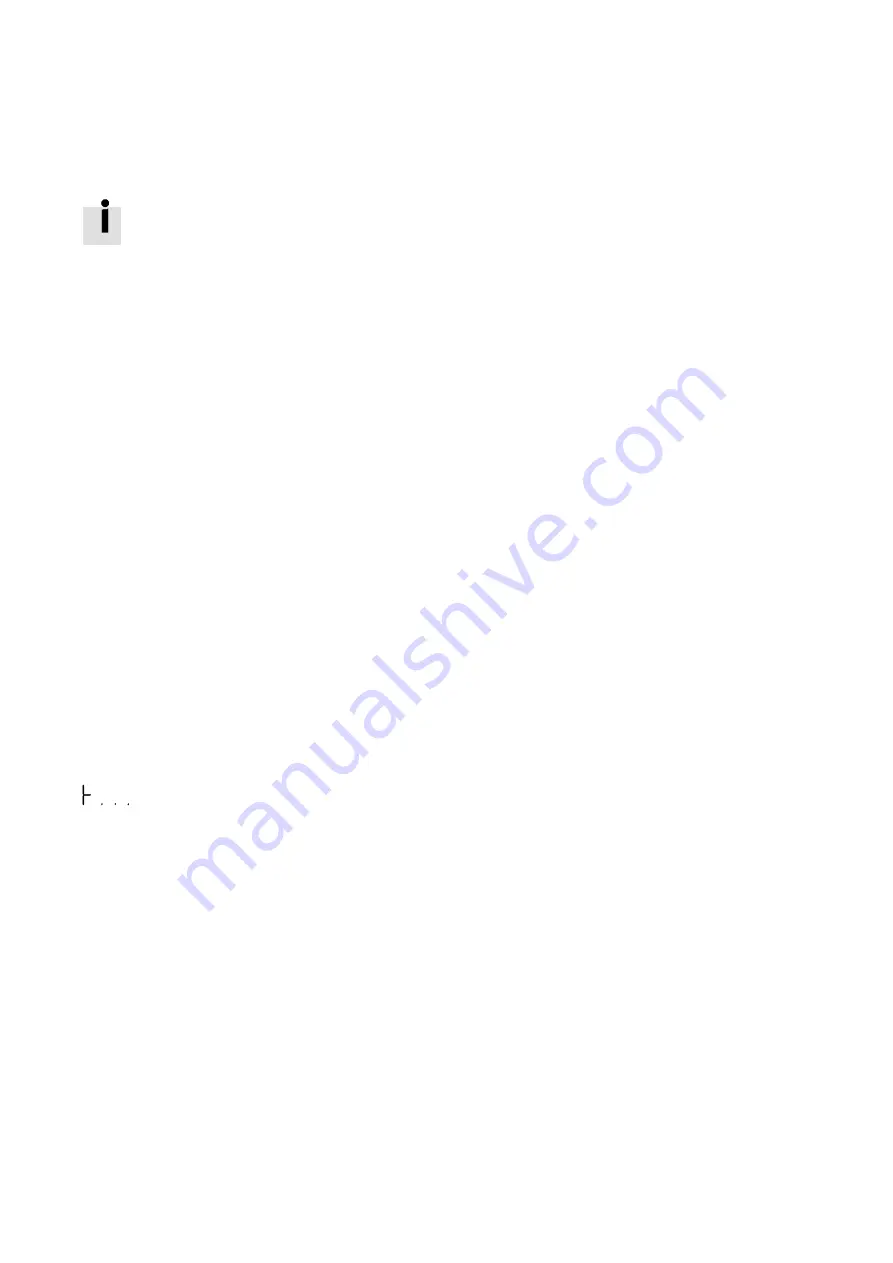
6. Testing parts with the Checkbox
6-12
Festo P.BE-Checkbox-EN en 0103c
If the quality check and the position recognition for the parts
assortment is not sastisfactory, you can use aditional operat-
ing parameters and tools with CheckOpti, in order to optimize
the test results. Please consult your technical advisor in this
respect.
6.2.2 Visual check
Check the test results e.g. according to the following points of
view:
–
Have the orientations been recognized correctly?
–
Is the grading of the parts recognized as good/bad correct?
Use the sample parts to check the test parts with regard
to their grading. If you have also checked faulty parts,
check whether these have actually been recognized as
bad.
–
Use as many test parts as possible to make sure that they
are correctly output at the delivery positions for good,
bad or incorrectly orientated parts.
Note the explanations on the test procedure in the following
chapter sections 6.2.3 and 6.2.4. If necessary, optimize the
test result via the influence of the tolerance (chapter 6.2.5).
6.2.3 Checking the features
The individual features of the test parts differ from the aver-
age values of the sample part features. The Checkbox ascer-
tains for each test part the feature which deviates the most
(maximum deviation).
During the test procedure you can see this test part deviation
for 1.5 seconds in the TOLERANCE display.
Summary of Contents for Checkbox Identbox
Page 1: ...Manual Checkbox Identbox Countbox Sortbox Manual 526 373 649 320 en 0103c The Checkbox family...
Page 2: ......
Page 4: ...Contents and general instructions II Festo P BE Checkbox EN en 0103c...
Page 8: ...Contents and general instructions VI Festo P BE Checkbox EN en 0103c...
Page 18: ...Contents and general instructions XVI Festo P BE Checkbox EN en 0103c...
Page 19: ...System summary 1 1 Festo P BE Checkbox EN en 0103c Chapter 1...
Page 33: ...Fitting and Installation 2 1 Festo P BE Checkbox EN en 0103c Chapter 2...
Page 49: ...The I O module on the Checkbox 3 1 Festo P BE Checkbox EN en 0103c Chapter 3...
Page 71: ...Commissioning 4 1 Festo P BE Checkbox EN en 0103c Chapter 4...
Page 79: ...Teaching parts with the Checkbox 5 1 Festo P BE Checkbox EN en 0103c Chapter 5...
Page 91: ...Testing parts with the Checkbox 6 1 Festo P BE Checkbox EN en 0103c Chapter 6...
Page 109: ...Maintenance 7 1 Festo P BE Checkbox EN en 0103c Chapter 7...
Page 115: ...Technical appendix A 1 Festo P BE Checkbox EN en 0103c Appendix A...
Page 142: ...A Technical appendix A 28 Festo P BE Checkbox EN en 0103c...
Page 143: ...Brief instructions B 1 Festo P BE Checkbox EN en 0103c Appendix B...
Page 144: ...B Brief instructions B 2 Festo P BE Checkbox EN en 0103c Contents B Brief instructions B 1...
Page 151: ...Index C 1 Festo P BE Checkbox EN en 0103c Appendix C...
Page 152: ...C Index C 2 Festo P BE Checkbox EN en 0103c Contents C Index C 1...