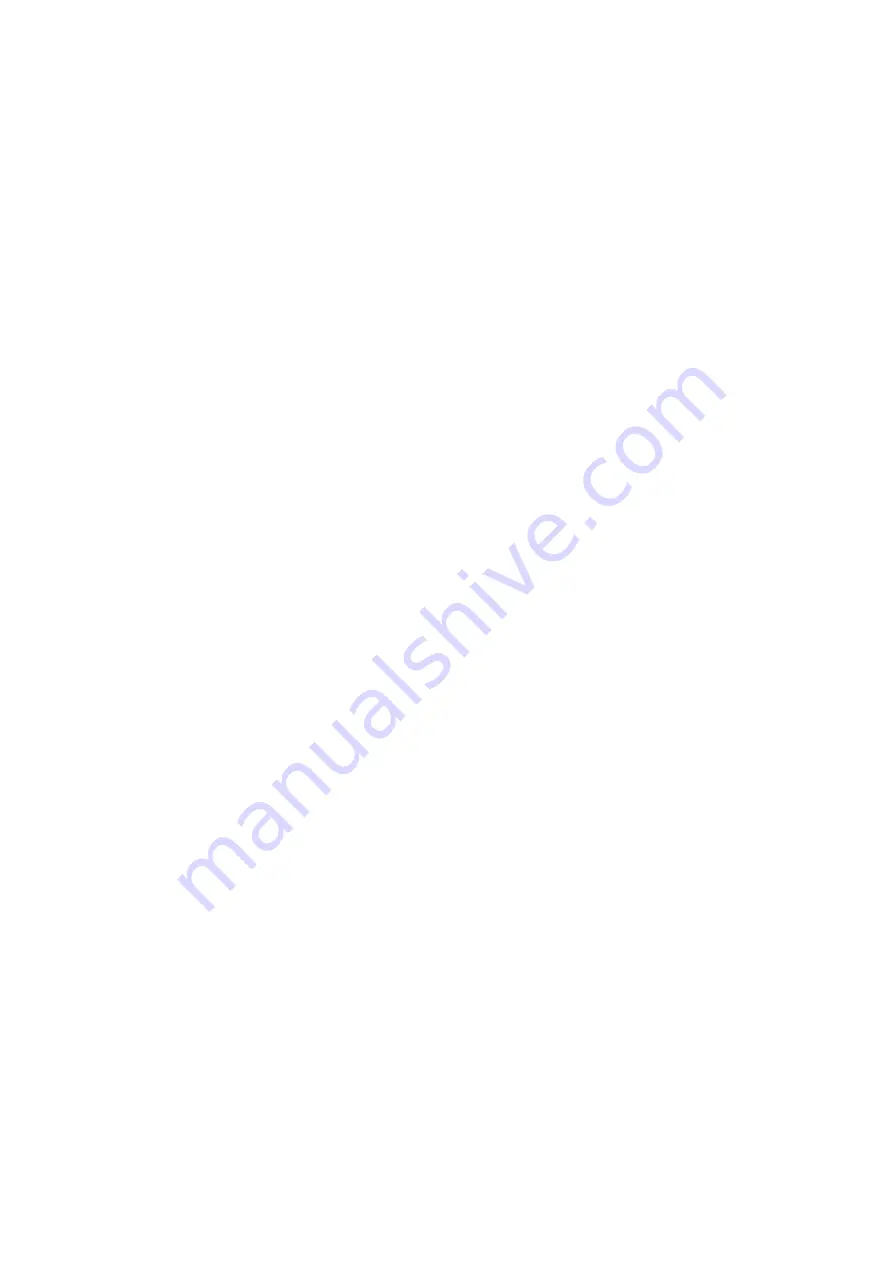
B 4
Engine:
The paver is powered by a 6-cylinder, water cooled diesel engine with direct injection and a
turbo charger. Electric starting and belt driven alternator battery charging is standard. The engine
power / rpm is controlled by the engine speed control on either of the consoles. The engine is shut
down either by removing the key “ON/OFF” switch or the emergency stop switch. For further details,
see the technical data in the engine’s instruction manual.
Track:
The two rubber tracks are driven indepently of each other. They are each direct drive requiring
less maintenance and service than chain driven machines. Each track is adjusted automatically using
hydraulic pressure. The rubber track allows the machine to attain a high transportation speed with
excellent maneuverability and traction.
Hydraulic system:
The diesel engine has the Pump Drive gear box attached to it. This drives the
hydraulic pumps for all the main and auxiliary paver functions. The hydraulic system also drives the
generator needed to heat materials to prevent the material from sticking to the screed plate. All power
on the paver comes from hydraulics.
Track drive:
The closed-loop track drive system includes two speed track drive motors that are
connected to the drive pumps by means of high pressure hydraulic hoses. The hydraulic motors are
mounted to the track drive wheels and mobilize the tracks. Track movement is controlled by directional
control joysticks on the consoles.
Steering system/operator’s platform:
The independent hydrostatic travel drives allow the paver to
be turned on the spot. The electronic synchronization, controlled from the operating panel, ensures that
the paver runs straight ahead. The operating panels can be secured in variable positions on both left
and right console panels, by a locking mechanism.
Steering is accomplished merely by driving one track at a different speed than one other. If turning left,
the track on the right hand side will move faster than the track on the left. If turning right, the track on
the left hand side will move faster than the track on the right.
