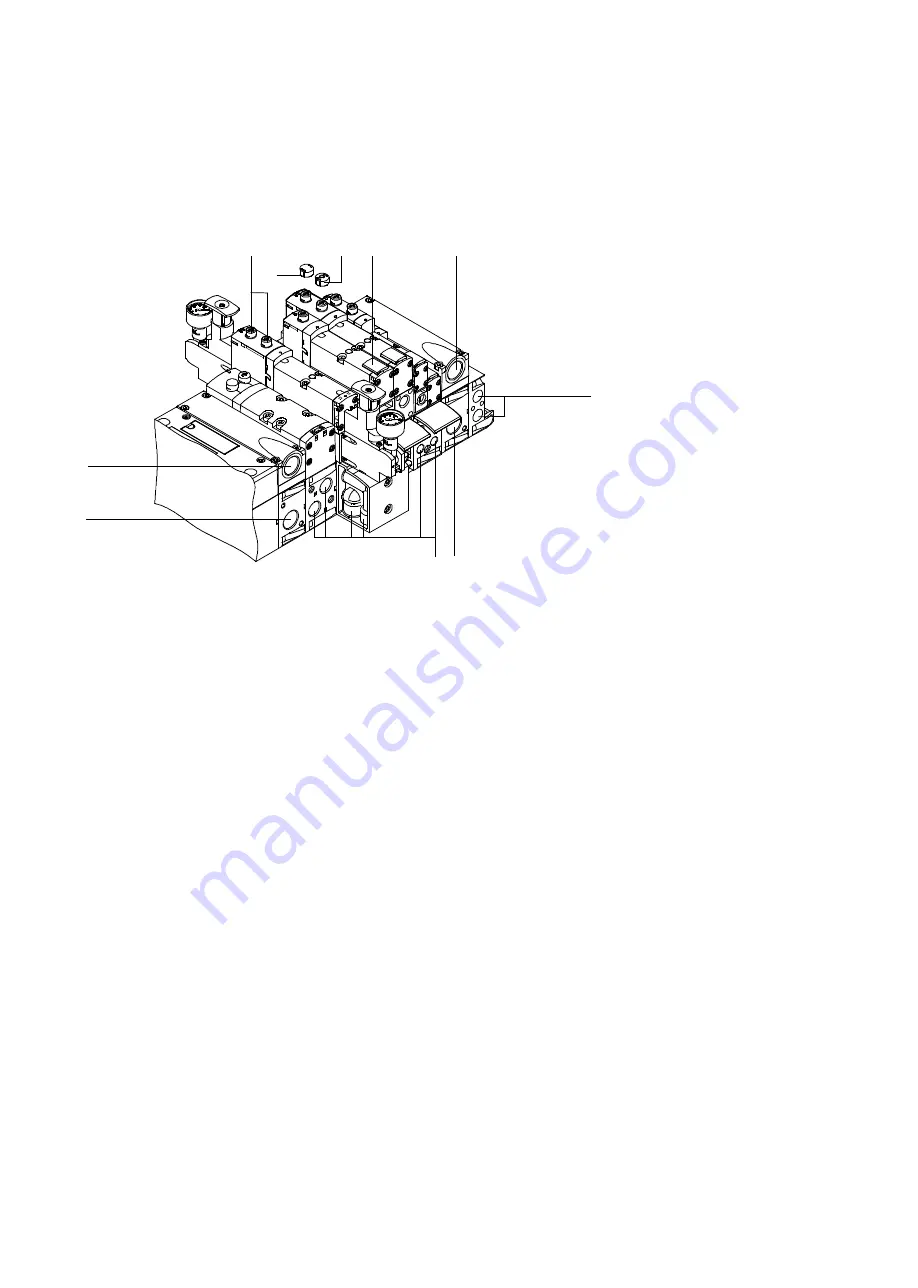
1. Summary of components
1-32
Festo P.BE-VTSA-44-EN en 1101f
You will find the following pneumatic connecting and operat-
ing elements on the VTSA... valve terminal:
8
7
1
2
3 4
5
6
7
5
1
Manual override (per pilot solenoid,
non-detenting or turning with detent)
2
Optional manual override cover cap
(manual override without function)
3
Optional manual override cover cap,
for non-detenting function of manual
override
4
Inscription fields
5
Exhaust ports “Valves” (3/5)
6
Pilot connections (12) and (14) for
supplying the external pilot air
7
Supply port (1) “Operating pressure”
8
Working lines (2) and (4), per valve
position
Fig. 1/8:
Pneumatic Connection, display and operating elements of the basic components,
Widths 18 ... 52 mm
Summary of Contents for VTSA-44-ASI Series
Page 2: ......
Page 16: ...Contents and general instructions XIV Festo P BE VTSA 44 EN en 1101f ...
Page 17: ...Summary of components 1 1 Festo P BE VTSA 44 EN en 1101f Chapter 1 Summary of components ...
Page 63: ...Fitting 2 1 Festo P BE VTSA 44 EN en 1101f Chapter 2 Fitting ...
Page 79: ...Installation 3 1 Festo P BE VTSA 44 EN en 1101f Chapter 3 Installation ...
Page 89: ...3 Installation 3 11 Festo P BE VTSA 44 EN en 1101f 1 2 4 3 Fig 3 2 Removing the tubing ...
Page 125: ...Commissioning 4 1 Festo P BE VTSA 44 EN en 1101f Chapter 4 Commissioning ...
Page 142: ...4 Commissioning 4 18 Festo P BE VTSA 44 EN en 1101f ...
Page 167: ...Technical appendix A 1 Festo P BE VTSA 44 EN en 1101f Appendix A Technical appendix ...
Page 210: ...B Supplementary component summary B 18 Festo P BE VTSA 44 EN en 1101f ...
Page 211: ...Index C 1 Festo P BE VTSA 44 EN en 1101f Appendix C Index ...
Page 212: ...C Index C 2 Festo P BE VTSA 44 EN en 1101f Contents C Stichwortverzeichnis C 1 ...
Page 220: ...C Index C 10 Festo P BE VTSA 44 EN en 1101f ...