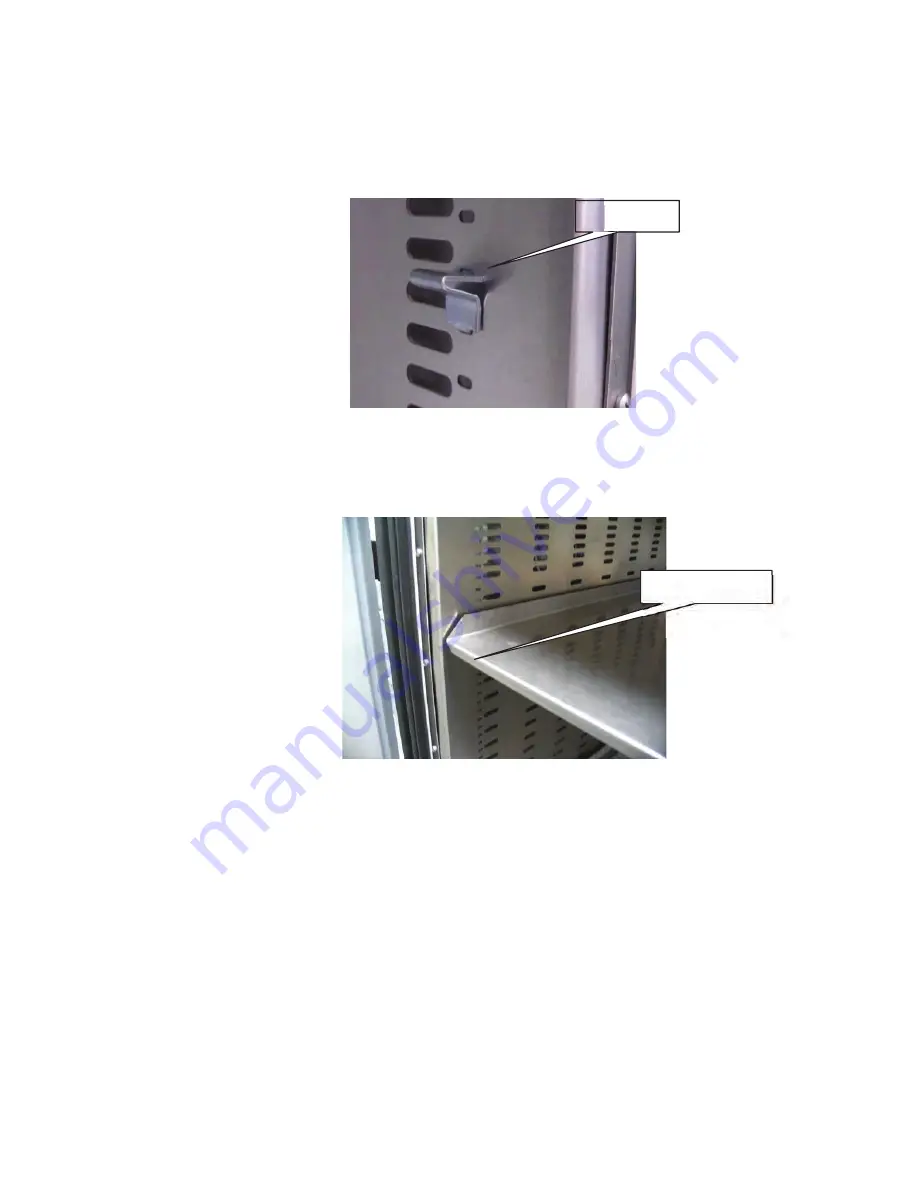
4000
Ͳ
LC
Series
D4580880
Ͳ
01
Page
10
of
61
8.
Install (4) shelf clips in the duct sheet for each shelf (2) front
and (2) in rear at the desired height. Spacing is
approximately 0.5” (1.3 cm) for each shelf.
9.
Place the shelves on the clips with the down flange facing the door
opening. (see photo below)
Shelf
down
flange
Shelf
Clip