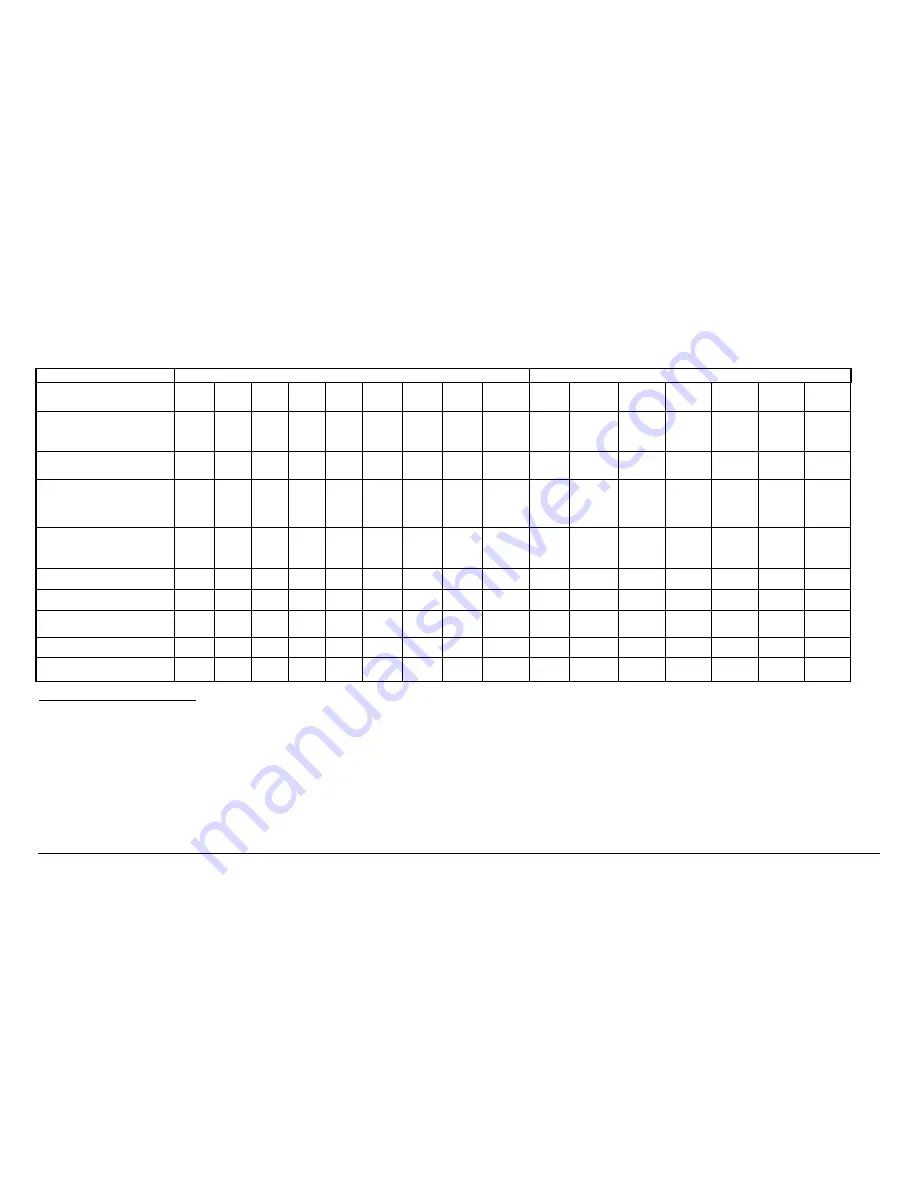
2 - 3
2.2 OUTPUT RATINGS
2.2.1 ARMATURE RATING
590/1
598/9
Output Current Ratings
(Armature)
1
35A
70A
110A
150A
180A
270A
360A
450A
720A
950A
1100A
1388A
1600A
1800A
2300A
2800A
Nominal Power Rating @
460V DC Assuming 95%
Motor Efficiency
15KW
(20HP)
30KW
(40HP)
45KW
(60HP)
60KW
(80HP)
75KW
(100HP)
110KW
(150HP)
150KW
(200HP)
190KW
(250HP)
300KW
(400HP)
395KW
(530HP)
455KW
(610HP)
575KW
(770HP)
660KW
(880HP)
745KW
(1000HP)
950KW
(1275HP)
1150KW
(1550HP)
Maximum Rating
Ambient
2
45°C
45°C
35°C
35°C
35°C
35°C
35°C
35°C
35°C
35°C
35°C
35°C
35°C
35°C
35°C
35°C
Cooling:
Forced(F)/Natural(N) Fan:
Integral(I)/Separate(S)
N
-
N
-
F
I
F
I
F
I
F
I
F
I
F
S 3
F
S
F
S
F
S
F
S
F
S
F
S
F
S
F
S
Overload Capacity
Available (Armature
Current)
4
Y
Y
Y
Y
Y
Y
Y
Y
N
Y
Y
Y
Y
Y
Y
Y
Field Current Rating
10A
10A
10A
10A
10A
10A
20A
20A
20A
30A
30A
30A
30A
30A
30A
30A
Maximum Supply Voltage
500V
500V
500V
500V
500V
500V
500V
500V
500V
660V
660V
660V
660V
660V
550V5
550V
8
Maximum Field Supply
Voltage
500V
500V
500V
500V
500V
500V
500V
500V
500V
500V
500V
500V
500V
500V
500V
500V
Power Loss
105W
210W
330W
450W
540W
710W
1080W
1350W
2160W
2850W
3300W
4164W
4800W
5400W
6900W
8400W
Installation Drawing HG:
055805 055805 055806 055806 386968 055807 057208 057209 0574496 057829
7
057829
7
057829
7
0578297
057829
7
057829
7
057829
7
1
Altitude derating, nominal sea level to 500 metres, derate above 500 metres at 1% per 200 metres up to maximum of 5,000 metres.
