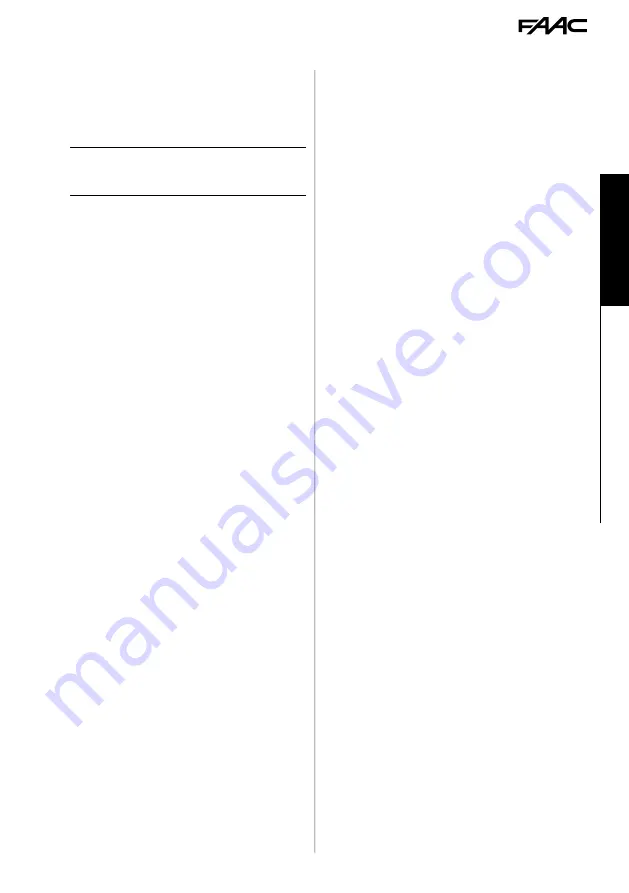
B614
9
732998 - Rev.A
Tr
ansla
tion of the orig
inal instruc
tions
ENGLISH
3. B614
3.1 INTENDED USE
The B614 barriers are designed for vehicular access
control in residential buildings/apartment complexes.
To move the beam manually, follow the instructions
for manual functioning.
!
Any other use that is not expressly specified in these
instructions is prohibited and could affect the integri-
ty of the product and/or represent a source of danger.
3.2 LIMITATIONS OF USE
Comply with the limitations on frequency of use listed
in the technical data section.
The B614 requires the use of a specific FAAC beam
that conforms to the dimensions indicated in this
manual. Only the FAAC accessories indicated in this
manual should be installed on the beam.
The B614 requires the use of a FAAC spring that is
adequate for counterbalancing the weight of the beam
and the relative accessories.
The barriers with exclusively vehicle access control
must be fitted with suitable visible signs prohibiting
foot traffic. A separate route for foot traffic outside
the range of the beam must be provided and properly
indicated.
If foot traffic cannot be ruled out, the barrier falls within
the scope of the EN 12453 standard.
The presence of weather conditions such as snow, ice
and strong wind, even occasional, could affect the
correct operation of the automation, the integrity of
the components and be a potential source of danger
(see § Emergency use). The limitations of use of the
B614 in wind is equivalent to grade 10 on the Beaufort
Scale (max. speed: 102 km/h).
The installation must be visible during the day and
at night. If it is not, appropriate solutions must be
provided to make the fixed and moving parts visible
(light kit on the beam).
The B614 must be connected to a FAAC electronic
board as indicated in this manual ( Technical cha-
racteristics).
Implementing the automation requires the installa-
tion of the necessary safety devices, identified by the
installer through an appropriate risk assessment of
the installation site.