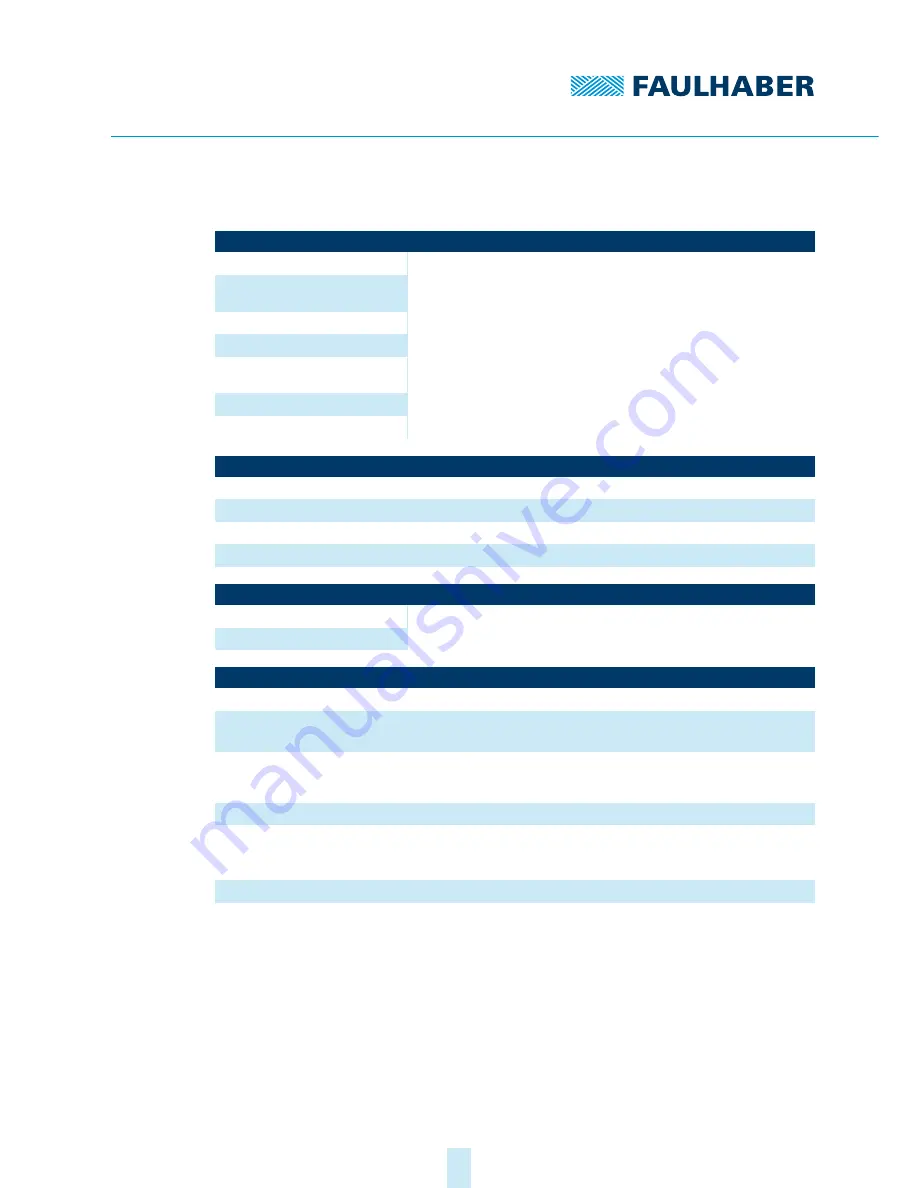
1st edition, 03-05-2018
7000.05063, 1st edition, 03-05-2018
7000.05063
Product description
16
3.3
Technical data
Dimensioning limits
Power supply of the electronics
See chap. 8.1, p. 60
Motor power supply (not if using
the motherboard)
PWM switching frequency
Electronics efficiency
Maximum continuous output cur-
rent
Maximum peak output current
Standby current of the electronics
Operating and storage conditions
Ambient temperature range
See chap. 8.1, p. 60
Relative air humidity
5…93 % (non-condensing)
Maximum operating altitude
2000 m above sea level
Pollution degree
2, acc. to DIN EN 61010
Dimensions and mass
Dimensioned drawing
See chap. 8.1, p. 60
Ground
Safety
Safety integrity level
SIL 3, acc. to IEC 61800-5-2 / EN 62061
Performance level
PL e (with separate switching of the STO inputs), acc. to EN 13849
Outage rate
a)
: PFH
D
= 4,57 × 10
-10
a)
Assumed as the basis of the calculation of the outage rates was a demand rate of 1 per 8 hours
Maximum time between the
request of the safe state and the
shutdown of the output signals
5 ms
Overvoltage category
III, acc. to DIN EN 60664-1
Decisive voltage class
DVC A, acc. to DIN EN 61800-5-1
Adjacent circuits require functional insulation (DVC A), basic insulation
(DVC B) or electrical separation (DVC C)
Protection class
Housings must be suitable for use in the intended environment.
Summary of Contents for MC 5004 P STO
Page 1: ...WE CREATE MOTION Installation Instructions MC 5004 P STO Original Instructions EN ...
Page 64: ...1st edition 03 05 2018 7000 05063 1st edition 03 05 20187000 05063 Additional documents 64 ...
Page 65: ...1st edition 03 05 2018 7000 05063 1st edition 03 05 20187000 05063 Additional documents 65 ...
Page 67: ...1st edition 03 05 2018 7000 05063 1st edition 03 05 20187000 05063 Additional documents 67 ...
Page 68: ...1st edition 03 05 2018 7000 05063 1st edition 03 05 20187000 05063 Additional documents 68 ...