Push roller crossbar:
The push rollers for material trucks are connected to a crossbar that pivots at its
center. This crossbar allows for differences in distances to the rear wheels on a variety of material
trucks. This permits the paver to deviate less from its course and makes paving curves easier.
Material compartment (hopper):
The hopper inlet is equipped with a conveyor system that empties
the hopper and transfers the material to the auger. The hopper can hold approximately 30,000 lbs.
(13608 kg) and are raised hydraulically to empty onto the conveyor chains. To facilitate the emptying
and to improve material transfer, each of the lateral covers of the hopper are hydraulically moved.
Conveyors (Material transfer):
The paver is equipped with two conveyors driven separately with
pressure from a single pump. The system consists of a single, pressure compensated, load sense style,
variable displacement, open loop pump driving two fixed volume hydraulic motors. This pump supplies
hydraulic power for both conveyors of the machine and provides power for the cylinders on the
machine.
These conveyors transfer the material from the hopper to the augers. By using sensors to monitor the
Summary of Contents for DYNAPAC F1000T T4f
Page 2: ...www G QDSDF com ...
Page 20: ...B 12 5 Location of instruction labels and identification plates ...
Page 27: ...B 19 ...
Page 31: ...C 4 ...
Page 36: ...C 9 ...
Page 38: ...C 11 3 2 Driving mode ...
Page 45: ...D 2 2 Controls 2 1 Operating panel Left Hand Operator s Panel Right Hand Operator s Panel ...
Page 49: ...D 6 PANEL B Left Hand Operator s Panel Right Hand Operator s Panel ...
Page 51: ...D 8 PANEL B Left Hand Operator s Panel Right Hand Operator s Panel ...
Page 53: ...D 10 PANEL B Left Hand Operator s Panel Right Hand Operator s Panel ...
Page 55: ...D 12 PANEL C ...
Page 57: ...D 14 PANEL C 45 40 49 42 41 47 44 43 48 ...
Page 59: ...D 16 PANEL C 45 40 49 42 41 47 44 43 48 ...
Page 61: ...D 18 PANEL D 53 52 54 51 55 50 53 52 51 50 ...
Page 63: ...D 20 PANEL D 53 52 54 51 55 50 53 52 51 50 ...
Page 65: ...D 22 PANEL D 53 52 54 51 55 50 53 52 51 50 ...
Page 67: ...D 24 PANEL E 56 57 58 ...
Page 69: ...D 26 PANEL E 56 57 58 ...
Page 71: ...D 28 PANEL E 56 57 58 ...
Page 73: ...D 30 3 Auxiliary functions 60 61 62 63 ...
Page 86: ...D 43 Left right handset 101 103 105 107 104 106 102 100 ...
Page 88: ...D 45 101 103 105 107 104 106 102 100 ...
Page 107: ...D 64 1 2 Engine Error messages ...
Page 108: ...D 65 ...
Page 109: ...D 66 ...
Page 110: ...D 67 ...
Page 111: ...D 68 ...
Page 112: ...D 69 ...
Page 113: ...D 70 ...
Page 114: ...D 71 ...
Page 115: ...D 72 ...
Page 116: ...D 73 ...
Page 117: ...D 74 ...
Page 118: ...D 75 ...
Page 119: ...D 76 ...
Page 120: ...D 77 ...
Page 121: ...D 78 ...
Page 122: ...D 79 ...
Page 123: ...D 80 ...
Page 124: ...D 81 ...
Page 125: ...D 82 ...
Page 126: ...D 83 ...
Page 127: ...D 84 ...
Page 128: ...D 85 ...
Page 129: ...D 86 ...
Page 130: ...D 87 ...
Page 131: ...D 88 ...
Page 132: ...D 89 ...
Page 133: ...D 90 ...
Page 134: ...D 91 ...
Page 135: ...D 92 ...
Page 136: ...D 93 ...
Page 137: ...D 94 ...
Page 138: ...D 95 ...
Page 139: ...D 96 ...
Page 140: ...D 97 ...
Page 141: ...D 98 ...
Page 142: ...D 99 ...
Page 143: ...D 100 ...
Page 144: ...D 101 ...
Page 145: ...D 102 ...
Page 146: ...D 103 ...
Page 147: ...D 104 ...
Page 159: ...D 116 ...
Page 161: ...D 118 ...
Page 163: ...D 120 ...
Page 165: ...D 122 ...
Page 168: ...D 125 ...
Page 170: ...D 127 ...
Page 173: ...D 130 ...
Page 175: ...D 132 ...
Page 193: ...E 11 ...
Page 195: ...F 2 F 2 0 Maintenance overview 1 Maintenance overview ...
Page 197: ...F 4 F 3 0 Maintenance Conveyor and Hopper 1 Maintenance Conveyor and hopper ...
Page 205: ...F 12 F 4 0 Maintenance Auger 1 Maintenance Auger ...
Page 211: ...F 18 F 5 0 Maintenance Engine 1 Maintenance engine sub unit ...
Page 226: ...F 31 F 6 0 Maintenance Hydraulic System 1 Maintenance hydraulic system ...
Page 237: ...F 42 F 7 0 Maintenance Track 1 Maintenance running gear ...
Page 246: ...F 51 F 8 0 Maintenance Electronic System 1 Maintenance Electronic system ...
Page 256: ...F 61 F 10 0 Checks Decommissioning 1 Tests check up cleaning stopping ...