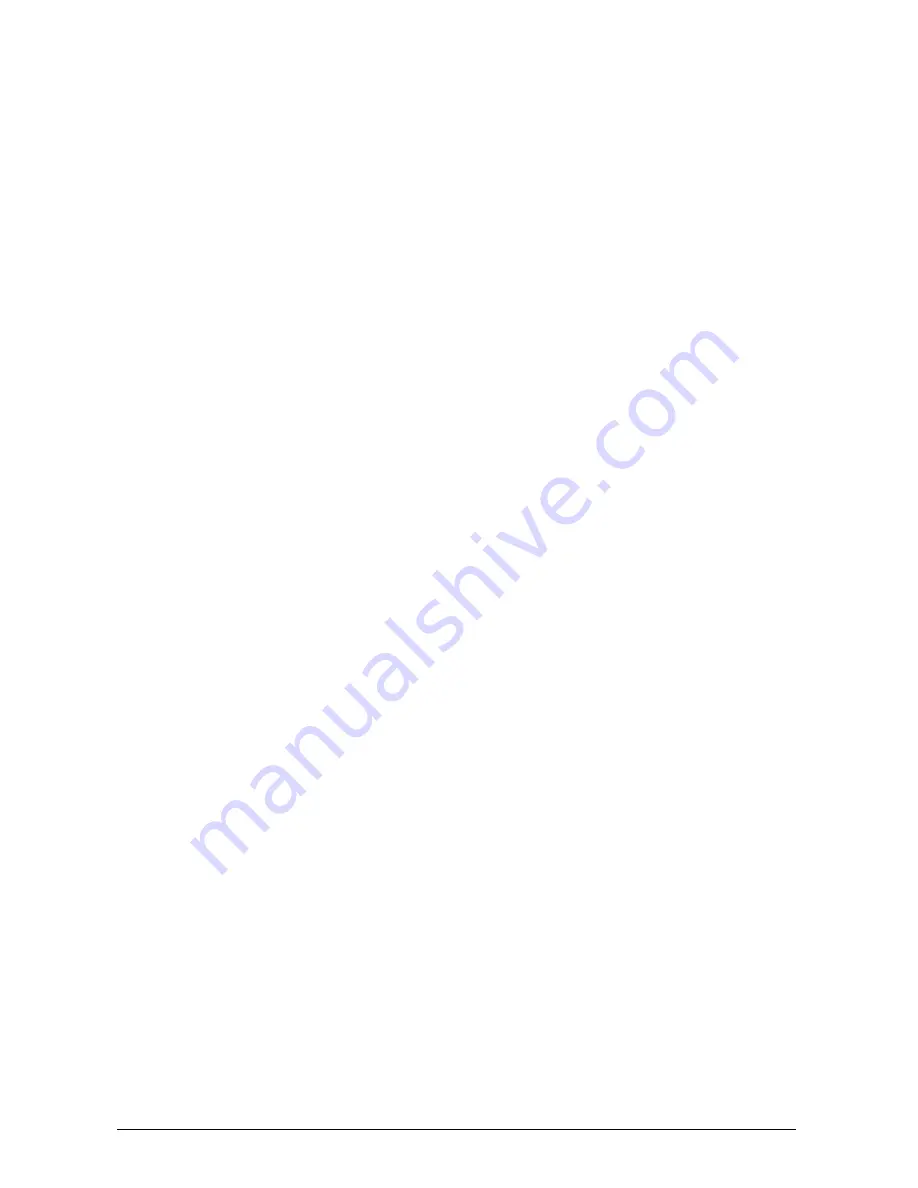
4 - 24
INTERACTION WITH EARTH-FAULT MONITORING SYSTEMS AND SAFETY CONSIDERATIONS
Due to the EMC filter internal capacitors between phase and earth, on initial connection of the AC supply a pulse of current
will flow in the earth. This has been minimised in the recommended EMC filters, but may still trip out any RCD (Resident
Current Detector) in the earth system. In addition high frequency and DC components of earth leakage currents will flow
under normal operating conditions. Under certain fault conditions, larger DC protective earth currents may flow. The pro-
tective function of some RCDs cannot be guaranteed under such operating conditions. Eurotherm Drives do not recommend
the use of RCDs, but where their use is mandatory, they should be capable of correct operation with DC and AC protective
earth currents (such as type B RCDs as in amendment 2 of IEC755) and have adjustable trip amplitude and time
characteristics, to prevent nuisance tripping on initial power connection. RCDs used with 590 drive modules and other
similar equipment are
not suitable for personnel protection
. Another means of providing personal safety must be
provided for, see EN50178/VDE0160.
