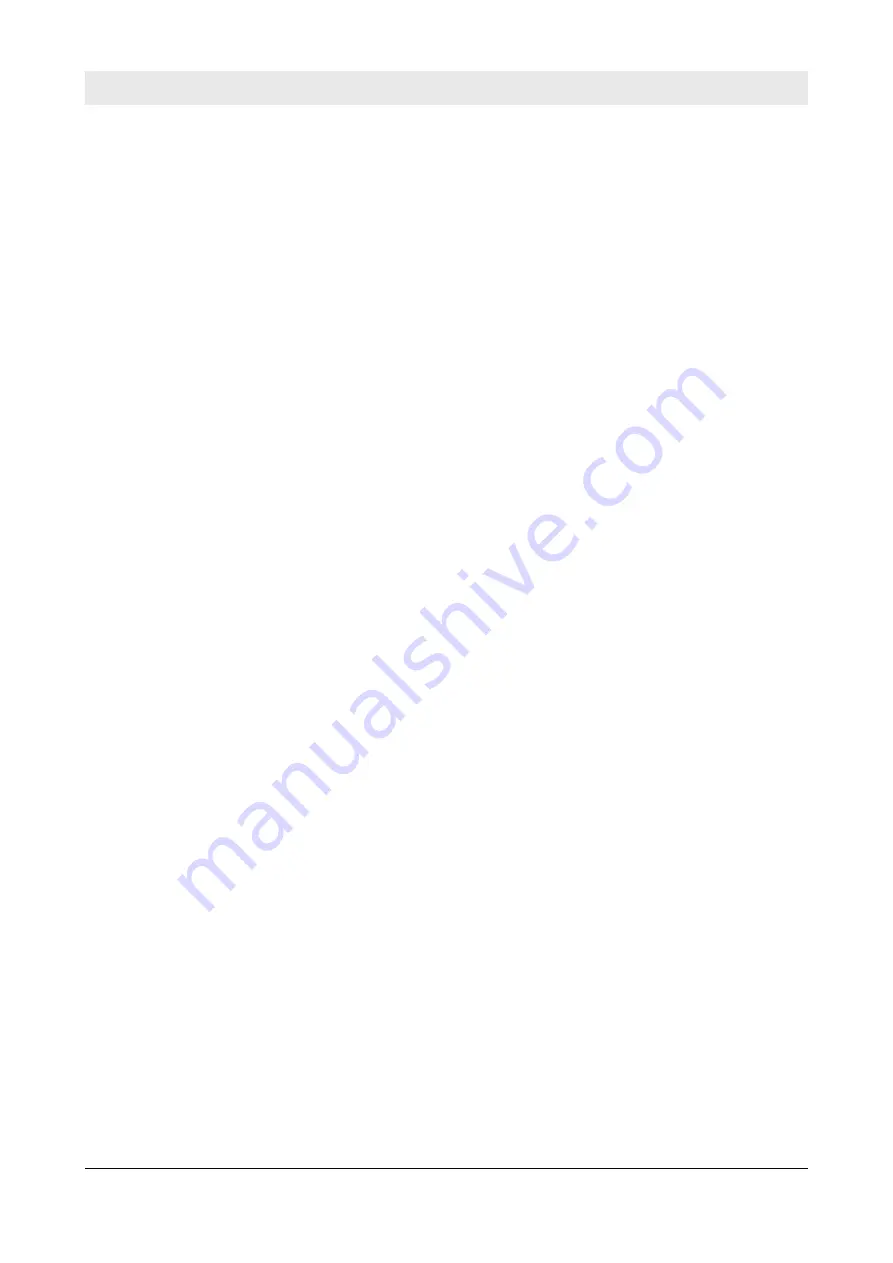
Driving across slopes should therefore be
strictly avoided, because of the high risk of tip-
ping over and the related risk of severe or even
fatal accidents.
For rollers with a drum width of 1 meter or less
there is a considerable risk of tipping over near
edges (e.g. curbstones, embankments,
trenches, potholes) when driving over these
edges.
3.7.4 Working with vibration
When compacting with vibration you must
always check the effect of the vibration on
nearby buildings and underground supply lines
(gas, water, sewage, electric power). If neces-
sary stop compacting with vibration.
Do not activate the vibration on hard (frozen,
concrete) ground. Components may get dam-
aged.
3.7.5 Parking the machine
Park the machine on horizontal, level, firm
ground.
Before leaving the machine:
n
shift all control levers to “Neutral position”,
“Off” or “0”,
n
apply the parking brake,
n
shut down the engine, pull off the ignition
key,
n
pull off the main battery switch,
n
secure the machine against unauthorized
use.
Do not jump off the machine, but use hand
grips and access steps.
Concerning your safety – Driving the machine; working operation
BW 100 ADM-5
46
Summary of Contents for BOMAG BW 100 ADM-5
Page 9: ...1 Introduction Introduction BW 100 ADM 5 9 ...
Page 13: ...2 Technical data Technical data BW 100 ADM 5 13 ...
Page 18: ...Technical data Noise and vibration data BW 100 ADM 5 18 ...
Page 19: ...3 Concerning your safety Concerning your safety BW 100 ADM 5 19 ...
Page 65: ...4 Indicators and control elements Indicators and control elements BW 100 ADM 5 65 ...
Page 82: ...Indicators and control elements Outside of machine BW 100 ADM 5 82 ...
Page 83: ...5 Checks prior to start up Checks prior to start up BW 100 ADM 5 83 ...
Page 97: ...6 Operation Operation BW 100 ADM 5 97 ...
Page 128: ...Operation Emergency procedures BW 100 ADM 5 128 ...
Page 129: ...7 Loading transporting the machine Loading transporting the machine BW 100 ADM 5 129 ...
Page 139: ...8 Maintenance Maintenance BW 100 ADM 5 139 ...
Page 194: ...Maintenance As required BW 100 ADM 5 194 ...
Page 195: ...9 Setting up refitting Setting up refitting BW 100 ADM 5 195 ...
Page 200: ...Setting up refitting Edge cutter mounting and removing tools BW 100 ADM 5 200 ...
Page 201: ...10 Troubleshooting Troubleshooting BW 100 ADM 5 201 ...
Page 206: ...Fuse Amperage Designation F00 80 A Main fuse Troubleshooting Fuse assignment BW 100 ADM 5 206 ...
Page 212: ...Troubleshooting Trouble shooting ECONOMIZER BW 100 ADM 5 212 ...
Page 213: ...11 Disposal Disposal BW 100 ADM 5 213 ...
Page 215: ......
Page 216: ......