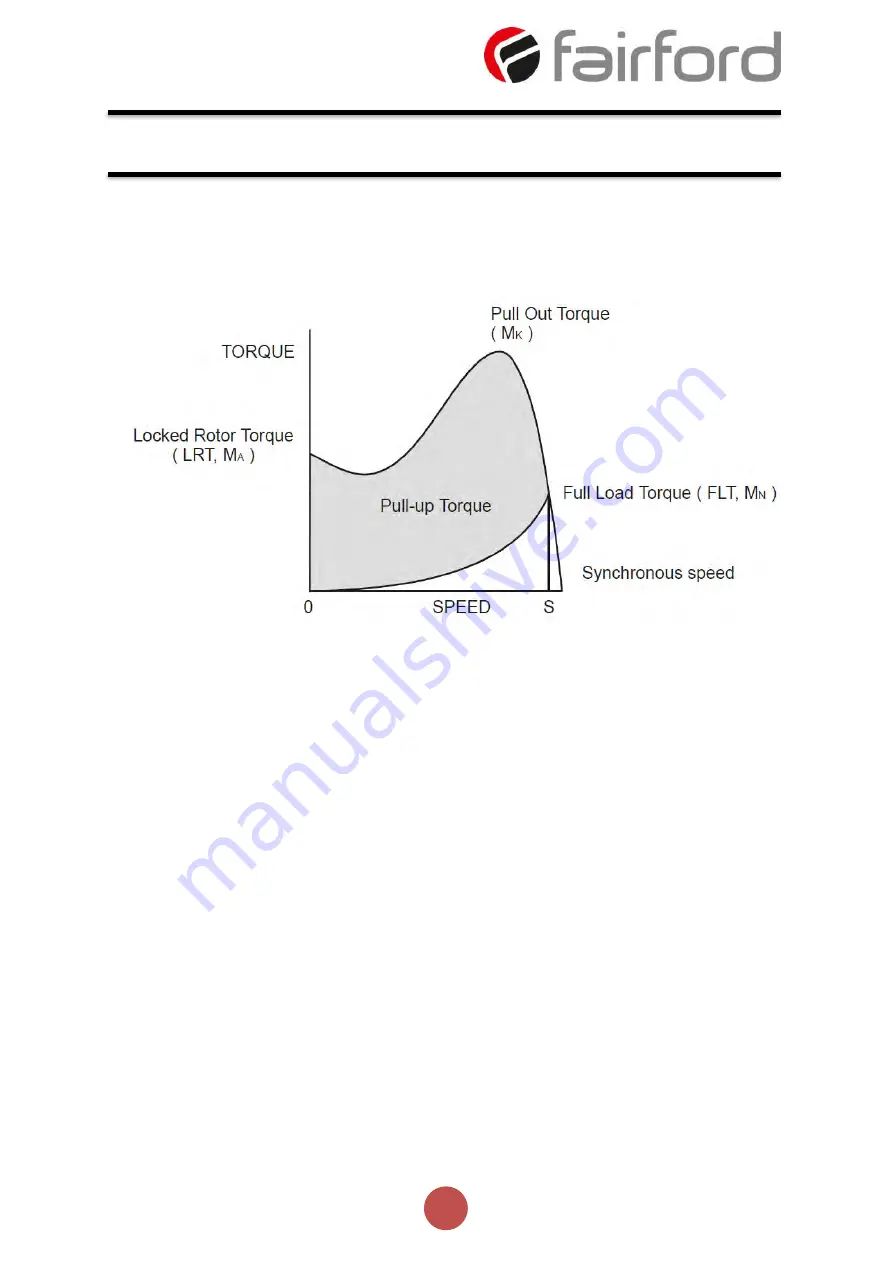
104
agility
TM
Series Soft Start User Manual
MAN-AGY-001. Version 04. 21/09/2018
The Induction Motor (continued)
The acceleration of a motor-load system is caused by the difference between the developed
torque (motor) and the absorbed torque (load), and is shown by the shaded area in the next
figure:
Torque/Speed Curve
–
Accelerating Torque
Obviously, the larger the difference, the faster the acceleration and the quicker full speed is
reached - and, coincidentally, the greater the stresses experienced by the supply and drive
systems during the acceleration process
. An “ideal” start would accelerate the load with just
sufficient force to reach full speed smoothly in a reasonable time, and with minimum stress to the
supply and drive mechanisms.
Broadly speaking, the motor speed/torque characteristic is controlled by the rotor resistance - a
motor with high rotor resistance can generate it’s peak torque (pull
-out torque) at standstill giving
the high break-away torque characteristic, which reduces steadily as the speed increases and
becoming zero at synchronous speed. At the other end of the scale, a motor with a very low rotor
resistance will produce a low starting torque but will generate its peak torque closer to the
synchronous speed. Consequently, this type of motor runs at full power with higher operating
efficiency and low slip speed. It is possible to combine the twin
requirements of high starting torque and efficient full-speed operation within a single motor by
techniques such as double-cage or deep bar design, and this, usually, is the motor characteristic
chosen for lifting and hoisting applications:
However, most induction motors are designed to have a “standard” characteristic that provides a
compromise between starting torque and operating efficiency. To summarise, an induction motor
will only start and accelerate when it produces more torque than the connected load absorbs.
This is true for all speeds - including standstill and full speed.
Applications (continued)