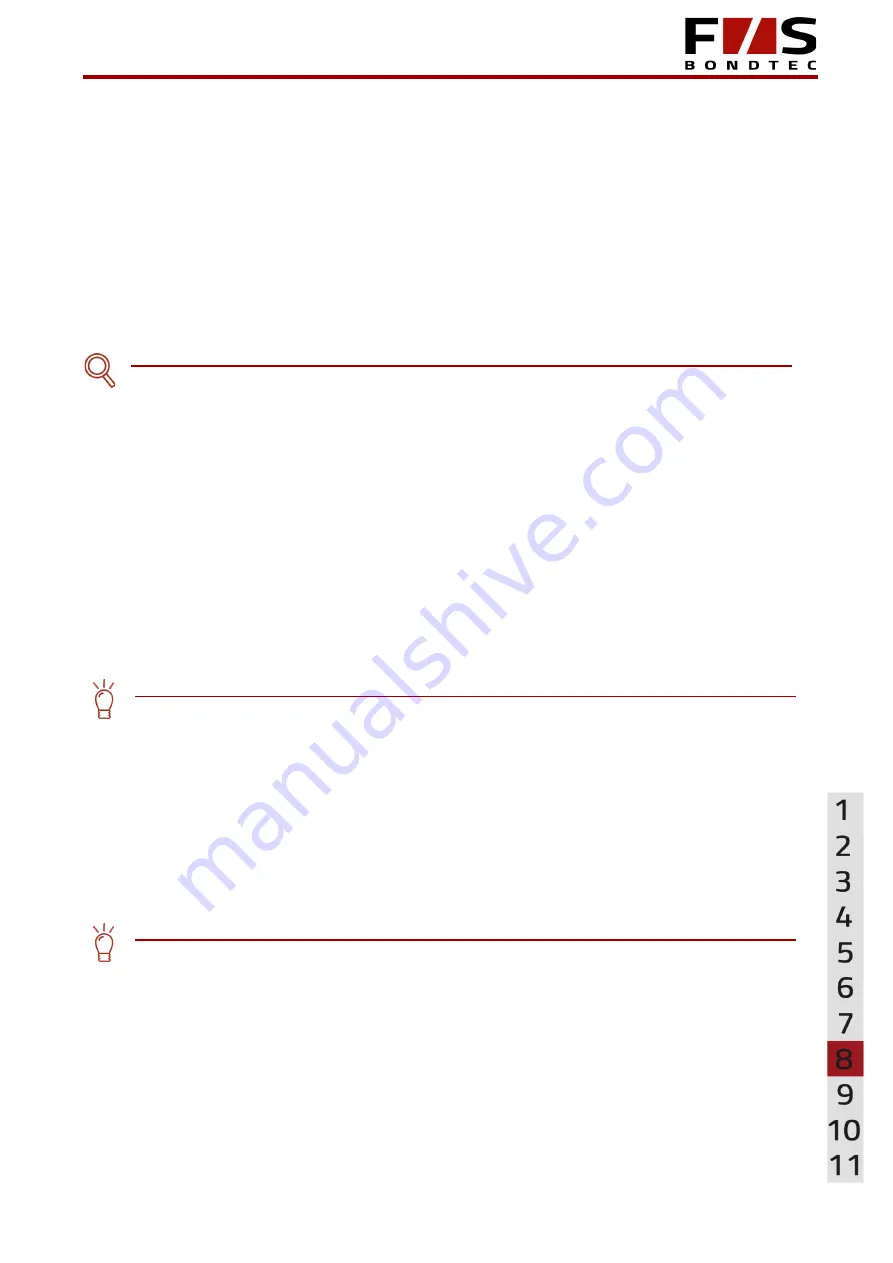
Process Optimization
© 2020 F&S BONDTEC Semiconductor GmbH. All rights reserved.
31
8.1.3 Bondforce
The bondforce is primarily dependent on the wire diameter used. In the thin wire range (18-75µm diameter) one can
assume that the suitable setting of the bondforce (for bondable surfaces) will be approximately equal to the wire dia-
meter. The bondforce is constant over the entire bonding time.
For heavy wire (100-500µm diameter) the bond force should be increased continuously during the entire bonding
process.
To do this, you must activate <Bondforce Ramp>. Then you can enter the time of the ramp and the force at the end
of the bonding process.
You can also orientate yourself on the wire diameter used.
In most cases, the appropriate setting for Bondforce should be selected according to the wire diameter. The force at
the end of the ramp should be approximately twice the wire diameter.
TIP
If the edges of the bonding area are dark colored when Al wire is bonded, the ratio of US Power and Bond-
force is not correct and the edges of the bonding area will burn because the bonding tool rubs against the
surface of the wire instead of rubbing the wire over the surface of the component. (too much US Power with
too little Bondforce)
As a result, an Al deposit will also form very quickly on the bonding tool and premature wear of the bonding
tool will occur.
8.1.4 Touchdown Steps
The TD Steps create the area to deform the wire during the bonding process. As a guideline, half the wire diameter is
used.
IMPORTANT!
The rules are slightly different when it comes to ball bonding, because the wire diameter must be set on the
1st bond and half the wire diameter on the 2nd bond. This is necessary because the ball created at the end
of the wire during flaming has a much larger diameter than the wire.
The TD Steps will move the Z-axis further down by the programmed distance after the bond tool has been set up. At
this point the bonding tool has already touched down on the component, the entire transducer holder is lifted and a
gap is created between the transducer holder and the lower stop of the transducer holder.
IMPORTANT!
The wire is not yet deformed when the Z-axis is passed over.
If the bonding process is started afterwards, the wire is deformed by the applied bonding force and by US power.
The transducer holder sinks to the bottom and the gap, that was previously created when the wire was passed over,
is reduced again.
This reduction of the gap is displayed graphically on the monitor as DLC curves (DeformationsLimitControl).