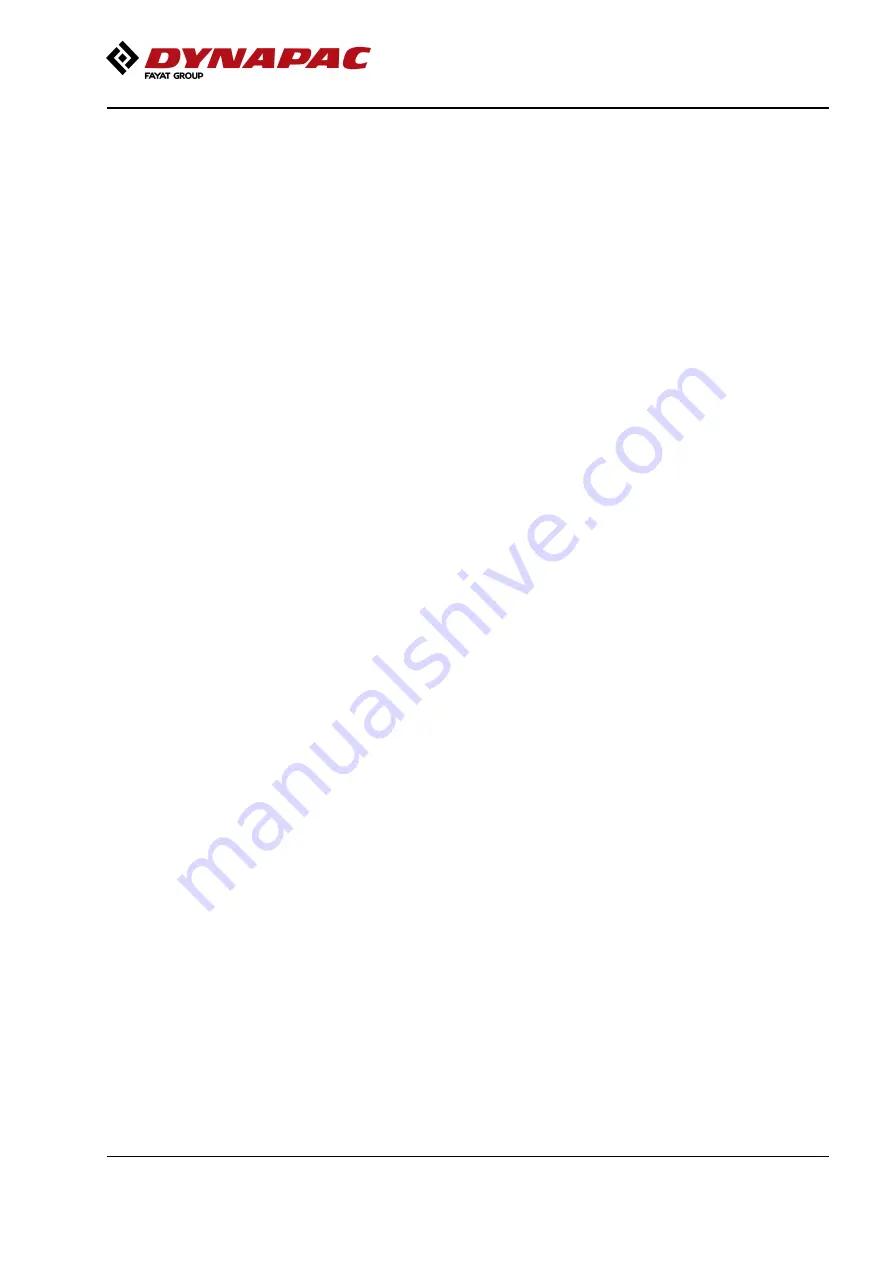
Preventive maintenance
4812165801.pdf
2024-04-22
Preventive maintenance
Complete maintenance is necessary for
the machine to function satisfactorily and at the lowest
possible cost.
The Maintenance section includes the periodic
maintenance that must be carried out on the machine.
The recommended maintenance intervals assume that
the machine is used in a normal environment and
working conditions.
Acceptance and delivery inspection
The machine is tested and adjusted before it leaves
the factory.
On arrival, before delivery to the customer, delivery
inspection must be conducted as per the check list in
the warranty document.
Any transport damage must be reported immediately
to the transport company, as this is not covered by the
product warranty.
Warranty
The warranty is only valid if the stipulated delivery
inspection and the separate service inspection have
been completed as per the warranty document, and
when the machine has been registered for starting
under the warranty.
The warranty is not valid if damage has been caused
by inadequate service, incorrect use of the machine,
the use of lubricants and hydraulic fluids other than
those specified in the manual, or if any other
adjustments have been made without
the requisite authorization.
111
Summary of Contents for DYNAPAC CX8
Page 2: ......
Page 12: ...e 4812165801 pdf 2024 04 22 Compressor Replacing V belt 166...
Page 16: ...Introduction 4812165801 pdf 2024 04 22 4...
Page 36: ...Technical specifications 4812165801 pdf 2024 04 22 24...
Page 46: ...Machine description 4812165801 pdf 2024 04 22 4812129673 Warning CALIFORNIA Proposition 65 34...
Page 72: ...Machine description 4812165801 pdf 2024 04 22 60...
Page 110: ...Operation 4812165801 pdf 2024 04 22 98...
Page 140: ...Maintenance Every 10h 4812165801 pdf 2024 04 22 128...
Page 142: ...Maintenance Every 50h 4812165801 pdf 2024 04 22 130...
Page 146: ...Maintenance Every 250h 4812165801 pdf 2024 04 22 134...
Page 164: ...Maintenance Every 1000h 4812165801 pdf 2024 04 22 152...
Page 179: ......
Page 180: ...Dynapac Compaction Equipment AB Box 504 SE 371 23 Karlskrona Sweden www dynapac com...