MINIMISING RADIATED EMISSIONS
All 590 drive modules can be made to comply with the most stringent radiated emission limits of EN55011 (1991) Class B
by simply mounting inside an enclosure with 10 dB attenuation between 30 and 100 MHz (which would typically be the
attenuation provided by a metal cabinet with no aperture greater than 0.15m) and screening any control and signal cabling
outside of the enclosure. The control and signal cables should be terminated at the entrance to the enclosure. Outside of the
enclosure all cables must be screened. Inside the enclosure the radiated magnetic and electric fields will be high, due to
proximity, and any components fitted inside the enclosure must be sufficiently immune. Remember that the EN55011
radiated emission measurements are made between 30 MHz and 1 GHz in the far field, at a distance of between 10m and 30
m. No limits are specified lower than 30 MHz, or in close proximity. Emissions from individual components tend to be
additive.
The cable between the enclosure and the motor must be screened or armoured (both field and armature) and should also
contain the motor protective earth connection. The screen/armour must be earthed at both ends by connecting it to both the
motor frame and the entrance to the cubicle, ideally in 360
°
termination's via cable glands (to meet the most stringent
emission requirements). Screen to earth connections via 360
°
bonding is 75% more effective than earthing via pigtails
(Note some motor gland boxes and conduit glands are made of plastic, if this is the case then braid must be connected
between the screen and the chassis, in addition at the motor end ensure that the screen is electrically connected to the motor
frame since some terminal boxes are insulated from the frame by gasket/paint). Often the screens are terminated on a power
screen rail at the entrance to the enclosure using ‘u’ clips to achieve a near 360
o
screen band. The integrity of the screen
must be maintained over the entire length of the cable between the enclosure and motor. If the cable is broken to insert
terminals, contactors, chokes, fuses etc., then the screen must be connected over the shortest possible distance. Note some
hazardous area installations may preclude direct earthing at both ends of the screen, in this case earth the other end via a 1
µ
F, 50VAC capacitor. The motor protective earth should be connected to the drive module motor protective earth
connection.
If a shielded cable is not available, lay unshielded motor cables in a metal conduit which will act as a shield. The conduit
must be continuous with a direct electrical contact to the drive module and motor housing. If links are necessary, use braid
with a minimum cross sectional area of 10 mm
2
.
Safety earthing always takes precedence over EMC earthing.
The use of screened cable without an EMC filter is not recommended, as line-conducted interference will increase
substantially and the capacitive coupling of the output cable to earth will result in high earth-leakage currents.
To ensure the correct operation of the 590 drive module, some control and signal cables (encoder, all analogue inputs and
communications) have to be screened back to the drive terminals inside the enclosure. The screen integrity must be
continuous right back to the drive if not connected to the cubicle. Always minimise the length of screen stripped back to
make this connection. The screen should only be connected at the drive end. If high frequency noise is still a problem, earth
at the non drive end via a 0.1
µ
F capacitor.
SCREENING AND EARTHING WHEN MOUNTED IN AN ENCLOSURE
Make sure the requirements of EN60204 are adhered to with electrical equipment for machines. Satisfactory EMC
performance is only achievable when the 590 drive module, filter, choke and associated equipment is mounted on a
conducting metal mounting panel. Beware of constructions using insulating mounting panels or undefined mounting
structures A single point earthing strategy should be followed as closely as possible for a single drive module mounted in
an enclosure as shown in figure 4-6. The protective earth connection (PE) to the motor must run inside the screened cable
between the motor and 590 drive module, where it is to be connected near to the motor protective earth terminal on the
drive module as shown in figure 4-6. (Note in accordance with EN60204 only one protective earth conductor is permitted at
each earth terminal contacting point). Local wiring regulations may require the protective-earth connection of the motor to
be connected locally but this will not cause shielding problems due to the relatively high RF impedance of the local earth
connection.
