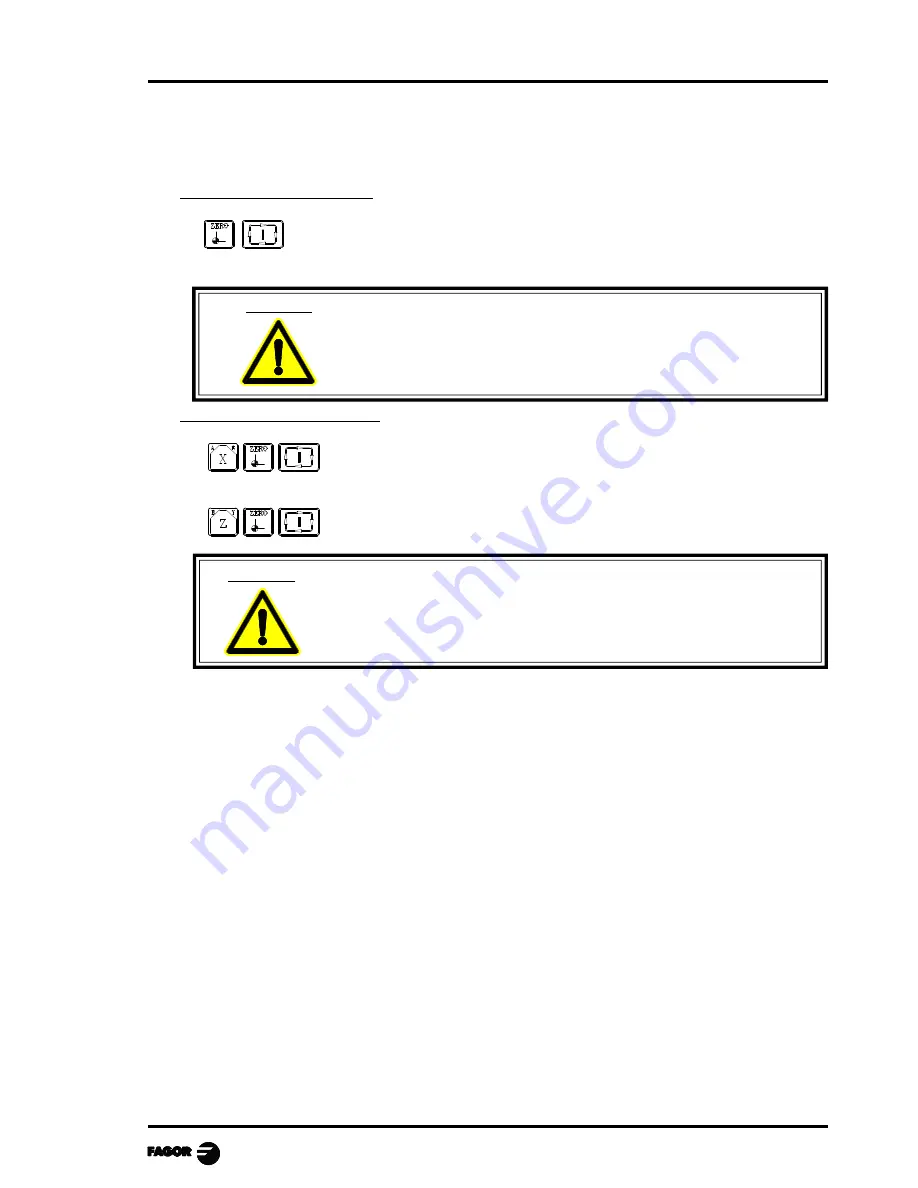
Chapter 2 - page 7
MCO-TCO work mode
2.3 HOME SEARCH (MACHINE REFERENCE ZERO)
Home search can be done in 2 ways:
Home search on all the axes
The CNC will execute the machine reference zero routine defined by the
manufacture in the general machine parameter P34 (REFPSUB).
Warning:
The CNC saves the part zero or zero offset that is active at the time.
If no home searching subroutine is defined, the CNC will display the
relevant error message.
Home search on a single axis
Carries out the home search on the X axis
Carries out the home search on the Z axis
Warning:
The CNC does not save the part zero or zero offset that is active at the
time and assumes as new part zero the position taken by machine
reference zero (home).