2
Derate linearly at 1% per degree centigrade for temperature exceeding the maximum rating ambient. Maximum operating ambient is 55°C.
3
A lower current version limited to 360Amps is available with an integral fan (HG057208).
4
The standard overload capacity available is 200% for 10 seconds, 150% for 30 seconds. The 720 Amp Chassis has no overload capacity at maximum current, whereas at output currents less
than 650 Amps overload capacity is as normal.
5
External Stack assemblies at 660V are not available above 2000 Amps without reference to Eurotherm Drives Internal Sales Department.
6
For Installation Drawings for 720A Stock Assembly see: HG049669 Standard Mounting / HG054248 Bracket Mounting.
7
Installation Drawings for External Stack Thyristor assemblies available on application to Eurotherm Drives Engineering Department.
This manual was downloaded on www.sdsdrives.com
+44 (0)117 938 1800 - [email protected]
Summary of Contents for 590A SERIES
Page 22: ...This manual was downloaded on www sdsdrives com 44 0 117 938 1800 info sdsdrives com ...
Page 23: ...This manual was downloaded on www sdsdrives com 44 0 117 938 1800 info sdsdrives com ...
Page 24: ...This manual was downloaded on www sdsdrives com 44 0 117 938 1800 info sdsdrives com ...
Page 25: ...This manual was downloaded on www sdsdrives com 44 0 117 938 1800 info sdsdrives com ...
Page 26: ...This manual was downloaded on www sdsdrives com 44 0 117 938 1800 info sdsdrives com ...
Page 27: ...This manual was downloaded on www sdsdrives com 44 0 117 938 1800 info sdsdrives com ...
Page 28: ...This manual was downloaded on www sdsdrives com 44 0 117 938 1800 info sdsdrives com ...
Page 29: ...This manual was downloaded on www sdsdrives com 44 0 117 938 1800 info sdsdrives com ...
Page 30: ...This manual was downloaded on www sdsdrives com 44 0 117 938 1800 info sdsdrives com ...
Page 31: ...This manual was downloaded on www sdsdrives com 44 0 117 938 1800 info sdsdrives com ...
Page 32: ...This manual was downloaded on www sdsdrives com 44 0 117 938 1800 info sdsdrives com ...
Page 33: ...This manual was downloaded on www sdsdrives com 44 0 117 938 1800 info sdsdrives com ...
Page 55: ...This manual was downloaded on www sdsdrives com 44 0 117 938 1800 info sdsdrives com ...
Page 56: ...This manual was downloaded on www sdsdrives com 44 0 117 938 1800 info sdsdrives com ...
Page 66: ...This manual was downloaded on www sdsdrives com 44 0 117 938 1800 info sdsdrives com ...
Page 68: ...This manual was downloaded on www sdsdrives com 44 0 117 938 1800 info sdsdrives com ...
Page 82: ...This manual was downloaded on www sdsdrives com 44 0 117 938 1800 info sdsdrives com ...
Page 83: ...This manual was downloaded on www sdsdrives com 44 0 117 938 1800 info sdsdrives com ...
Page 84: ...This manual was downloaded on www sdsdrives com 44 0 117 938 1800 info sdsdrives com ...
Page 97: ...This manual was downloaded on www sdsdrives com 44 0 117 938 1800 info sdsdrives com ...
Page 98: ...This manual was downloaded on www sdsdrives com 44 0 117 938 1800 info sdsdrives com ...
Page 99: ...This manual was downloaded on www sdsdrives com 44 0 117 938 1800 info sdsdrives com ...
Page 100: ...This manual was downloaded on www sdsdrives com 44 0 117 938 1800 info sdsdrives com ...
Page 101: ...This manual was downloaded on www sdsdrives com 44 0 117 938 1800 info sdsdrives com ...
Page 102: ...This manual was downloaded on www sdsdrives com 44 0 117 938 1800 info sdsdrives com ...
Page 103: ...This manual was downloaded on www sdsdrives com 44 0 117 938 1800 info sdsdrives com ...
Page 104: ...This manual was downloaded on www sdsdrives com 44 0 117 938 1800 info sdsdrives com ...
Page 105: ...This manual was downloaded on www sdsdrives com 44 0 117 938 1800 info sdsdrives com ...
Page 106: ...This manual was downloaded on www sdsdrives com 44 0 117 938 1800 info sdsdrives com ...
Page 107: ...This manual was downloaded on www sdsdrives com 44 0 117 938 1800 info sdsdrives com ...
Page 108: ...This manual was downloaded on www sdsdrives com 44 0 117 938 1800 info sdsdrives com ...