This manual was downloaded on www.sdsdrives.com
+44 (0)117 938 1800 - [email protected]
Summary of Contents for 590A SERIES
Page 22: ...This manual was downloaded on www sdsdrives com 44 0 117 938 1800 info sdsdrives com ...
Page 23: ...This manual was downloaded on www sdsdrives com 44 0 117 938 1800 info sdsdrives com ...
Page 24: ...This manual was downloaded on www sdsdrives com 44 0 117 938 1800 info sdsdrives com ...
Page 25: ...This manual was downloaded on www sdsdrives com 44 0 117 938 1800 info sdsdrives com ...
Page 26: ...This manual was downloaded on www sdsdrives com 44 0 117 938 1800 info sdsdrives com ...
Page 27: ...This manual was downloaded on www sdsdrives com 44 0 117 938 1800 info sdsdrives com ...
Page 28: ...This manual was downloaded on www sdsdrives com 44 0 117 938 1800 info sdsdrives com ...
Page 29: ...This manual was downloaded on www sdsdrives com 44 0 117 938 1800 info sdsdrives com ...
Page 30: ...This manual was downloaded on www sdsdrives com 44 0 117 938 1800 info sdsdrives com ...
Page 31: ...This manual was downloaded on www sdsdrives com 44 0 117 938 1800 info sdsdrives com ...
Page 32: ...This manual was downloaded on www sdsdrives com 44 0 117 938 1800 info sdsdrives com ...
Page 33: ...This manual was downloaded on www sdsdrives com 44 0 117 938 1800 info sdsdrives com ...
Page 55: ...This manual was downloaded on www sdsdrives com 44 0 117 938 1800 info sdsdrives com ...
Page 56: ...This manual was downloaded on www sdsdrives com 44 0 117 938 1800 info sdsdrives com ...
Page 66: ...This manual was downloaded on www sdsdrives com 44 0 117 938 1800 info sdsdrives com ...
Page 68: ...This manual was downloaded on www sdsdrives com 44 0 117 938 1800 info sdsdrives com ...
Page 82: ...This manual was downloaded on www sdsdrives com 44 0 117 938 1800 info sdsdrives com ...
Page 83: ...This manual was downloaded on www sdsdrives com 44 0 117 938 1800 info sdsdrives com ...
Page 84: ...This manual was downloaded on www sdsdrives com 44 0 117 938 1800 info sdsdrives com ...
Page 97: ...This manual was downloaded on www sdsdrives com 44 0 117 938 1800 info sdsdrives com ...
Page 98: ...This manual was downloaded on www sdsdrives com 44 0 117 938 1800 info sdsdrives com ...
Page 99: ...This manual was downloaded on www sdsdrives com 44 0 117 938 1800 info sdsdrives com ...
Page 100: ...This manual was downloaded on www sdsdrives com 44 0 117 938 1800 info sdsdrives com ...
Page 101: ...This manual was downloaded on www sdsdrives com 44 0 117 938 1800 info sdsdrives com ...
Page 102: ...This manual was downloaded on www sdsdrives com 44 0 117 938 1800 info sdsdrives com ...
Page 103: ...This manual was downloaded on www sdsdrives com 44 0 117 938 1800 info sdsdrives com ...
Page 104: ...This manual was downloaded on www sdsdrives com 44 0 117 938 1800 info sdsdrives com ...
Page 105: ...This manual was downloaded on www sdsdrives com 44 0 117 938 1800 info sdsdrives com ...
Page 106: ...This manual was downloaded on www sdsdrives com 44 0 117 938 1800 info sdsdrives com ...
Page 107: ...This manual was downloaded on www sdsdrives com 44 0 117 938 1800 info sdsdrives com ...
Page 108: ...This manual was downloaded on www sdsdrives com 44 0 117 938 1800 info sdsdrives com ...