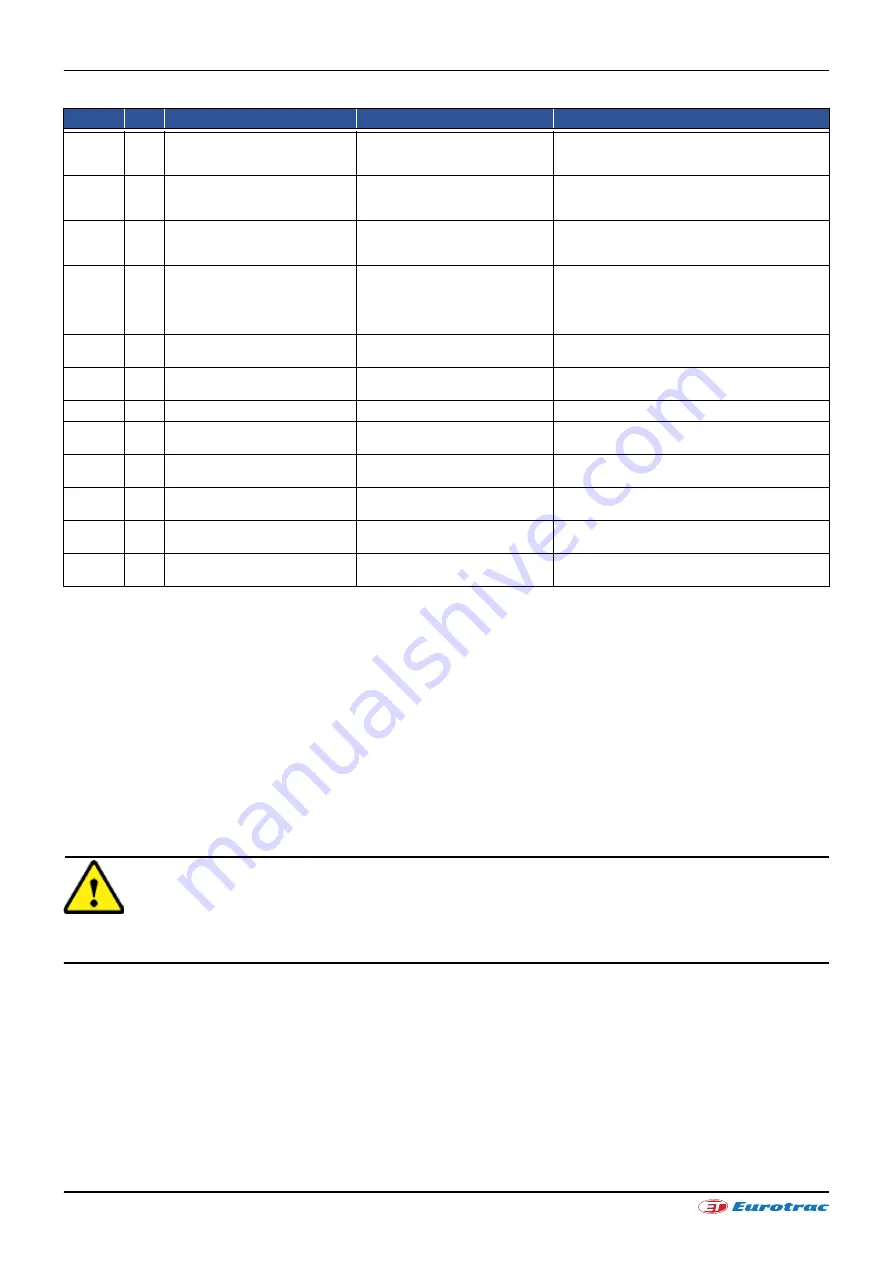
Page 63/81
April 2021
W11 - W12S -W12F - W13F - T13F | Operation manual
Rear Axle and Reduction Gear Box
Check oil level in the rear axle and gear reduction box and add oil, if needed.
Maintenance interval:
•
Check the oil level every 400 operating hours. For this purpose, the loader must be standing on even ground
and should have been inoperative for approx. 10 min before checking. The oil must be up to the screw "A". Top
up with oil as necessary.
•
Change the oil every 800 operating hours, for the first time after 50 operating hours. Run the gear until warm
and then drain the oil via plug "B". Top up with fresh oil in the specified quantity and grade.
•
Visual inspection for possible leakage should be carried out on a daily basis.
Dispose of the waste oil in accordance with statutory regulations.
CAUTION
Using other lubricants can lead to significant noises in the self-locking differential and changes in the locking values.
In the event of damage, we retain the right to analyse the oil.
523589
17
Proprietary
During regeneration mode, Engine
warm-up condition is not satisfied
(coolant temp. is low)
During parked active regeneration mode
523590
16
Proprietary
Time out error: regeneration
incomplete due to low temperature
of DPF
• During parked active regeneration mode
• Coolant temp. is 50 °C (122 °F) or more
3936
2
Aftertreatment Diesel Particulate
Filter System
Loss of function of DPF
• Barometric pressure sensor is normal
• Exhaust temperature sensor T0 is normal
• Differential Pressure sensor is normal
523599
0
Proprietary
All exhaust temp. sensor failure
simultaneously
• Engine speed is 1400 rpm or more
• Quantity of injection is 5 mm3/st or more
• Coolant temp. is 50 °C (122 °F) or more: continues
longer than 300 sec
• 100 seconds after starting
523601
0
Proprietary
Exhaust gas temperature sensor
0, 1, 2 output
Battery voltage is normal
523602
0
Proprietary
Time interval from the end time to
the start time of the regeneration
• Battery voltage is normal
• Key switch is ON
523603
15
Proprietary
Coolant temp.
Coolant temp. sensor is normal
523578
2
Proprietary
No communication with EGR
• Battery voltage is normal
• Starter switch signal is not activated
523591
2
Proprietary
CAN_CCVS communication stopping
• Battery voltage is normal
• Starter switch signal is not activated
523592
2
Proprietary
CAN_CM1 communication stopping
• Battery voltage is normal
• Starter switch signal is not activated
523595
2
Proprietary
CAN_ETC5 communication stopping
• Battery voltage is normal
• Starter switch signal is not activated
523596
2
Proprietary
CAN_TSC1 communication stopping
• Battery voltage is normal
• Starter switch signal is not activated
Code
Summary of Contents for T13-F
Page 45: ...Page 45 81 April 2021 W11 W12S W12F W13F T13F Operation manual...
Page 46: ...Page 46 81 April 2021 W11 W12S W12F W13F T13F Operation manual...
Page 47: ...Page 47 81 April 2021 W11 W12S W12F W13F T13F Operation manual...
Page 73: ...Page 73 81 April 2021 W11 W12S W12F W13F T13F Operation manual Hydraulic diagram W12S...
Page 74: ...Page 74 81 April 2021 W11 W12S W12F W13F T13F Operation manual Hydraulic diagram W12F W13F...
Page 75: ...Page 75 81 April 2021 W11 W12S W12F W13F T13F Operation manual Hydraulic diagram T13F...
Page 77: ...Page 77 81 April 2021 W11 W12S W12F W13F T13F Operation manual Electric diagram W12F W13F T13F...
Page 78: ...Page 78 81 April 2021 W11 W12S W12F W13F T13F Operation manual...
Page 79: ...Page 79 81 April 2021 W11 W12S W12F W13F T13F Operation manual...