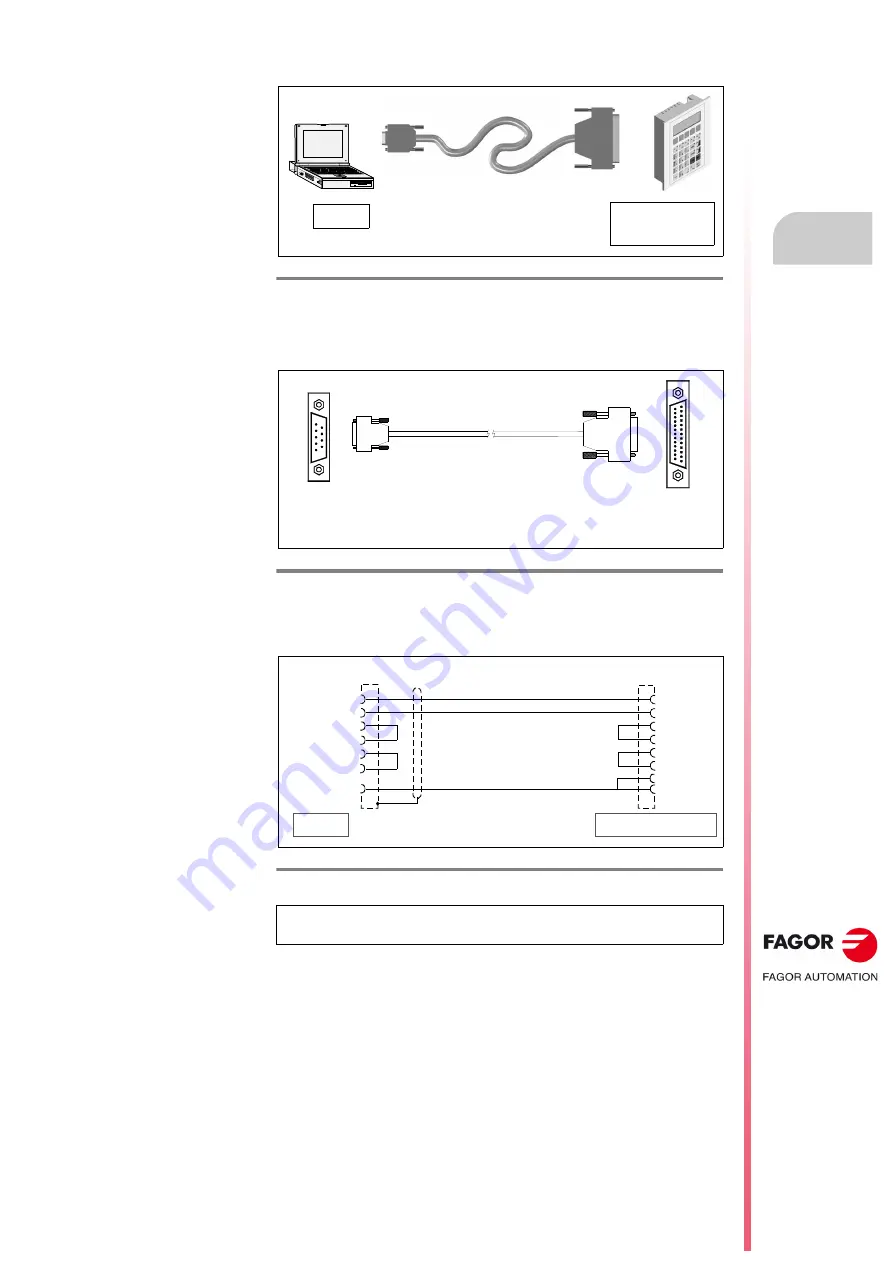
Cables
7.
Ref.1912
· 255 ·
DDS
HARDWARE
PC-VT connection using an RS-232 cable ·without adapter·
The connection cable when not using the adapter RS232/RS422 BE has
the following connectors at its ends:
The connection is:
F. H7/11
RS-232 serial line connection between a PC and VT from ESA (without
adapter).
F. H7/12
A.
Connector of the RS-232 cable for direct connection to the PC.
B.
Connector of the RS-232 cable for direct connection to the VT panel from
ESA.
F. H7/13
RS-232 connection between PC and VT without adapter.
NOTE.
See the previous section for further information on the pinout of the
25-pin connector of the MSP port of the VT panel from ESA.
9-pin Sub-D,
type female
connector
RS-232 cable
25-pin Sub-D,
type male
connector
to the VT
panel (ESA)
to PC
5
1
6
9
13
1
25
14
A
RS-232 cable
to PC
(Sub-D, F9)
B
to the VT panel (ESA)
(Sub-D, M25)
These two connectors are located at both
ends of the RS-232 cable when connecting without the adapter.
8
6
4
3
2
5
Pin
4
15
3
2
5
Pin
CTS
DSR
DTR
TxD
RxD
RTS
Signal
CHASSIS
CTS
TRS
RxD
TxD
GND
Signal
18
25
7
7
Maximum length: 15 meters
To PC
To the VT panel (ESA)
Sub-D, F9
Sub-D, M25
Summary of Contents for DDS Series
Page 1: ...DRIVE DDS Hardware manual Ref 1912...
Page 6: ...6 Ref 1912 DDS HARDWARE 6 I This page intentionally left blank...
Page 9: ......
Page 10: ......
Page 11: ......
Page 12: ......
Page 16: ...Ref 1912 DDS HARDWARE 16...
Page 20: ...Ref 1912 DDS HARDWARE 20...
Page 179: ...3 Drives Ref 1912 179 DDS HARDWARE...
Page 180: ...3 Drives Ref 1912 DDS HARDWARE 180...
Page 200: ...4 AUXILIARY MODULES Auxiliary modules Ref 1912 DDS HARDWARE 200...
Page 260: ...7 Cables Ref 1912 DDS HARDWARE 260...
Page 397: ...Sales models 12 Ref 1912 397 DDS HARDWARE 12 9 Order example F H12 21 Order example...
Page 404: ...13 Compatibility Ref 1912 DDS HARDWARE 404...
Page 405: ......