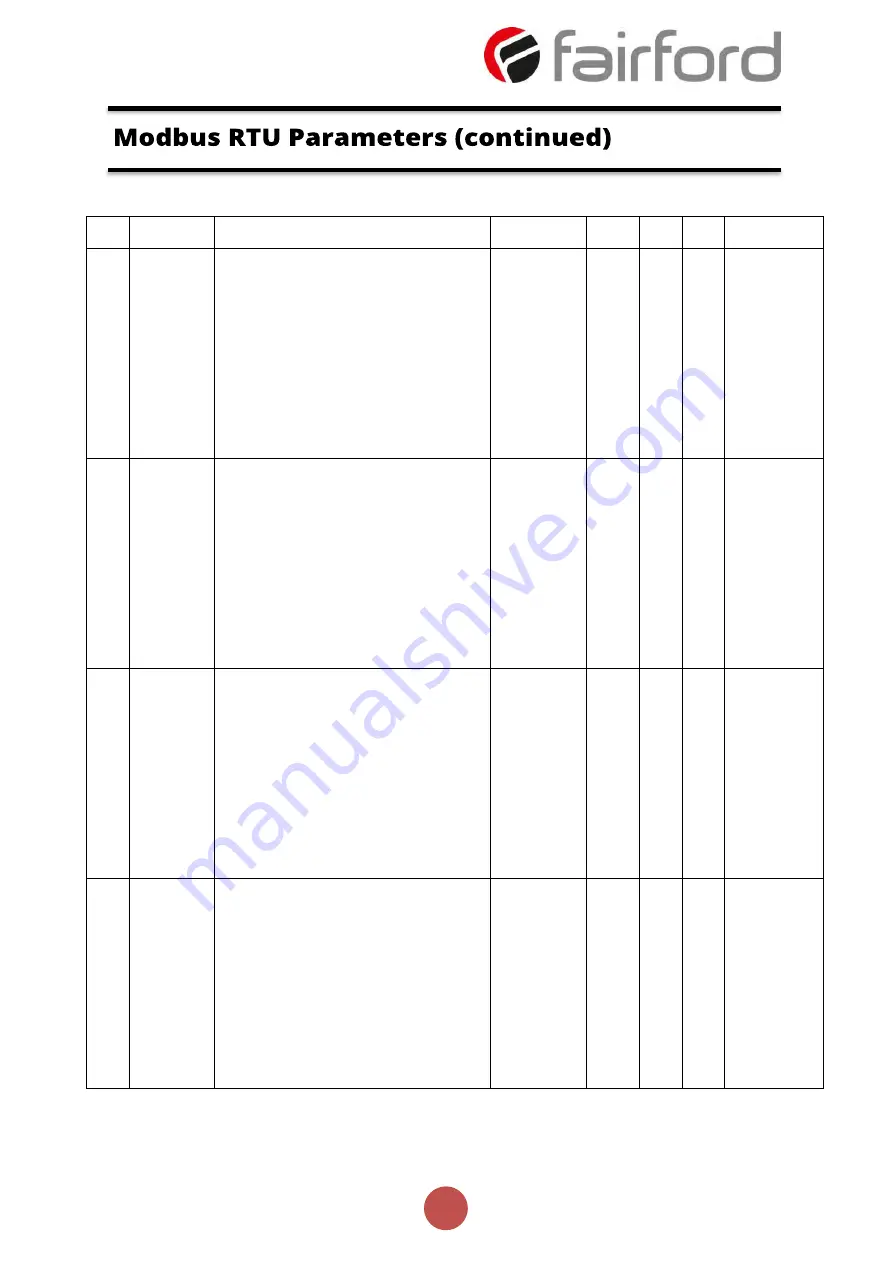
60
agility
TM
Series Soft Start User Manual
MAN-AGY-001. Version 04. 21/09/2018
PNU Name
Description
Options
Words Type Units Detail
98
Total Events The total number of events that have been
recorded in the log file
2
R
Multiplier: 1
Divisor:1
Offset: 0
Min: 0
Max: 65535
Default: 0
103 AGY200 Ver The hardware version for Main PCB
1
R
Multiplier: 1
Divisor:1
Offset: 0
Min: 0
Max: 65535
Default: 1
104 AGY300 Ver The hardware version for Power PCB
1
R
Multiplier: 1
Divisor:1
Offset: 0
Min: 0
Max: 65535
Default: 1
106 Total Uc On The total number times the start command
has been applied
2
R
Multiplier: 1
Divisor:1
Offset: 0
Min: 0
Max: 65535
Default: 0