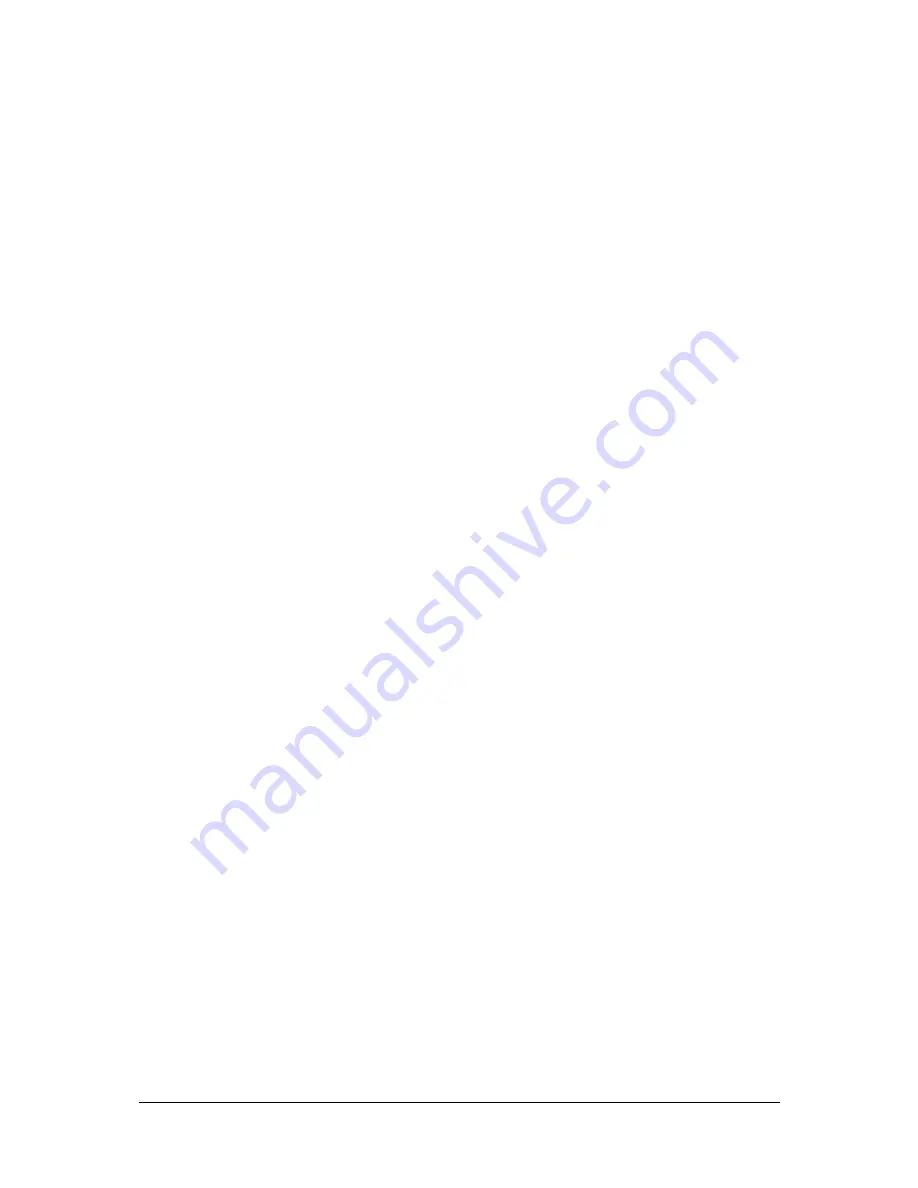
6 - 3
The speed feedback is scaled within the drive using the calibration switches for coarse adjustment:
S2 - 0/100 Volts
S3 - 0/ 90 Volts
S4 - 0/ 9 Volts
This allows an adjustment calibration factor for full speed up to 199 Volts. P10 on the preset board will allow
fine adjustment of the top speed.
If tach voltages exceed 200V then external resistors should be added.
The drive also contains protective circuitry such that in the event of loss of speed feedback (i.e. tach failure) the
motor speed will not rise excessively. This action occurs when the speed feedback term is less than 0.5% to 4%,
(adjustable using trimpot. P4 on the Preset Board) and limits the maximum output voltage of the drive. This
condition still allows rated armature current to be produced at low speed and when the speed feedback term
exceeds this level, (confirming tach operation) the limit is removed and normal control action is resumed.
Armature voltage feedback is available by using the armature voltage isolation unit 5590
ZERO SPEED SENSING
When the speed feedback signal is less than 0.5% to 4% (as set by P4) the Zero Speed Relay Driver is energised
such that external terminal 36 s24V to drive an external relay.
SPEED ERROR
The combined setpoints are compared with the tach feedback signal on an error amplifier (Diagnostic 17) such
that the Speed Signal is always made equal to the Total Setpoint. An offset trimpot P3 is available on the Preset
Board to allow the offsets to be reduced to zero. It is not possible to achieve zero speed on demand of a zero
speed setpoint without the motor shaft creeping round at a very low speed however accurately the offset is
trimmed. However, if absolute zero speed is required, then operating Option Switch S8/2 will enable the
Standstill Logic. This will operate when the Total Setpoint is below 0.5% and the motor speed is below 4% -
0.5% as set by trimpot P4. In this condition a quench action is employed and no firing pulses are applied to the
thyristor bridge. If however the Total Setpoint or the speed feedback exceed the thresholds the Standstill Logic
will be disabled, the quench action removed and firing pulses are again applied to the thyristor bridge, thus
allowing armature current to flow.
The gain of the Error Amplifier is adjustable (by P5 on the Preset Board) over a 10 to 1 range to provide control
of the stability and dynamic performance of the drive. This adjustment does no affect the steady state speed
holding accuracy of the drive.
CURRENT DEMAND
The error signal is passed through a 2-Term (Proportional plus Integral) amplifier (Diagnostic 18) which ensures
very high DC loop gain, thus achieving accurate steady state speed control and good dynamic performance by
correctly optimising the low and high frequency gain of the system for small and large signals. The Integral time
constant is adjustable over a 10 to 1 range using trimpot P6 on the Preset Board. The output of this 2-Term
amplifier becomes the armature Current Demand signal under normal condition and is also available on external
terminal 19. However it may be isolated from the following stages by a solid state switch when terminal 18
(Diagnostic 19) is connected to 0V, (otherwise this terminal is left open circuit). The auxiliary current input
(terminal 20), diagnostic 20 can also provide the Current Demand signal or be algebraically added to the 2 Term
output. via a solid state switch. If this facility is required terminal 21 (Diagnostic 21) must be connected to 0V,
otherwise this terminal is left open circuit.
MAIN CURRENT LIMIT
The Armature Current Demand signal then controls the magnitude of armature current and hence clamping the
maximum excursion of this signal limits the maximum armature current that can flow. The reference for the
clamp is taken from trimpot P7 on the Preset Board. The top of this potentiometer is available externally at
terminal 23 and is normally connected to terminal 24 (+10V), thus +10V as measured on the wiper of P7
(Diagnostic 24) corresponds to 200% armature current can be programmed according to some other control
strategy.
This manual was downloaded on www.sdsdrives.com
+44 (0)117 938 1800 - [email protected]
Summary of Contents for 590A SERIES
Page 22: ...This manual was downloaded on www sdsdrives com 44 0 117 938 1800 info sdsdrives com ...
Page 23: ...This manual was downloaded on www sdsdrives com 44 0 117 938 1800 info sdsdrives com ...
Page 24: ...This manual was downloaded on www sdsdrives com 44 0 117 938 1800 info sdsdrives com ...
Page 25: ...This manual was downloaded on www sdsdrives com 44 0 117 938 1800 info sdsdrives com ...
Page 26: ...This manual was downloaded on www sdsdrives com 44 0 117 938 1800 info sdsdrives com ...
Page 27: ...This manual was downloaded on www sdsdrives com 44 0 117 938 1800 info sdsdrives com ...
Page 28: ...This manual was downloaded on www sdsdrives com 44 0 117 938 1800 info sdsdrives com ...
Page 29: ...This manual was downloaded on www sdsdrives com 44 0 117 938 1800 info sdsdrives com ...
Page 30: ...This manual was downloaded on www sdsdrives com 44 0 117 938 1800 info sdsdrives com ...
Page 31: ...This manual was downloaded on www sdsdrives com 44 0 117 938 1800 info sdsdrives com ...
Page 32: ...This manual was downloaded on www sdsdrives com 44 0 117 938 1800 info sdsdrives com ...
Page 33: ...This manual was downloaded on www sdsdrives com 44 0 117 938 1800 info sdsdrives com ...
Page 55: ...This manual was downloaded on www sdsdrives com 44 0 117 938 1800 info sdsdrives com ...
Page 56: ...This manual was downloaded on www sdsdrives com 44 0 117 938 1800 info sdsdrives com ...
Page 66: ...This manual was downloaded on www sdsdrives com 44 0 117 938 1800 info sdsdrives com ...
Page 68: ...This manual was downloaded on www sdsdrives com 44 0 117 938 1800 info sdsdrives com ...
Page 82: ...This manual was downloaded on www sdsdrives com 44 0 117 938 1800 info sdsdrives com ...
Page 83: ...This manual was downloaded on www sdsdrives com 44 0 117 938 1800 info sdsdrives com ...
Page 84: ...This manual was downloaded on www sdsdrives com 44 0 117 938 1800 info sdsdrives com ...
Page 97: ...This manual was downloaded on www sdsdrives com 44 0 117 938 1800 info sdsdrives com ...
Page 98: ...This manual was downloaded on www sdsdrives com 44 0 117 938 1800 info sdsdrives com ...
Page 99: ...This manual was downloaded on www sdsdrives com 44 0 117 938 1800 info sdsdrives com ...
Page 100: ...This manual was downloaded on www sdsdrives com 44 0 117 938 1800 info sdsdrives com ...
Page 101: ...This manual was downloaded on www sdsdrives com 44 0 117 938 1800 info sdsdrives com ...
Page 102: ...This manual was downloaded on www sdsdrives com 44 0 117 938 1800 info sdsdrives com ...
Page 103: ...This manual was downloaded on www sdsdrives com 44 0 117 938 1800 info sdsdrives com ...
Page 104: ...This manual was downloaded on www sdsdrives com 44 0 117 938 1800 info sdsdrives com ...
Page 105: ...This manual was downloaded on www sdsdrives com 44 0 117 938 1800 info sdsdrives com ...
Page 106: ...This manual was downloaded on www sdsdrives com 44 0 117 938 1800 info sdsdrives com ...
Page 107: ...This manual was downloaded on www sdsdrives com 44 0 117 938 1800 info sdsdrives com ...
Page 108: ...This manual was downloaded on www sdsdrives com 44 0 117 938 1800 info sdsdrives com ...